Granulation Line
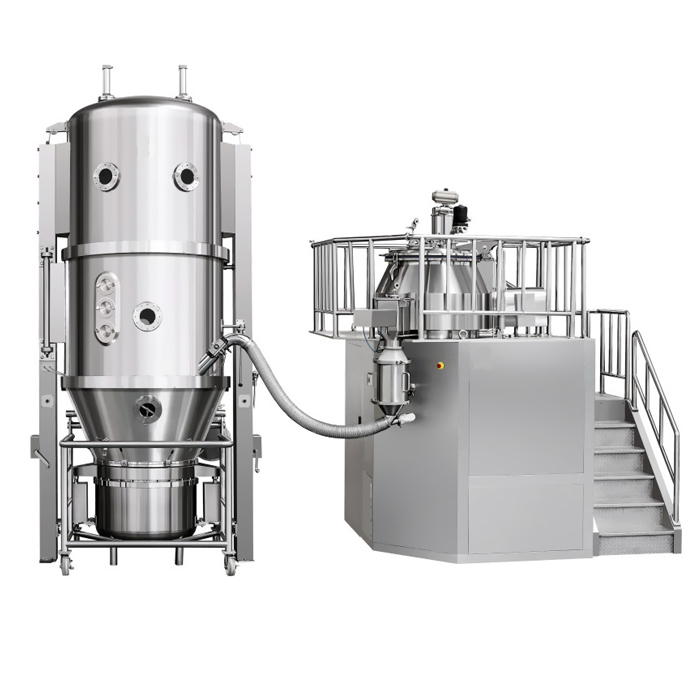
Granulation Line : Product Features
- Provide improved productivity through automation
- Optimal containment, meet with FDA/cGMP standard
- Advanced closed-loop granulation lines system
- Low process time, higher efficacy, maximum operational safety technology
- Smoothly product transfer, more reliable processes
- Optimization with many formulations
- Maximum protection for the product, people, and the environment
- Proven process design, simple scalability
- Grounding and ground monitoring
- Increased yield and efficient
- Siemens 12 inch HMI panel is available
- Siemens Simatic S7-300 series PLC control system is available
Granulation line : Product Description
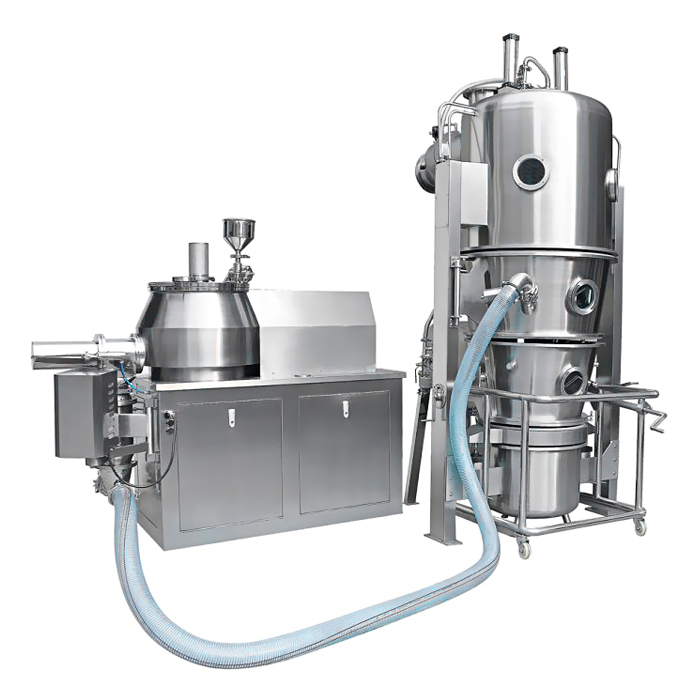
If you are in the pharmaceutical manufacturing industry, then you should consider buying this premium granulation line. This pharmaceutical equipment will ensure there is no cross-contamination.
Granulation line combines both granulation and drying processes to ensure continuous and stable production, it can highly increase the yield of finished products.
The vacuum conveying device and lifting turnover discharging system can greatly decrease labor intensity and avoid dust pollution. This means that the granulation line saves on the cost of labor.
Senieer granulation line system adopts automatic PLC control with the graphical interface. This means that the operation and process parameters can be set automatically for history review and print.
The WIP system in the Granulation line can fulfill well cleaning effect for the granulator and dryer. The ex-proof system, reliable interlock, and earthing ensure the safety of the people, equipment, and environment.
If you would like to buy a custom granulation line, we will work hard to meet the process and specifications. We can customize the designs and sizes of granulation lines.
Please note that we sell these reliable granulation lines to customers who deal in food, chemical, and pharmaceutical products. With us, location is not a barrier. We even make it possible for customers who would like to order this granulation line online.
Would you like to buy this granulation line? then Send your inquiry on Senieer Granulation line right now We are a reliable and reputable granulation line manufacturer in China.
