01 Drug Development Process, Chemical Characterization, Production And Control In Oral Solid Dosage Forms
- Components in the formulation
- BE information
02 Chemical Characterization, Production And Control In Oral Solid Dosage Forms
Reverse Engineering incluation of three different lots of RLD for:
- Potency/purity
- Impurity profile (related substances)
- Content uniformity
- Weight variation
- Dissolution profile
- Disintegration time
- Hardness and Friability
CGMP Specifications That Meet Regulatory Requirements
System Based CGMP Auditing On Manufacturing Facility:
- Quality System
- Materials System
- Facilities and Equipment System
- Production System
- Packaging and Labeling System
- Laboratory Control System
03 Chemical Characterization, Production And Control In Oral Solid Dosage Forms
Pre-Formulation Studies for Drug Development Process
- Analytical method development (Develop adequate analytical methods for API)
- Acquiring API and related impurity reference standards (USP or other sources)
- API characterization and qualification, including chemical and physical properties studies, such as solubility, density, particle size distribution,polymorphism (any attributes relevant to the formulation)
- Excipients specifications (acceptance criteria and testing methods to meet USP/NF standards), and excipients characterization and qualification, including compatibility studies with API.
CGMP Specifications That Meet Regulatory Requirements
- Qualification of API and excipients suppliers, including auditing and full testing on three different lots
- Establish acceptance criteria for API and excipients and corresponding analytical methods
- Validation or verification of theseanalytical methods
- Preparation of pre-formulation study report or summary from CGMP perspective
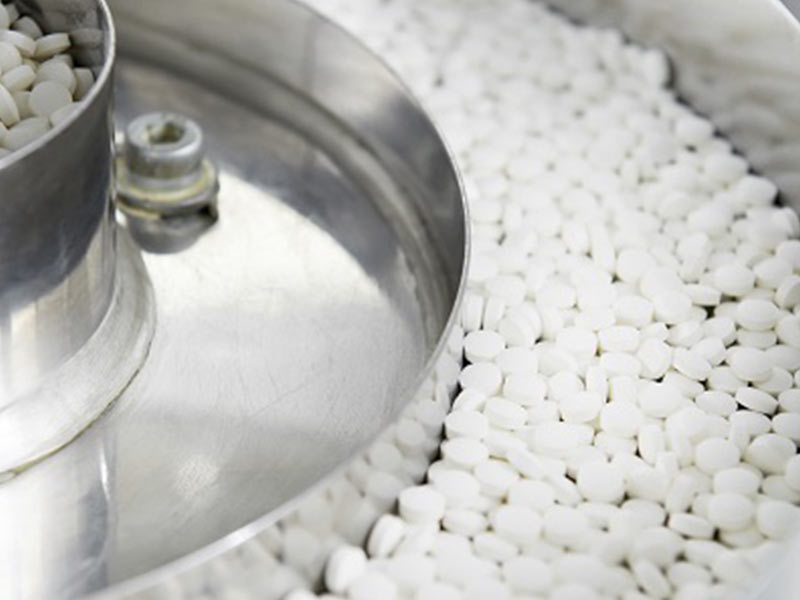
04
Chemical Characterization, Production And Control In Oral Solid Dosage Forms
3 Formulation Development
- Formulation selection (components and composition) based on RLD formulation andin-house study.
- Define initial process (platform) forpreparation of prototype generic drug product (DP),
- Define the initial specifications for DP, including logo and number artwork preparation on the surface of the drug product.
- Produce one (or more) small research and development DP batch and test the product according to finished product specifications, including the evaluation of DP impurity profile and perform dissolution profile study compared with the RLD product.
- Place the DP on accelerated stability study (up to 3 months) to evaluate the stability of the formulation developed.
- Analytical method validation or verification, including forced degradation studies on DP to demonstrate that the analytical method used is stability-indicating.
- Selection of container closure system (CCS), including component resin, specification, test methods, supplier ’s DMF.
CGMP Specifications That Meet Regulatory Requirements
- Properly document study results and preparation of DP formulation development report or summary to support the formulation for further
- Preparation of proper analytical method validation or verification protocol and final report.
- Vendor qualification, including full testing on the first three lots of CCS.
Note: CCS which has been used in FDA approved drugs is highly recommended.
