There Is No “Only” Containment Solution
Michael Maintok — Senieer Corporation Key Technology Business Development Interview
As the requirements for product protection and operator protection increase, so do the requirements for containment solutions. However, this does not mean that the use of fully automatic containment systems is mandatory. In this interview, containment expert Michael Mantock explains different containment concepts.
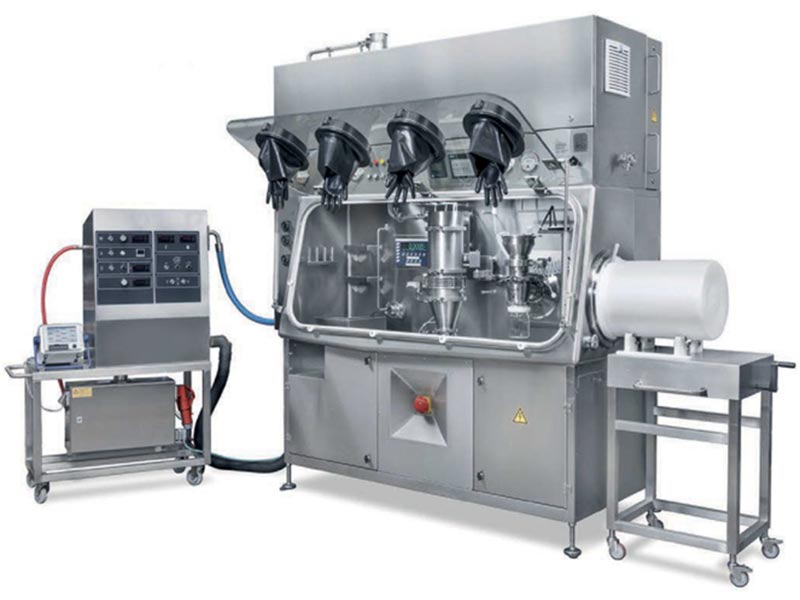
Interviewer on containment
In recent years, there has been an increase in the use of containment production equipment when handling active ingredients. However, it can be seen that each operator handles it differently. Senieer offers different production process equipment to meet containment requirements. What are the current needs for containment?
Michael Maintok on containment
We are currently working on different projects, targeting all imaginable solutions involving different levels of containment: solutions covering OEB4 or OEB5, WIP cleaning with manual intervention or CIP in-line cleaning equipment. Containment production is very important, even if personnel have taken some protective measures, operators should not easily approach the equipment at any time. Online cleaning scenarios of different customers: some equipment needs to be cleaned manually after cleaning in place (WIP), and the workload is relatively large and the cost is higher, so automatic cleaning (CIP) is used; some equipment is cleaned in place (WIP) and subsequent manual cleaning with protective clothing is simpler and less expensive. Of course, the necessary risk analysis must be carried out in advance.
Some customers only automate critical interfaces, such as loading, unloading, and sampling. But fabric filters in fluid bed cannot be cleaned in line (CIP). It must be manually wetted first, and then the filter can be removed in an open area.
For example, if cleaning is only performed every two weeks, in this case, a fully protected operating design is acceptable. And these questions are definitely considered by companies in the pharmaceutical industry with a global presence. There are also large pharma plants that require fully automated cleaning – of course it’s going to be a lot of money, but partly because of regulations and ideas from the operators.
Interviewer
What are the reasons for the formation of these solutions?
Michael Maintok
The typical question is: how often do we need to clean the equipment? How long does manual or automatic cleaning take? Then find the best way out of it. But it also requires that operators must be protected and cross-contamination is not allowed. In this case, everyone will work together to find the best solution. Often, clients already have specific ideas. But in the end, people will come to and accept a completely different solution. Because these companies are subject to audits – then the scheme needs to be validated and there will be no problems during the inspection.
Interviewer
What will the inspector look out for?
Michael Maintok
There are different standards. For example, local government agencies are often more concerned with operator protection, while FDA inspectors want to know how high the risk of cross-contamination is. Occupational safety is very important if working with highly active substances and if the product does not meet the required pharmaceutical quality, it will not be approved. People always think that countries with lower occupational safety requirements don’t take this so seriously – but I don’t think so. Furthermore, occupational safety always means product protection at the same time.
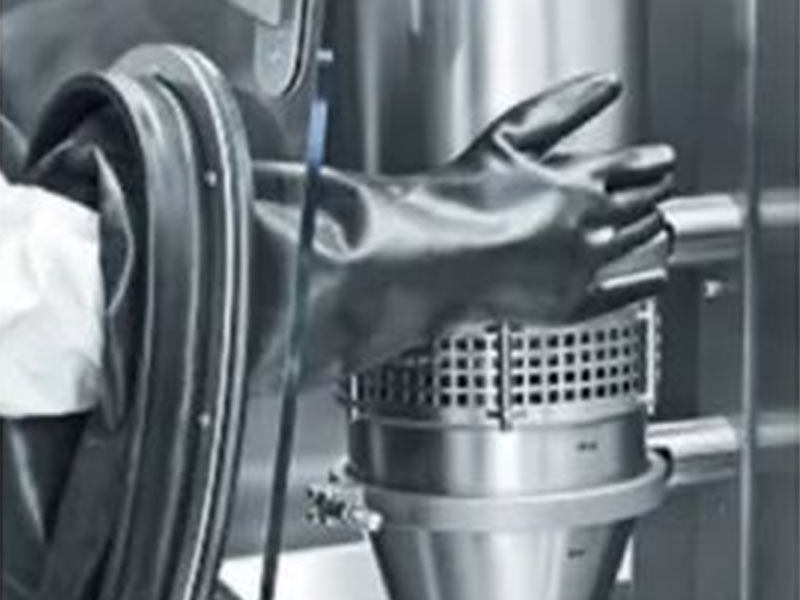
Interviewer
Why choose a highly automated containment solution?
Michael Maintok
If the equipment does not need to be opened, then there is no need to demonstrate that the cleaning is complete. However, it is always up to the operator. There is a standard operating SOP procedure for cleaning in place (WIP) where the operator must check every work step while following the dual control principle. In the case of cleaning in line (CIP), the cleaning process needs to be validated to demonstrate that cleaning is always performed in the same way.
Interviewer
Even though the general idea of the company is to clean automatically, it’s likely to run into questions about cost-effectiveness at some point.
Michael Maintok
For high containment equipment, cleaning in line (CIP) has become a trend, but it is not yet an automatic conscious behavior. Currently, these two ideas coexist, and people are trying to find the best way. You may recall that Pfizer built a factory in Pfizer Illertissen in 2008, which was fully automated. At the time, it was believed that the only way to proceed with the OEB5 work was this. But today people don’t think that way. For products with lower OEL values, fully automated work may be considered. But the requirements of OEB 5 can now also be dealt with in a more economical way.
Interviewer
What makes people change their minds?
Michael Maintok
Technical feasibility. Implementing robotics within isolators is an increasingly important topic because of the increasing demand for OEL values of the working environment, but this does not necessarily fit the requirements of OEB 5. The containment manual says, “The question is not whether containment is required, but which containment is required”. When one considers that the requirements will increase, then full automation is often required.
Interviewer
In your opinion, what are your general recommendations for factories with high containment requirements?
Michael Maintok
If anything, it’s this: There is no such thing as an “only one” containment solution. Even for OEB 5 requirements and dealing with products with an OEL value of 100 ng/m3, there is not only “one solution”, there are many approaches and possibilities. It must be determined on a case-by-case basis.