Why Global Company Trust Senieer

Top Quality Factory Price
We have a quality control department to verify each product at different phases, from the procurement of parts to finished granulation line

Equipment Consult & Design Service
Am not sure about the granulation line specifications or operations. What can I do? Simply consult us and we will guide you on everything about granulation line. Our engineers are always willing to give free guidance and consultation whenever they are needed.

Equipment Training & Maintance Service
Free granulation line training & maintenance service for you, we can offer the training regardless of the number of technicians that you want us to train. We can offer the training regardless of the number of technicians that you want us to train.

As Your Layout, Customize Machine
According to your layout, we can suggest the best granulation line capacity and type for you, customize granulation line for you

ISO.CE Standard Qualified
We successfully obtaining the ISO9001:2008 certificate and CE security management system certificate, this is significant for Senieer in building enterprise image. It shows that our granulation line equipment meet the global standards. This certification is a clear proof that we are granulation line manufacturer that competes favorably with other brands.

Equipment Installation Service
Senieer offers equipment installation & commissioning service for production granulation lines, we ensure that all the safety measures adhere during the installation so as to avoid any mishap during the operation of the granulation line
CEO Note
Hey! This is Nikki. Thanks for checking out our granulation line for sale. It is my hope that you are going to buy this granulation line and use it in our pharmaceutical industry.
We are pharmaceutical equipment and machine manufacturer that has been in operation for over 30 years. One of our products is the granulation line equipment. Do you have any questions about granulation line or about any other pharmaceutical machinery, just contact me as I will be glad to help you.
Senieer With Customers
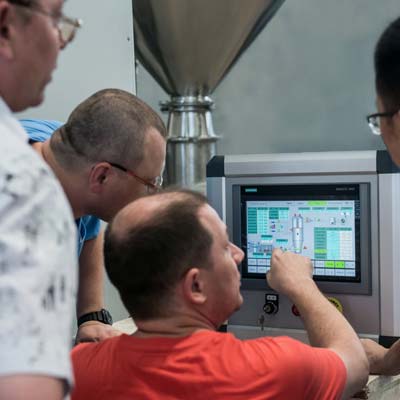
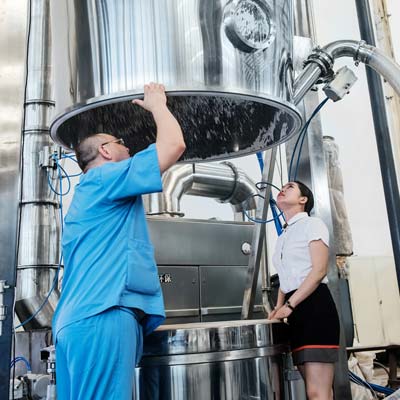
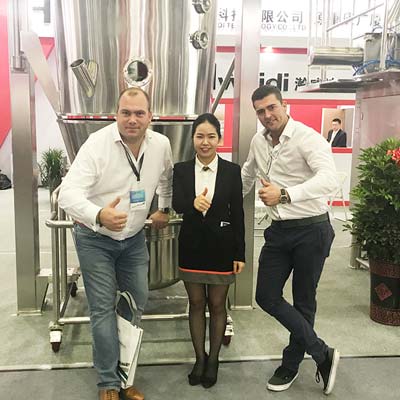
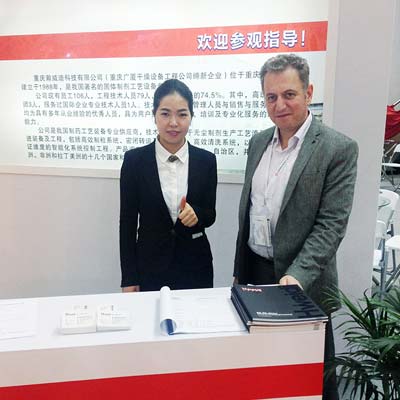
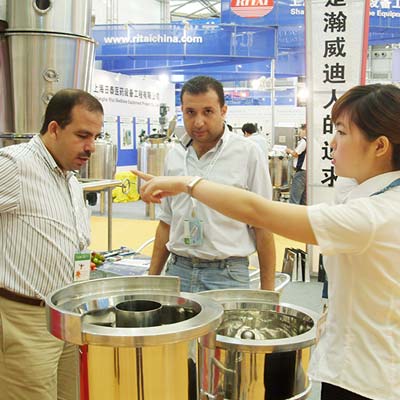
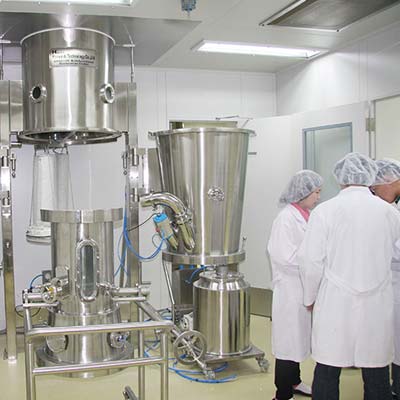
Helpful Resource To Support Your Business
Need Any Help
We address your technical needs, and tell you what we can offer.
