Home » Granulation Line
Granulation Line
Senieer® closed granulation line for production of granules, capsules, tablets dosage forms
Include wet granulation line and dry granulation line
Customize different granulation lines solutions as per your process requirements
Introduction Of Granulation Line
Senieer granulation lines are engineered to optimize batch consistency and reduce material loss. These systems integrate mixing, granulating, drying, milling and blending, etc. in a seamless process, ensuring minimal downtime and maximum efficiency, save energy. Whether working with granulation for tablet production, pharmaceutical industry, nutrition, animal, or veterinary and food ingredients, etc. Our granulation solutions deliver superior performance.
Design Qualification (DQ), Installation Qualification (IQ), Operation Qualification (OQ), Performance Qualification (PQ), Factory Acceptance Test (FAT), Site Acceptance Test (SAT), all are available.
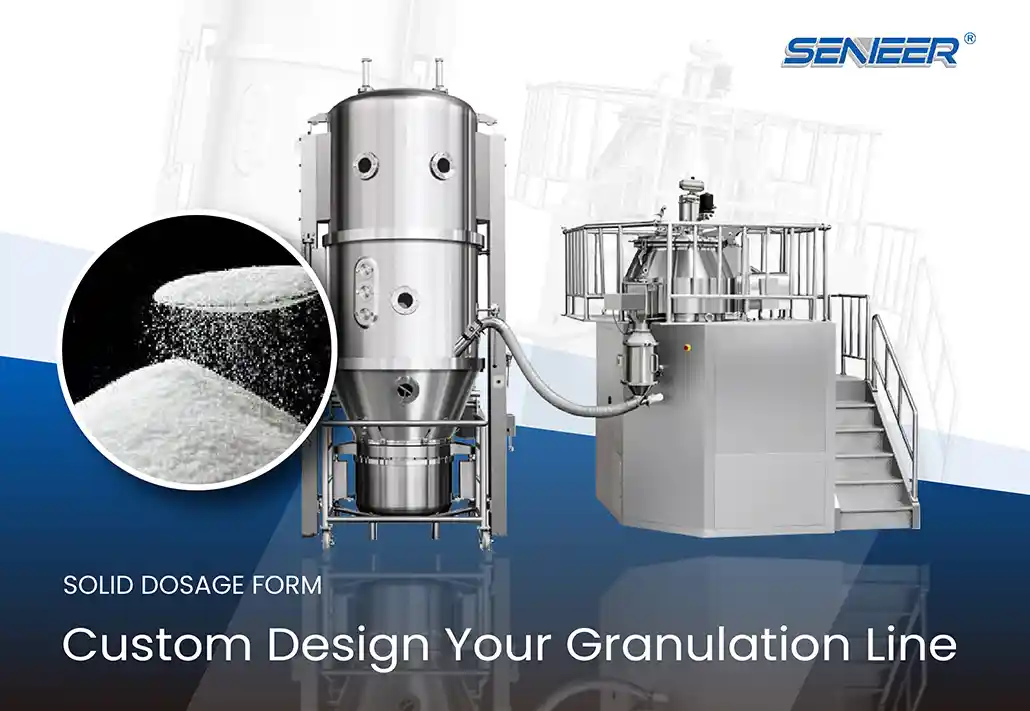
Different Types Of Granulation Line and Process
Granulation includes wet granulation and dry granulation. Senieer offers different granulation lines solutions for its customers. Till now, Senieer professional team has visited 50 countries to communicate URS and understand the production conditions and process improvements of customers’ factories and workshops. Senieer has been practicing the combination of technology and equipment to create value for customers.
Choose Your Granulation Line
Senieer’s Granulation Lines are tailored for various industries, including pharmaceuticals, food processing, and chemicals. We customized some granulation lines for our customers according to their needs, and each line adopts different feeding ways, such as vacuum transfer system, traditional gravity flow, and closed containment system. Whether you need a high-shear granulation system for pharmaceuticals or a fluidized bed system for food, Senieer has the solution that will meet your production needs.
The Senieer Granulation Line typically follows these steps:
- Sieving: The granules are sieved to ensure they are uniform in size and free from lumps.
- Granulating: The wet mass is then granulated using a granulator, which breaks it into uniform granules.
- Drying: The granules are dried using a fluid bed dryer or other drying systems to remove moisture.