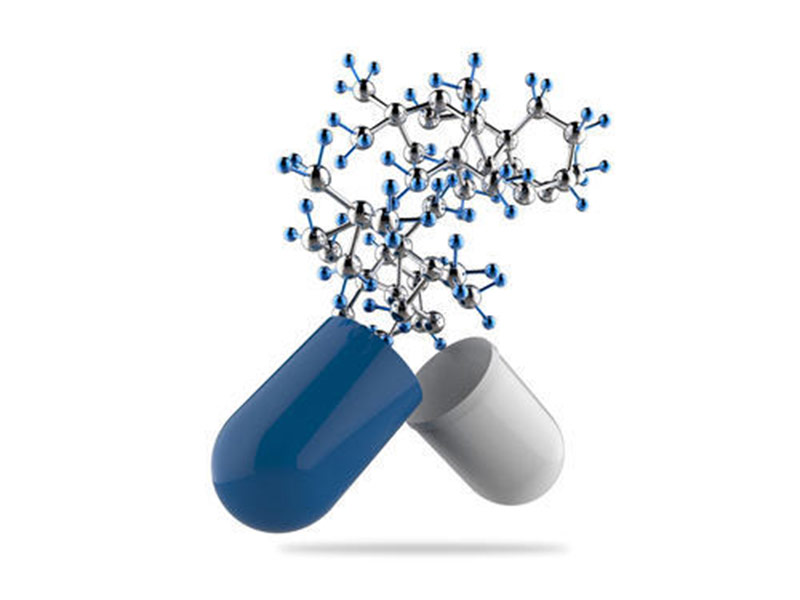
05 Chemical Characterization,Production And Control In Oral Solid Dosage Forms
Process Understanding, Characterization And Optimization (Scale-up)
- Identification of the critical parameter(s) in each unit operation and implement in-processcontrol ranges, such as :
- Blend content uniformity (BCU) issue (Is the blending time critical? What is the sampling plan and sampling method to monitor BCU? What are the analytical method and acceptance criteria for BCU? Etc.
- LOD in dry process (time, temperature, etc.)
- Weight variation control in tablet compression
- Several development batches in varies batch sizes may be produced for research and development purpose. Adequate experimental data should be collected to support any critical parameters identified and in-process control ranges used in scale-up process.
- The final DP specifications should be established.
CGMP Specifications That Meet Regulatory Requirements
- Document justification on critical parameter identification and their in-process control ranges.
- Preparation of product and process development report or summary to support the critical parameters identified and their in-process control ranges used for pilot batch and commercial batch manufacture.
06 Chemical Characterization, Production And Control In Oral Solid Dosage Forms
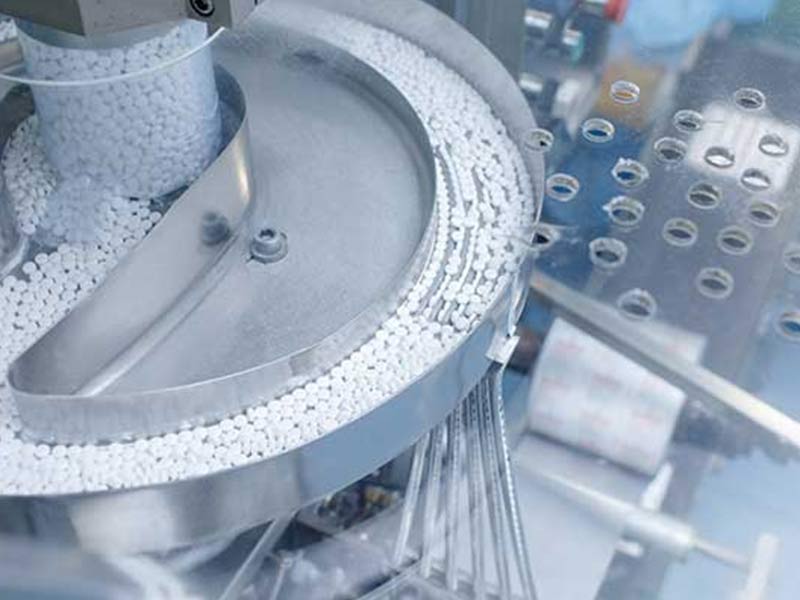
- Engineering or Demonstration Batch Manufacture
- Preparation of batch record (BR) for Engineering ordemonstration batch manufactur
- Reviewing drafted BR and ensuring the critical parameter(s) are adequately identified and the in- process control ranges are properly implemented.
- A comprehensive sampling plan should beconsidered to collect more data at this scale.
- The batch size should be at least 100,000 tablets or 10% of proposed commercial batch size.
- It is highly recommended that engineering or demonstration batch be produced by using commercial manufacturing equipment.
- The final DP release tests should meet established specifications.
This engineering or demonstration batch manufacture could be optional depending upon the research and development study performed and related manufacturing experience a firm has.
CGMP Specifications That Meet Regulatory Requirements
Validation Master Plan (VMP) for the specified product should be prepared at this stage. It should be served as a “ road map ” to start qualification and validation works related to the product.
- Following work should be completed according VMP before demonstration batch or pilot batch preparation:
- Qualification of related facilities and systems (such as, HVAC, waster system, etc) .
- Qualification ( DQ, IQ, OQ and PQ) of the equipment used in manufacturing of the DP.
- Preparation of equipment cleaning validation protocol.
- Analytical methods validation or verification.
07 Chemical Characterization, Production And Control In Oral Solid Dosage Forms
BE Pilot Study to gain information on bio-equivalent of in-house product.