Senieer: Your Leading Granulation Line Manufacturer
Nowadays, continuous processing also called continuous fluid bed granulation vs high shear lines to take a more and more important role in Pharmaceutical equipment and machine.
Senieer is a market leader in pharmaceutical production solutions in China. Focus on an integrated solution for solid dosage forms.
Senieer GRANULATION LINE for solid dosage forms also called inline process, it includes High Shear Mixer, Fluid Bed Dryer, Fluid Bed Processor, Fluid Bed Granulator, Lifting Column, Conical Mill, Vacuum Conveying System, Blender, etc.
As a pioneer and leading granulation line manufacturer of premium processing technology systems with 30 years of experience in the development and manufacture of solids, continuous processing becomes more and more important in pharmaceutical, health product, food, fine chemical, and feed processing industry.
We are the system provider for complex production lines in all powder processing industries.
Senieer has special kinds of dust-free solid dosage granulation lines for resolving mass batch production, it realizes continuous production for granulation, drying, lifting, mixing lines.
Solid dosage form equipment line means that the high shear mixer granulator is physically attached to the fluid bed system using a product transfer line.
The product is extracted from high shear mixer granulator using negative pressure and transported to the fluidized bed dryer with the process air.
Regardless of whether a cone mill is interposed or whether the product is a difficult one, Senieer can rise to the challenge.
Minimum transfer time combined with the maximum degree of emptying is proof of this.
Closed product handing is proven technology at Senieer.
Senieer provides special machine line concepts for batch production and continuous operation with well-designed solutions for ONE-WITH-ONE, ONE-WITH-TWO, or ONE-WITH-MORE product flow. Efficient and process optimized.
We offer high performance and high-reliability granulation line equipment design.
Senieer fluid bed lines have a modular design. We offer high performance and high reliability integrated granulation line design.
The base devices are designed as heavy-duty 2 bar,10bar, or 12 bar pressure shock resistant and can be adjusted using various options.
As a partner of the pharmaceutical industry with comprehensive process know-how, our engineers are always at the forefront in the development of needs-based process solutions for your batch production.
Senieer is not only a pharmaceutical granulation line machinery manufacturer but also a granulation production line design company in China.
All types of equipment can be customized by your requirements, once you improve detail user requirement statement(URS), we can supply the equipment line drawing and suggestion for your factory layout, and we can supply our technical support.
Senieer can improve process test service for your best-contained granulation line equipment choice.
Customize and design the best equipment which satisfied with your process. Only those who understand the process and know details can develop systems that can do more than just the sum of individual components.
Senieer integrated granulation line is revolutionary.
Senieer import top class spare parts brands, such as Siemens, Festo, ABB, Sefar, Schlick, Spirax Sarco, etc. Outstanding added value and quality guarantee.
Senieer customizes all documentation related to the granulation line equipment, making easier the training, operation and maintenance of the equipment through the life term even in the more exigent industries as the pharmaceutical market, we provide a complete set cGMP including URS, DQ, IQ, OQ, SAT, FAT, USER manual documentation.
We perform the qualification executions as customer request.
Our business sections are operating under the strict International Quality Standard of operation with control regulation certificate ISO9001 which is called the “International Quality Certifications”.
Our company consistently carries out and applies the rules to our manufacturing facilities, strict supervision, and monitoring.
Having supervision in every department that highly focus and concentrate systematically on “Quality Management System” to fulfill the demands and maintaining the high-quality demands.
If you want to start in continuous granulation line business, please contact us for more details, we will send you detail specification, quotations, layout drawing for equipment.
Granulation Line: The Definitive Guide
The global pharma market is ever-growing. According to a study carried out by The Business Research Company, the global pharma market was estimated at $934.8 billion in 2017. Its size is projected to grow to $1170 billion by 2021.
North America and Western Europe have accounted for over 50% of the world’s pharma market for many years. But the Asia Pacific is now the second-largest pharmaceutical market.
Tablets are the most widely produced drug dosage forms. Manufacturing tablets involves compressing granules or powder blends.
For more than 30 years, Senieer has been an established pharmaceutical equipment manufacturer. We focus on equipment that manufactures solid dosage forms with emphasis on continuous granulation machines.
This granulation line, one high shear mixer connect two fluid bed granulators and one vacuum conveying with co mill
Why continuous granulation?
Batch processes have been the norm in the pharmaceutical industry. The challenge with batch-processes has to do with their dependence on human intervention and a rigorous adherence to operating procedures.
The results are always variable depending on how well the procedures have been followed. Continuous processing, on the other end, is efficient and offers a degree of independence from the operator’s influence. The product quality is less variable.
So how does it work?
In batch processes, several machines are used for different processes with pauses between processes for the operator to perform processes such as sampling or product transfer.
Continuous processes are more autonomous. And multiple processes can be carried out in the same equipment. You’ll encounter the term “Single-pot processing.” It means that several processes such as granulating, drying, coating, and sizing are carried out in the same fluid bed. Granulating, wet cone mill, drying, coating, lifting, transferring, dry cone mill, blending in the same granulation lines.