- Mixing: Powders or the final granules are ready for use in tablet or capsule production, or other downstream processes.
Guidelines For Granulation Line
Customized Granulation Lines For Customers
The following are some of the granulation lines we have customized according to customer needs. If you also need granulation lines, we hope Senieer cases can give you some inspiration and help.
1. Vacuum Transfer System
- High Shear Mixer → WetCone Mill → Vacuum Transfer → Fluid Bed Dryer → Vacuum Conveyor with Dry Cone Mill → Bin Blender
Closed system complete whole line
2. Traditional Gravity Flow
- High Shear Mixer → Wet Cone Mill/oscillating granulator → Fluid Bed Dryer → Pharma Lifter → DryCone Mill → Bin Blender
- Uses gravity for material transfer.
3. Closed Containment System (cGMP & OEB Compliance)
- High Shear Mixer (Isolator) → Wet Mill → Isolated Fluid Bed Dryer → Dry Mill → Isolated Bin Blender
- Suitable for high-containment API granulation with minimal exposure.
Downstream: tablet press machine, capsule filling machine, etc., Senieer can customize for you.
Senieer Granulation Line 1
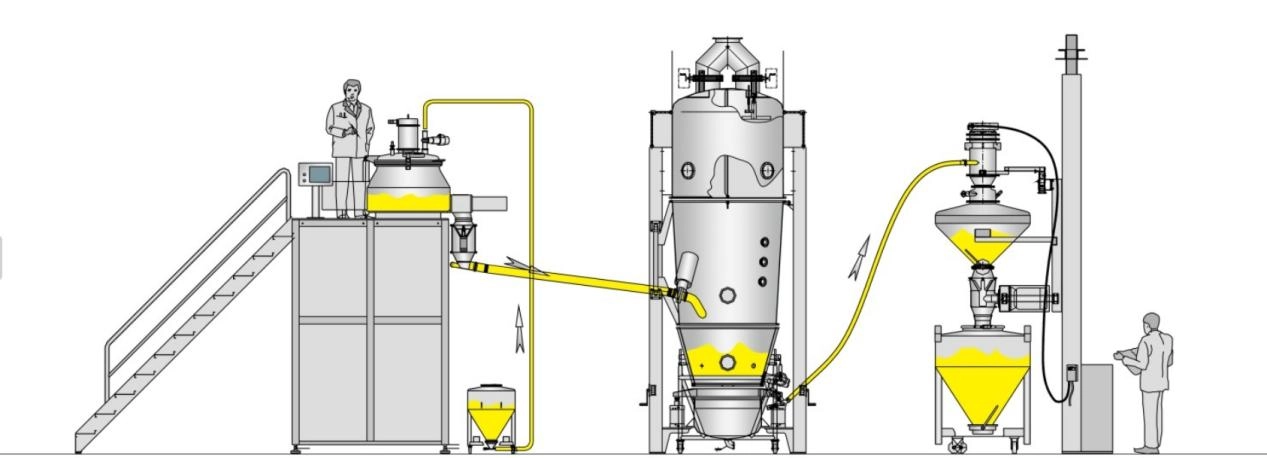
The crushed material is transferred to the rapid mixer granulator’s material bowl by vacuum feeder. After being premixed evenly by impeller and chopper, the binder is evenly dispersed and added to the bowl through the pressure tank or pneumatic diaphragm pump by spray gun.
Adjusting the impeller and chopper rotating speed, make the required wet granules, enter the wet cone mill system (option item). Under the action of the negative pressure suction of the fluid bed dryer, the granules enter the product container of the fluid bed dryer through the pipe, set the required temperature, air volume and other parameters, drying products automatically. After the material is dried to the required moisture, open the vacuum outlet valve and adjust fan volume.
Under the action of the fluidized swirl plate and vacuum conveyer of the vacuum transfer, the dried granules enter the vacuum silo of vacuum conveyer with dry cone mill by transfer pipe.
Select the dry cone mill screen mesh size and adjust the RPM, and load the granules into the IBC bin from the silo, this granulation line solution is mainly used for the production of capsule and tablet granules.
Application: The whole granulation process is completed in a closed system to achieve dust free transfer, easy operation, and meet CE, FDA and GMP.