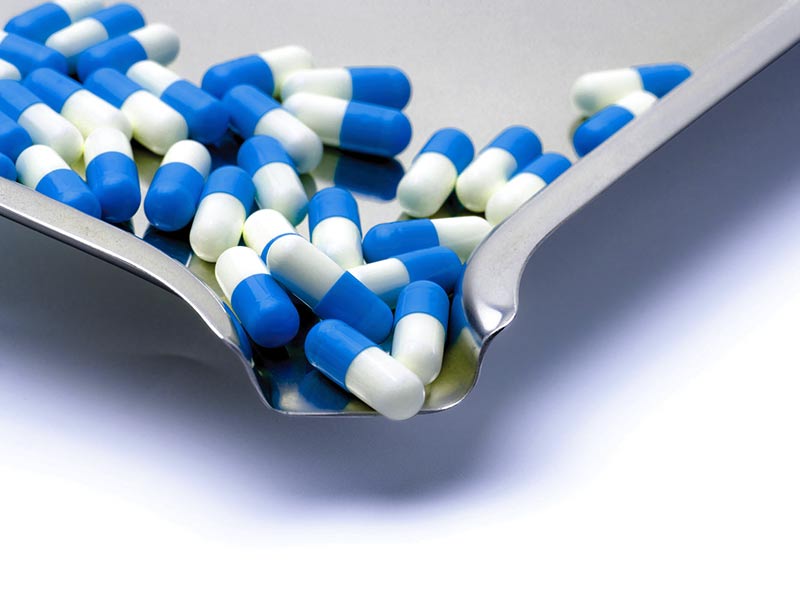
- Using the samples from engineering ordemonstration batch.
- 3 –5 persons compared with RLD.
This is also an option.
08 Chemical Characterization, Production And Control In Oral Solid Dosage Forms
Bio-batch Or Submission Batch Preparation
1. Manufacturing a bio-batch or submissionbatch under CGMP controls.
- Executed batch record should include yield in each unit operation, final DP units manufactured and packaged, as well as batch reconciliation data and draft label.
2. Bio-batch release testing and issue COA.
- Dissolution profile (12 units and 5 timepoints) compared with RLD batch.
- Tested according established specification
3. Establish stability protocol.
- Testing time points (0,1,2,3M for acceleratedand 0,3.6.9.12.18.24 for long-term conditions)
- Intermediate condition if necessary
- Stability test attributes (Appearance, purity,related substances, dissolution, etc.)
4. Perform DP stability study as appropriate (at least 3 months under accelerated condition) for submission purpose.
CGMP Specifications That Meet Regulatory Requirements
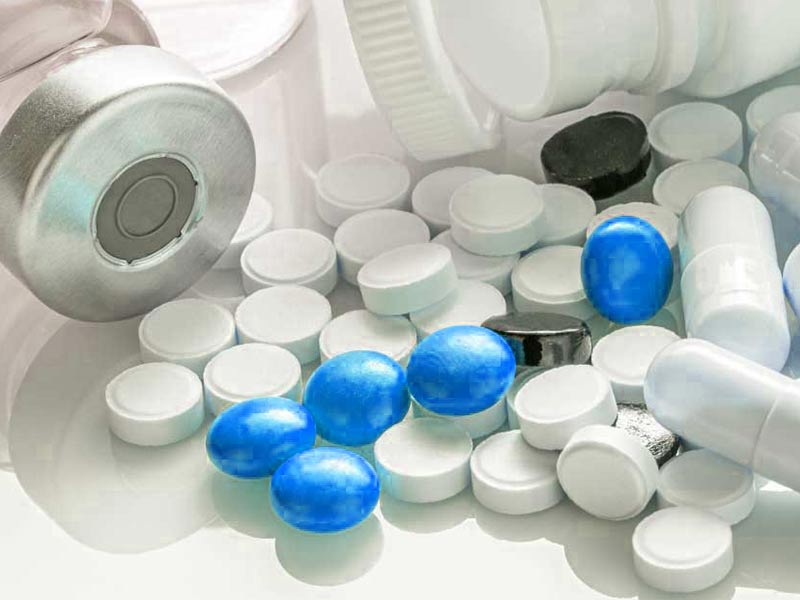
Preparation of final DP development report (or combination of pre- formulation, formulation and process development summaries)
Note:
This report will be served as the basis for preparation of Quality Overall Summary (QOS, 2.3 in CTD-format) and Pharmaceutical Development Section (3.2.P.2 in CTD-format) in ANDA submission
09 Chemical Characterization, Production And Control In Oral Solid Dosage Forms
- BE Study
- Using bio-batch or submission batch samples to compare with RLD
- 24 to36 patients, cross over studies.
CGMP Specifications That Meet Regulatory Requirements
- BE study should be conducted in a clinical laboratory which is in compliance with FDA GLP requirements.
10 Chemical Characterization, Production And Control In Oral Solid Dosage Forms
- Preparation of ANDA package for submission ANDA
- CTD-format should be used for preparation of an ANDA
11 Chemical Characterization, Production And Control In Oral Solid Dosage Forms
Preparation for Pre-approval Inspection (PAI)
CGMP Specifications That Meet Regulatory Requirements
- Preparation PAI from CGMP perspective by evaluating GMP systems on site.
- Preparation of process validation (PV) protocol, and may start or complete process validation by producing three consecutive conforming batches at commercial scale) and preparation validation report.
Note:
PV is not required to be completed for ANDA approval. However, validation protocol should be in place at the time of pre-approval inspection (PAI).