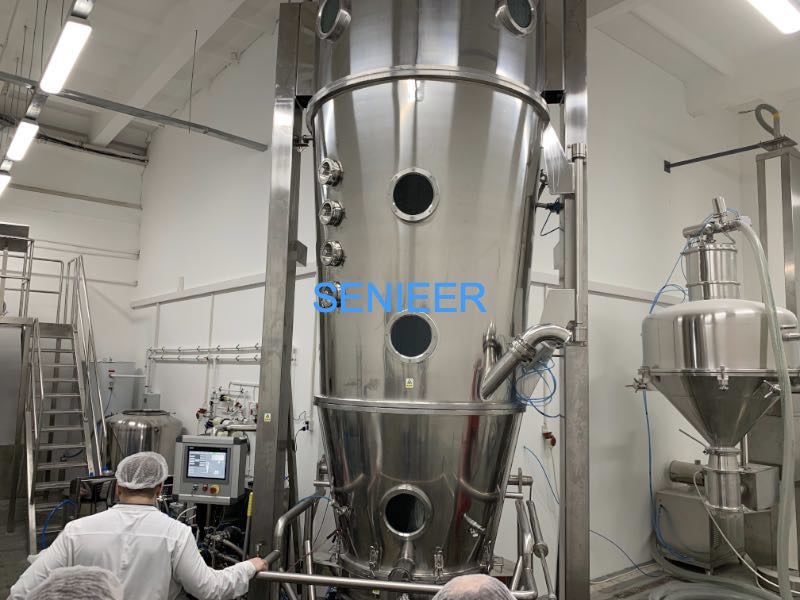
You will learn more about this, but first, let’s start with the basics.
Chapter 1: What is granulation?
1.1 Granulation Definition
It’s very simple to understand the granulation process in tablet manufacturing. Simply, it’s the formation of granules from smaller particles of APIs and excipients.
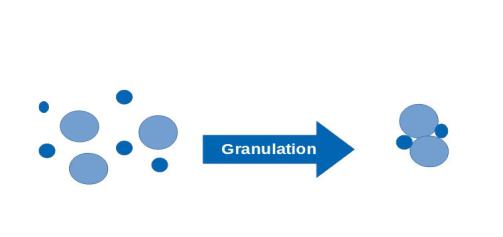
At the heart of the tablet manufacturing process is the granulation process. The desired outcome after granulation is dust-free granules. They are easy to compress into tablets than smaller grains.
1.2 Senieer Granulation Lines
Senieer is a one-stop solution for efficient and productive pharmaceutical lines. Our solid dosage forms will be the pillar of your factory bringing in many benefits including excellent products, reduced production costs, stability, among other advantages.
We have continuously served many customers around the world since 1988. You can order complete granulation line equipment or single machines for your existing pharma company.
If you need help understanding the equipment we offer, read on.
1.3 Granulation Techniques
Granulation helps promote the flowability, compressibility, bioavailability, and homogeneity of the API mix. There are different granulation methods and techniques, which influence the properties of the granules.
First, the major granulation line processes include:
- Direct Compaction
- Dry granulation
- Wet granulation
Tests have shown that direct compaction leads to problems with the flow of powder and the grains sticks on the surface of machines during compression.
Wet granulation also called high shear mixer granulation tends to be the most preferred process. And the granulation equipment is categorized based on the level of shearing force impacted on the bulk power.
We have:
- Low shear granulators
- High-shear granulators
High shear granulation forms granules that are harder and dense. Although they are tougher to mill, high shear pills have slower release-times, which improves their efficacy and availability.
Granules produced by low and medium shear fluidized granulation display good performance during milling and tablet compression.
1.3.1 High shear granulation
The high shear granulation process is wet because a liquid is added to the API mix to help create bonds between grains to form granules.
Binder liquids used include:
- Propan-2-ol/isopropanol (organic)
- Ethanol (organic)
- Water
Organic solvents (isopropanol and ethanol) are added to an API mix that can react with water (hydrolysis).
Since they evaporate rapidly at lower temperatures than water, the powder mix drys quickly when they are used. However, organic solvents are more costly than water. It’s also more challenging to dispose of them after production.
We can recommend binder liquids according to your process requirements.
Next, let’s look at the process steps for high shear mixer granulator:
- Granulation with a high shear mixer:
The main parts of the high shear mixer or the high shear homogenizer include:
- Dome-shaped stainless-steel mixing bowl
It holds the API + excipients. Inside, you’ll find the impeller and chopper. The mixing bowl may have jacketed-walled (as an optional item), where hot or cold liquids can be channeled through, to heat or cool the contents of the bowl.
- Impeller
The impeller consists of two or more blades. We normally we design three blade impellers. It agitates the power mix to distribute the granulation fluid evenly. It has a low rotation speed of 5 rpm-300 rpm.