Code of Federal Regulation Title 21 (CFR21), explosion-proof, WIP/CIP system as optional items.
Senieer Granulation Line 2
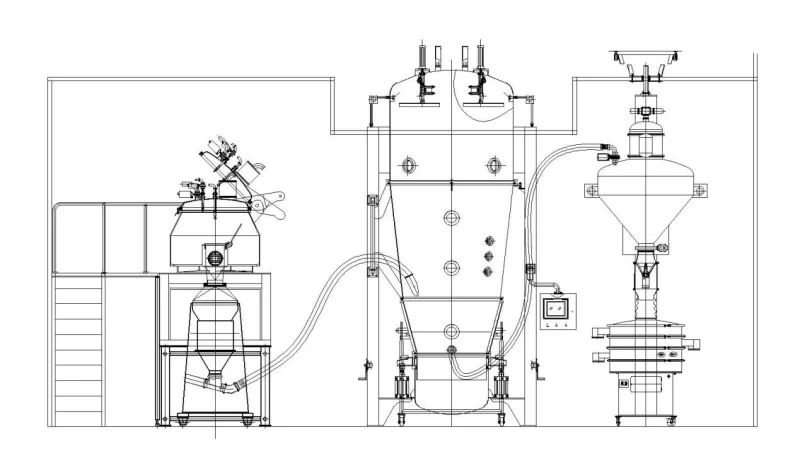
The crushed material is transferred to the high shear mixer’s material bowl by manual or vacuum feeder (option item). Make the granules process the same as the granulation line 1, after making qualified granules, then through oscillating granulator and rotary granulator process.
Then the same as granulation line 1, discharge product to fluidized bed dryer, after drying, the process through drying and dry cone mill, then discharge materials to vibro sifter, after selecting the qualified granules by sifter, then transferred to the mixing process through IBC bins.
Application: the solution is mainly used for granule production processes with high granule size requirements that meet GMP requirements and CE, FDA.
Senieer Granulation Line 3
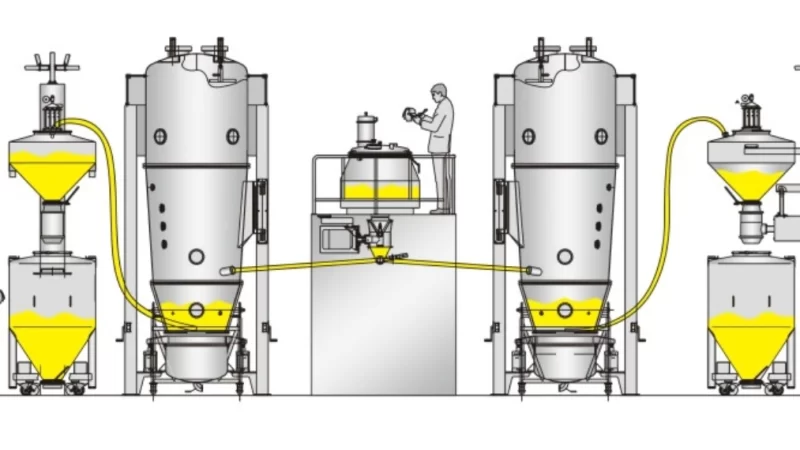
Adjusting impeller and chopper rotating speed, make the required wet granules, enter wet cone mill system (option item). Under the action of the negative pressure suction of the fluid bed dryer 1, the granules enter the product container of the fluid bed dryer 1 through the pipe, set the required temperature, air volume and other parameters, drying products automatically.
At the same time, high shear mixer granulator charging product again, continue the second wet granulation work again. Under the action of the negative pressure suction of the fluidized bed dryer 2.
At this time, the product in fluid bed dryer 1 has been dried. Open the vacuum discharge valve, adjust fan volume. Under the action of the fluidized swirl plate and vacuum conveyer of the vacuum transfer, the dried granules enter the vacuum silo of the vacuum conveyer with dry cone mill by transfer pipe.
The fluid bed dryer 1 starts to dry the product from the high shear mixer under negative pressure again. In this way, the wet granulator is always in operation, and two fluid bed dryers are alternately fed for drying, which improves the production efficiency.
This solution makes full use of the drying time of the FBD dryer and the interval time between charging and discharging, so the whole line equipment can be produced continuously, improve production efficiency and save labor.