- Chopper
The chopper has smaller blades than the impeller. It’s usually fitted on the side or at the bottom of the dome-shaped bowl. Its role is to shred the wet mass of powder into granules. It has a higher rotation speed from 200- 3000 rpm.
- Wet cone mill (as optional item)
The wet cone mill is available as an optional item. It mills granules produced by the wet granulator into smaller particles before drying.
An explosion-proof high shear mixer granulator design is also available if you need it.
Here are the production steps on the high-shear mixer. You can learn more by checking our full high shear mixer guide.
Step 1: Loading /charging process
The first process step in high shear granulation is loading the API and excipients into the bowl. You either load a premixed powder. Alternatively, mixing can be done inside the bowl by loading all the ingredients and running the impeller at full speeds for two to five minutes.
There are two ways to feed the ingredients; gravity feeding is done manually using a lifting column; or vacuum feeding using a vacuum pump -which we use in our high shear mixer.
Step 2: Applying binder fluid
After mixing, the binder fluid is added to the powder mix. The chopper and impeller are decelerated for this step to ensure even distribution of the binder fluid.
Step 3: Granulation by rotating rotors
After applying the binder fluid, the impeller and chopper are then accelerated to full production speeds for the granulation process. Nucleation and granules growth then occurs.
Granulation is done using a small batch of materials at any given moment. It ensures minimal losses should problems occur.
Our high shear mixer is equipped with a wash in place system (as an optional item) that will efficiently clean the high-granulator without disassembling the impeller or chopper.
- Drying the granules
There are several ways to dry granules after granulation; tray drying was a method used in the past but it was only suited for small amounts of product. It was inefficient since it produced uneven drying. It was also labor-intensive and time-consuming.
Now, most of the drying is performed in the fluid bed dryer. You can also use the fluid bed dryer.
Fluid bed dryer

The fluid-bed drying technique has more advantages than drying granules in an oven.
What is the principle of the fluid bed dryer?
It works by blowing a stream of dehumidified and dried air from the bottom of the fluid bed dryer base part.
The wet mass of granules is discharged over this bed of air. There is a fine mess on the upper section of the dryer to prevent the particles from escaping.
When the granules have attained the required qualities in terms of moisture level, they are emptied and transferred to the next process equipment.
The granulator is then filled with a new batch of wet granules. It dries materials much faster. Learn more about the fluid bed dryer.
Fluid bed granulator
The granulator has dual functions; it can perform low-shear granulation and it can also dry the wet mass of granules. We’ll talk more about the fluid bed granulator later in this chapter.
High shear mixer wet granulation and fluid bed system, etc of granulation lines available share one WIP system(optional item)
- Transferring granules
From the dryer or granulator, the granules have to be transferred. There are two ways to do this:
Vacuum conveying
It involves using a vacuum conveying to transfer the materials from the fluid bed dryer into another bin using a feeder tube. It has several advantages such as efficient use of space and reduced dust levels.
Lifting column
Senieer manufactures several types of lifters that are used for discharging and transporting materials from the fluid bed dryer.
You can learn more about the lifting columns here.
- Milling
Milling is the process of breaking down lumps of agglomerated granules into smaller sizes. Milled granules have to be sieved to ensure they conform to the required standards.
There are two milling types; wet milling done before drying the wet mass, and dry milling done after fluidized drying.
The machine used for milling is the cone mill or conical mill.
Cone Mill
The main features of the cone mill is an impeller and screen for filtering granules. The impeller is rotated by a motor and impacts kinetic energy on the lumps of granules.
The sheer force causes the mass to fracture and the granules fall on the screen –that’s made up of a series of holes with the preferred aperture size.
While the main aim of milling is size reduction, it also achieves other functions such as creating uniform particles with great flowability.
Online sieving also filters out very large particles that cannot be milled by the impeller
At Senieer, we supply cone mills that be installed inline. You can learn more about the bin cone miller here.
- Blending
Senieer has different kinds of blenders; IBC Bin Blender, Post Bin Blender, Fixed Bin Blender, and Laboratory Bin Blender.
Blending is done when we add more compounds during production. After inline milling and sieving, just before the tablet
filling & compression, we add lubricants to the granules.
What are lubricants?
They are compounds added to reduced friction between the granules and moving parts of the tablet compression machine.
Common lubricants including fatty acid esters e.g. sugar esters and glyceride esters such as monostearate.
After adding the lubricant, the granules are blended or mixed by a bin blender.
Bin blender
Senieer’s bin blender carries out clamping, lifting, tilting, and mixing of granules with the lubricant.
You’ll get uniform mixing, and the bin blender has several safety features. Learn more about the bin blender here.
- Capsule filling or tablet compression
After blending the granules can be made into tablets using the tablet compression machine.
You can also fill capsules – small gelatin caps – with the granules manually or with a capsule filling machine.
1.3.2 One High Shear Mixer With Two/More fluid bed granulators & dryers
the high shear mixer was connected to one fluid bed granulator or fluid bed dryer.
But we also supply a granulation line where the high shear mixer is connected to two fluid bed granulators or dryers.
We can even have one high shear mixer connected to more than two fluid bed granulators or dryers.
This setup has one major advantage; it leads to an increase in the volume of drugs produced.
1.3.3 Fluid Bed Granulator
Also called the fluidized bed granulator, it combines two processes in one pot: wet granulation by application of a binder fluid and drying of the resultant granules.
The granulation machine parts include an air handling unit, main tower (with the base part, product container, expansion chamber, and filter chamber), exhaust air system, and spray system.
So what’s happening here?
The steps include:
- Charging: Feeding of APIs and excipients materials into the product container. An automatic material charging system is available as an optional item.
- Fluidization: It involves blowing a constant stream of heated air from the bottom of the product container. The airstream suspends powder particles. Electric heating is available if you need it.
- Spraying: There is a nozzle inside the product container. It using atomized air to convert the binder solution into very fine droplets. The powder grains are moistened. Collision with other grains leads to the formation of bridges between them.
- Drying: The binder fluid is then evaporated from the granules. The fluidization process is stopped, and the product discharged.
One of the fluid bed granulation advantages is that the drying time is up to fifteen times faster than for tray drying.
You can learn more about the fluid bed granulator here.
1.3.4 Fluid Bed processor
The fluid bed processor further combines more processing steps into one unit including spray granulating, drying, coating, and direct pelleting.
To perform these tasks, the fluid bed processor has a top spray system used for spray granulation and a bottom spray system used for coating or granulation.
While the top-spraying coating is feasible, it is the least common technique because it doesn’t give the granules a perfect film, and there is wastage of the coating liquid.
While the bottom-spraying granulation is feasible, it has a low efficiency compare with top spray granulation.
Most of the coating in the pharma industry takes place using the bottom-spray method that is also called the Wurster fluid-bed process.
It’s more precise producing films with a high degree of uniformity and efficiency.
There are many advantages of using the fluid bed processor including better control of process parameters, reduced handling costs, less space required, and more!
Find out more about the fluid bed processor.
1.4 Advantages of the wet granulation line
The wet granulation line is mostly used to prepare solid dosage forms due to its many advantages: Some include:
- Better flowability of particles since it forms more spherical granules.
- The granules’ compressibility is also improved since it reduces air entrapment in the granules.
- For low-dose drugs, it provides better uniformity.
- It also improves the dissolution rate of soluble drugs.
- Wet granulation produces tablets that are suitable for further post-processing methods including tablet coating.
- With a high degree of containment and use of binder fluids, there is less dust pollution during the manufacturing process. Thereby, there is less chance of contamination.
- Our granulation from a high shear mixer, fluid bed, lifting column, bin blender happens in a closed container with no material loss and dust pollution.
2.6 Disadvantages of wet granulation line
While the wet granulation line process is the most employed, it is also subject to some limitations:
- It’s unsuitable for active ingredients that are sensitive to moisture.
Chapter 2: General Tablet manufacturing process
Have you been wondering how are tablets made? Let’s go over the process, step by step.
Step 1: Milling of APIs and Excipients
A tablet has two main components:
- The API
It’s the active ingredient that provides the pharmacological benefits to the user. Put more simply, it’s the component that provides the healing benefits. Some drugs have more than one API. But on average, APIs make up 10% of the medical pill. - Excipients
Everything that is not the API is the excipient. They have other roles like enhancing the bio-availability of the API. Some excipients include:
Excipient | Role |
Diluents | They add to the bulk of the tablet and control the dosing. The most common diluent is lactose. |
Binders | Also called adhesives, they promote cohesiveness between the other ingredients. |
Disintegrants | They ensure that the tablet will break down rapidly in water. It promotes the pills their dissolution in the body to release the active ingredient. |
Where do APIs and Excipients come from?
Pharmaceutical companies get their raw materials from suppliers. The API supplier will mill the API into the required particle size per the customer’s order. In most cases, the suppliers will be based overseas.
Still, APIs have to meet the stringent requirements and oversight by the authorities in the destination country. For instance, the US FDA still inspects API companies in overseas countries for their domestic pharma companies.
Step 2: Weighing and Blending
Weighing:
Pharmaceutical plants store their APIs and excipients in a warehouse. From the warehouse, they have to be weighed & mixed before production.
Weighing takes place in the weigh-room, which may also be called, ‘the pharmacy dispensary, dispensing room, weighing chamber, or dispensing booth.”
After weighing, APIs and excipients are placed inside a clean container formally named Intermediate Bulk Containers or IBC bins.
Bins may be round or square-shaped. They hold the raw materials and are also used for blending. Learn more about Senieer’s Bins and Drums.
A lot of care has to be taken inside the weighing room to avoid cross-contamination, where unwanted substances either from different drug formulations wrongly enter the ‘API mix .’
Some measures taken to prevent cross-contamination include thoroughly cleaning the equipment that contacts ingredients. Operators also wear safety gear so as not to inhale volatile particulates.