Downstream of the granulation line 3, connect post bin blender, bin blender, etc., and different kinds of blenders.
The entire granulation process is completed in a closed system, realizing dust-free transportation, easy operation and meeting GMP and cGMP.
Senieer Granulation Line 4
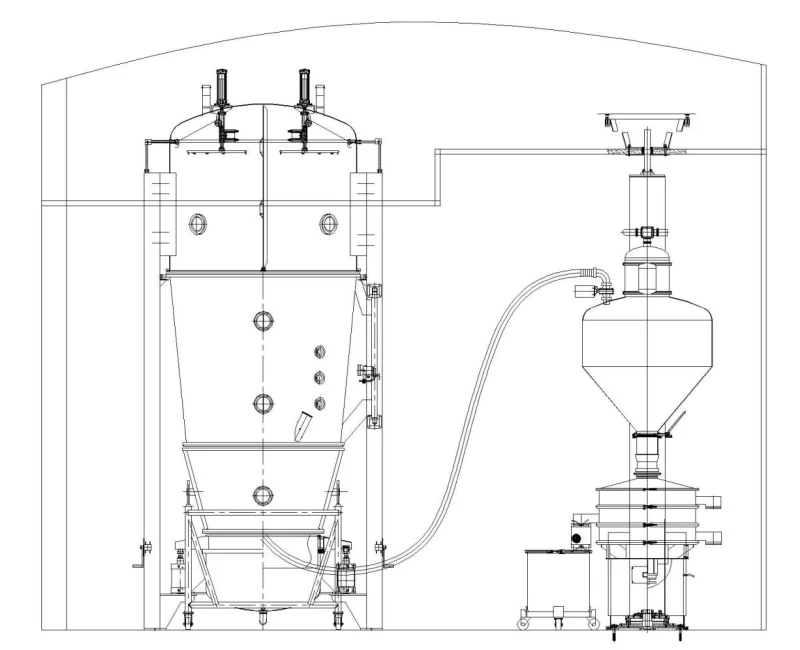
This is one step granulation. The weighed powder material is transported to the fluid bed product container through the pipe under the negative pressure generated by the fluid bed dryer itself. The powder material is fluidized in the equipment under the action of the airflow, so the material is mixed evenly and heated.
The prepared binder is transferred to the spray gun through the peristaltic pump. After being fully atomized by compressed air, it is evenly contacted with the powder material and bonded into uniform wet granules. In the repeated fluidization process, the granules gradually become bigger and dryer. After granulation is completed, open the vacuum discharge valve, adjust fan volume, under the action of the fluidized swirl plate and vacuum conveyer of the vacuum transfer, the dried granules enter the vacuum silo of the vacuum conveyer by transfer pipe. Then milling or sieving.
Application: Suitable for applications requiring uniform granulation and efficient drying of granules, this system combines granulation and drying in one system.
This solution is mainly used for varieties with large amounts of binders or Chinese medicine extracts under the difference in specific gravity between carrier materials. The particles made are loose and have good solubility. The entire granulation process is completed in a closed system, realizing dust-free transportation, easy operation and meeting pharmaceutical industry standards.
Features And Advantages Of Granulation Line
The Senieer Granulation Line is designed with the following features that enhance its performance in various industrial applications:
- Ensures fast and consistent granulation with excellent process control.
- Precise Particle Size Control: Adjustable settings for granule size and distribution to meet specific production requirements.
- Integrated Drying and Sieving: Combines drying and sieving in one system for greater efficiency and minimized handling.
- Customizable Components: Choose from different mixers, granulators, and dryers to suit your production needs.
- GMP-Compliant: All components are made from stainless steel and are easy to clean, ensuring hygiene and safety.
- Low Energy Consumption: Optimized systems for energy-efficient operation, reducing overall production costs.
- Automated Control: The user-friendly control system allows for easy operation, parameter adjustments, and real-time monitoring.
Specific Applications
· Pharmaceutical Industry – For tablet and capsule production, ensuring uniform granules for consistent drug release.
· Nutraceutical Industry – Producing vitamin and dietary supplement granules for improved compressibility.
· Food Industry – Used in instant drink powders, seasoning blends, and functional food additives.
· Cosmetic Industry – For granulated beauty and skincare ingredients, such as compact powders.