For large IBC bins with a capacity of over 1000 liters, the WIP system method of cleaning is adopted. Internal surfaces of the bin are cleaned without disassembling the equipment.
Some pharma companies may also use bin washer stand-alone systems.
Blending:
Once ingredients have been weighed and placed inside the IBC bin, the blending process can begin. It simply involves, mixing the constituents until you get a very consistent mix. All parts of the API mix must have the same ratio of excipients to the APIs.
During normal production, blending may be carried out several times. Sometimes new APIs or excipients may be introduced at certain stages after production commences.
To get a consistent blend, ingredients have to be of similar particle sizes. In previous years, sampling would be done by a human operator to test whether a successful blend had been achieved.
With new imaging technology like infrared spectral imaging that provides more detail than previous methods, the API mix particles can be studied more easily and accurately.
Safety screening may be done before or after blending. It prevents foreign contaminants from entering the API mix. It’s also done to ensure that ingredients meet the required particle sizes to promote higher product quality.
Step 3: Granulation
The granulation process in pharmaceutical manufacturing takes place after dry blending. As we have seen earlier, it involves creating large particles from API and excipients grains.
We usually have a specific particle size in mind. So for the granulation process to be deemed successful, it must generate the required particle size.
The typical size range of granules falls between 0.2 to 4.0 mm. But on average, granules tend to be within 0.2-0.5 mm.
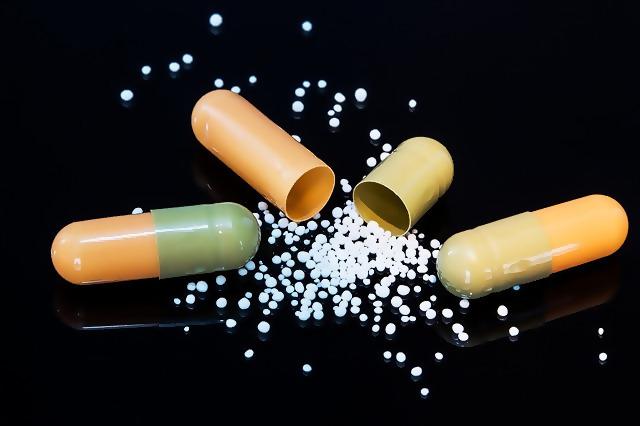
For powder grains to become granules, physical bonds must be created between them. There are two ways to do this:
- Without any liquid binding solution – (Dry granulation)
- Using a binding liquid agent – (Wet granulation)
Wet granulation is the widely used technique of creating tablets. We’ll talk about both methods in the next chapter.
Step 4: Screening + Lubrication
Before we talk about screening, you may have encountered granules with different colors and finishes. How are they made? Through, the coating process.
Coating:
Powders, tablets, and pellets, are coated for several reasons. Chiefly to delay the drug release in the body and protect the active ingredient from acids in the stomach.
Most of the drug absorption takes place in the small intestines. Besides, the coating may also safeguard the delicate walls of the stomach from aggressive drugs.
For instance, aspirin used to relieve mild pains has been studied for its negative gastrointestinal effects such as causing ulcers. It’s enteric-coated to make sure that it’s only released in the small intestines.
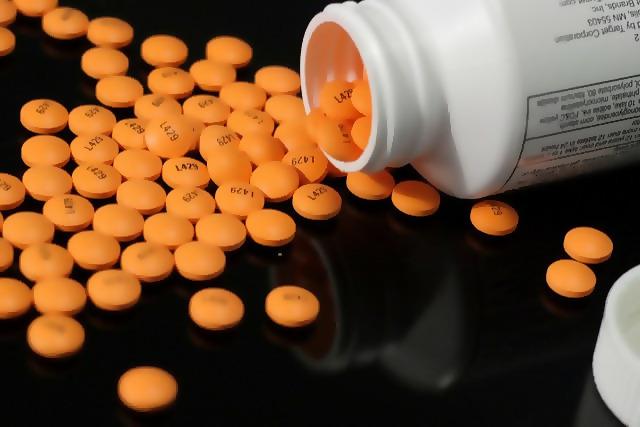
It may also improve the APIs availability, mask the unpleasant taste or smell of some drugs making it easy to swallow the tablet.
Screening
Granules have to be screened as a measure of quality control. The process involves passing the granules through a sieve or screener.
The most common sieve is the vibratory sieve, equipped with a motor and mesh with the required aperture size.
Only the granules of the proper size pass through. Bigger particles will remain on top of the screener.
Like most of the most equipment in the pharma plant, the sieve is usually made from stainless steel for durability.
Lubrication
Lubrication is an essential step before tablet compression. It’s done to reduce friction. And where does friction exist?
It occurs between the surface of the tablet with that of the tablet’s compression machine die and punch. This type of friction is called die-wall friction. By reducing it, we keep the tablet from sticking to the punches or die surface.
Inter-particulate friction can also occur between granules as external compression force is applied.
Step 5: Tablet Compression
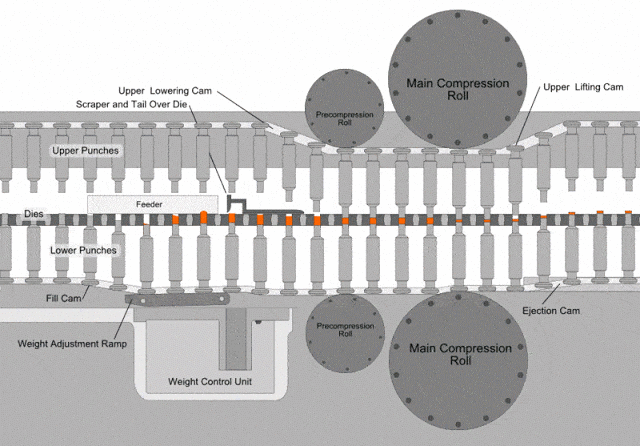
Tablet compression is mostly done after granulation. But in rare cases, direct compression of an API mix can be done on the powder mix.
In both cases, you’ll need a tablet compression machine to make tablets. Its main parts include the compression rolls and the punches as shown above.
Compression occurs in four steps:
- The granules flow into the die cavity through a feeder (Filling).
- Excess material is removed from the die using a scraper that scraps off the excess material (Metering).
- The lower punches and upper punches come together to compress the granules into the required tablet size. (Compression).
- The compressed tablet is ejected from the line for packing (Ejection)
Chapter 3: Quality Granulation machine in China
3.1 Get the best granulation line price
Senieer offers some of the most competitive prices for wet granulation lines.
You can choose between our integrated high shear mixer & fluid bed dryer, the fluid bed granulator, and the fluidized bed processor.
Founded in 1988, the company continues to supply innovative processing units and manufacturing technology.
3.2 Our services
Our pre-sales and after-sales services make it is easy for customers to acquire and use our processing equipment.
As a global company, Senieer products and services can be used all over the globe.
With our unique insight and long term experience in the pharmaceutical industry as one of the top granulation machine manufacturers, we can help you find the most reliable solutions for your company’s manufacturing needs.
Whether you need assistance setting up a completely new processing plant or need single process equipment, our technical team will offer all the consultation and guidance.
After you buy the tablet granulation machine, Senieer continues to collaborate with your company.
Our engineers can offer assistance during regular equipment maintenance, provide fluid bed granulation troubleshooting, and even handle on-site repairs.
You can also count on Senieer for a quick supply of spare parts.
We also offer training for operators to help them maximize your factory’s efficiency.
Contact Us
Reach out to our professional support team by sending a request on our contact page, and tell us more about your needs. You can also send an email to sales@senieer.com or call us at +86-13637787586
FAQ
- What quality standards do you conform to?
Senieer’s products conform to GMP, cGMP, and US FDA international standards.
- Are you a trading factory or factory?
We are a factory that manufactures the equipment at our workshop. That’s why we can handle custom orders. We can do a process test in our laboratory.
- Can I visit your plant?
You can visit our factory whether you have ordered a machine or your shopping for one.
- How many years have you been operating?
We have been operational for more than 30 years now. You will greatly benefit from our experience.
References
- The Growing Pharmaceuticals Market: Expert Forecasts and Analysis
- High shear mixers: A review of typical applications
- Granulation – Science Direct
Chapter 1:
Pharmaceutical bins are usually classified under the IBC (intermediate Bulk Containers) group of equipment. This is mainly because they give allowance for the temporary storage of materials as it awaits to be channeled to the next production stage.
Chapter 2:
Before you buy a pharmaceutical bin, it will be prudent to know whether it is the right one for the job. This is where the issue of pharmaceutical bin types comes in.
Chapter 3:
While buying pharmaceutical bins, it is prudent to know its main parts and components. This is vital as they determine the overall performance and operation of the bins.
Chapter 4:
While buying pharmaceutical bins, there are basic factors that you can easily overlook and others that will require your full attention. Failure to be keen on them may result in a poor purchase of the equipment.
Chapter 5:
Looking for the best pharmaceutical bin? There are numerous precautions that you should take. We have outlined some of these necessary precautions below
Chapter 6:
Here is a compilation of the frequently asked questions about pharmaceutical bins. I hope that from these questions you will be in a perfect place to make an informed decision about this pharmaceutical bin
Chapter 7:
Here is a compilation of the frequently asked questions about pharmaceutical bins. I hope that from these questions you will be in a perfect place to make an informed decision about this pharmaceutical bin
Chapter 8:
Here is a compilation of the frequently asked questions about pharmaceutical bins. I hope that from these questions you will be in a perfect place to make an informed decision about this pharmaceutical bin
Chapter 9:
Here is a compilation of the frequently asked questions about pharmaceutical bins. I hope that from these questions you will be in a perfect place to make an informed decision about this pharmaceutical bin
Chapter 10:
I hope we have answered all your questions about pharmaceutical bins. You can use the information in this comprehensive guidebook to purchasing the best pharmaceutical bin.