· Biotechnology Industry – Processing bioactive granules for controlled-release formulations.
· Veterinary Industry – Producing medications and supplements for animal healthcare.
· Animal Feed Industry – Granulating feed additives, vitamins, and minerals for better digestibility and nutrient absorption.
· Agricultural Industry – Creating granulated fertilizers, pesticides, and soil conditioners.
· Ceramics Industry – Granulating powders for advanced ceramic manufacturing.
· Battery Industry – Used in lithium-ion and other battery material granulation.
Wet And Dry Granulation
Senior granulation lines include wet granulation line and dry granulation line.
1. Wet Granulation
Wet granulation involves adding a liquid binder to fine powders, forming granules through controlled agitation and drying. This method enhances compression properties and minimizes segregation in tablet production.
Important Equipment
- High Shear Mixer Granulator: Rapid mixing and granulation with uniform binder distribution.
- Fluid Bed Dryer: Efficient drying of granules, maintaining optimal moisture content.
- Fluid Bed Processor: A machine used for granulating, drying, and coating powders by suspending them in a stream of hot air.
- Bin Blender: A device used to blend powders or granules by rotating a bin or drum to achieve uniform mixing.
- Milling System: Ensures uniform granule size for downstream processing.
2. Dry Granulation
Dry granulation( also called roller compactor) compacts powders into dense sheets or slugs without liquid binders, suitable for moisture-sensitive products.
Key Equipment:
- Roller Compactor: Uses high pressure to form granules without the need for moisture.
- Oscillating Granulator: Breaks down compacted sheets into uniform granules.
Innovations And Customization
Senieer Granulation Lines are equipped with several innovative features that enhance their versatility and efficiency:
- Advanced Monitoring: Real-time monitoring systems track and optimize key parameters such as moisture content (option item), granule size (option item), granulation time, drying time, air temperature, air moisture, pressure and dust, etc.
- Energe Efficient: Expansion chamber, filter chamber (inside of cleanroom part) and air let duct design insulation system, the processes are optimized to reduce energy consumption while maintaining high production rates.
- Automated Operation: Granulation line automatic control ensures precise, repeatable results with minimal manual intervention. Save recipe parameter, parameter record the track (CFR21) parameter recording and tracking. Intelligence and continuous production of granulation line.
- Customizable Size and Capacity: Machines can be tailored to meet the specific production volumes and granule requirements of the user.
Granulation line can also be connected to tablet press machine, capsule filling machine.
Technical Support and After-sales
- Comprehensive After-Sales Service: Senieer offers full support, from installation to troubleshooting, to ensure your granulation line operates smoothly throughout its life cycle.
- Operator Training: Senieer provides on-site and remote training for your team, ensuring they operate the granulation line efficiently, safely, and according to GMP standards.
- 24/7 Customer Support: Senieer’s dedicated technical support team is available around the clock to assist with any questions or issues that may arise.
Selection Advice
When selecting the right granulation line, should consider:
- Production Scale: Choose from batch or continuous granulation lines depending on your production volume and process flexibility needs.
- Material Type: Select the right equipment based on the material’s characteristics (e.g., wet or dry granulation processes) to ensure optimal results.
- Customizations: Evaluate if you need specific features such as adjustable granule sizes, advanced drying technologies, or automated cleaning systems for higher efficiency and GMP compliance.
Why Choose Senieer?
Senieer is a trusted leader in granulation technology, providing high-quality, reliable solutions for industrial granulation processes. Here’s why you should choose Senieer Granulation Lines:
- Reliability: Senieer Granulation Lines are built for long-lasting performance with minimal maintenance and downtime.
- Efficiency: Designed to maximize throughput while maintaining consistent granule quality, Senieer lines ensure a high ROI.
- Customizable Solutions: Tailor your granulation line to meet your specific production needs with a wide range of machines and options.
- GMP & Regulatory Compliance: All equipment is designed to meet global GMP, FDA, and other regulatory standards for product safety and quality.
- Expert Support: Senieer provides comprehensive after-sales support, ensuring your equipment operates at peak performance.
- Global Presence: Senieer’s expertise spans across multiple industries and markets, ensuring the best possible solution for your granulation needs.
Optimize your production with Senieer Granulation Lines! Contact Senieer today to learn more about its customizable solutions and how they can benefit your business.