Blister Packaging Line
Senieer® provides high-precision blister packaging lines with advanced automation,
ensuring product safety, and compliance with industry standards.
Introduction of Blister Packaging Line
The intelligent linkage production line(blister packaging line) is composed of blister packaging machine and high-speed cartoner. It is a highly intelligent electromechanical integration equipment independently developed by our company with advanced German technology and years of packaging experience. Adopting a new design concept and applying Schneider most advanced Pac Driver motion control system, a fully servo driven real-time online detection and feedback closed-loop system. Realize seamless integration between blister packaging and cartoner, and achieve orderly packaging, middle packaging, Case Packing, stacking and other functions of aluminum plastic plates. Realizing a high-speed intelligent linkage production line for blister.
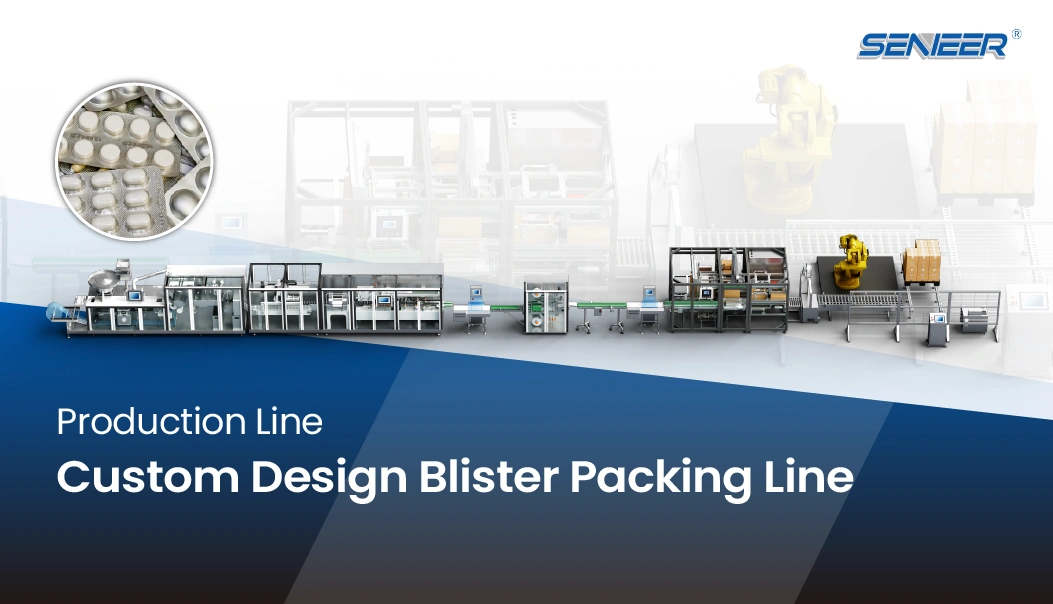
Enhance Productivity: Choose an Efficient Blister Packaging Line
The machines utilize intelligent control systems and high-efficiency forming technology to optimize production. Automated functions reduce human intervention, enhancing productivity and reducing errors. The modular design allows for easy maintenance and seamless integration with existing production lines. With advanced servo control and forming technology, Senieer’s blister packaging solutions ensure high-speed production and reliable quality.
Choose Your Blister Packaging Line
Blister Packaging Line is used to form, fill, and seal pharmaceutical products in pre-formed blisters. These machines ensure product integrity, extend shelf life, and provide tamper-proof packaging, making them ideal for the pharmaceutical, nutraceutical, and food industries. Senieer’s Packaging Lines support PVC/ALU, PVDC/ALU and ALU/ALU materials to meet diverse packaging needs..
Roller Sealing Blister Packing Machine: Uses continuous roller heat sealing for high-speed production.
Plate Sealing Blister Packing Machine: Uses a flat plate to apply heat and pressure for sealing, ideal for precise packaging.
The process of blister packaging line is usually as the following: blister forming station, product feeding system, dealing unit, punching system, printing & embossing, inspection & reject System, cartoning machine, end-of-line solutions.
Guidelines For Blister Packaging Line
Senieer’s blister packaging line provides industry-leading precision and efficiency. Key benefits include:
- High Accuracy Forming and Sealing: Advanced forming and sealing technology ensures precise product placement and protection.
- Multi-Industry Applications: Suitable for pharmaceutical, nutraceutical, and food industries.
- Flexible Packaging Mechanisms: Supports PVC, PVDC, PP and Alu-Alu materials.
- Automated Feeding, Sealing, and Cutting: Ensures continuous operation with minimal human intervention.
Working Process Of Blister Packaging Line
- blister forming Mechanism
The first stage of the blister packaging process involves forming cavities in plastic or aluminum foil using Negative Pressure or Positive Pressure Forming and heat. This process creates a protective barrier around tablets and capsules.
- Product Feeding System
Once cavities are formed, the product feeding system accurately places tablets or capsules into each blister pocket using vibratory or brush feeders. This ensures precise and contamination-free filling.
- Sealing Unit
After filling, the sealing unit applies heat and pressure to seal the blisters with aluminum foil or other lidding material, ensuring product protection.
- Punching System
The sealed blister sheets are cut into individual blisters through a high-speed punching system, ensuring uniform shape and size.
- Printing & Embossing
Blisters can be printed with batch numbers, manufacture date , and expiry dates, using an integrated printing and embossing system. This step ensures product traceability and regulatory compliance.
- Inspection & Reject System
A vision inspection system checks blisters for missing or broken tablets and removes defective packs, maintaining high product quality.
- Cartoning Machine
Blister packs are fed into the automatic cartoner, which inserts them into pre-folded cartons, applies leaflets, and seals the cartons for final packaging.
- End-of-Line Solutions
Additional equipment such as case packers and palletizers can be integrated for a fully automated blister packaging line, ensuring high efficiency and minimal labor requirements.
Features Of Blister Packaging Line
- High-speed operation for increased productivity
- Precise optical sensor technology for accurate product feeding
- Compact design for space efficiency
- Servo-driven automation for reliability
- cGMP and FDA compliance
- Customizable configurations for diverse product requirements
Advantages Of Blister Packaging Line
Product Integrity:
- Protects against environmental factors that could reduce shelf life.
Tamper Resistance:
- Prevents external contamination and interference before use.
- Any tampering is easily identifiable.
Cost Efficiency:
- More affordable than alternative packaging methods, such as plastic containers.
- Does not require variable adjustments for different products.
Dose Accuracy:
- Ensures precise dosing by isolating each tablet or capsule in its own cavity.
- Helps prevent accidental overdosing.
Ease of Identification:
- Clearly displays product name, expiration date, and lot number for easy tracking.
Main materials Used In Blister Packaging Line
Blister packaging consists of four primary components:
Forming Film:
- Makes up 80–85% of the blister package.
- Chosen based on product weight, sharp edges, impact resistance, cost, and compatibility.
- Other factors include migration, aging, heat sealing properties, and ease of trimming.
Heat Seal Coating:
- Creates a bond between the lidding material and the plastic blister.
- Must have good gloss, abrasion resistance, clarity, and hot tack to ensure proper sealing.
- Supports the weight of the blister package.
Printing Ink:
- Provides branding and visual appeal.
- Must withstand heat up to 300°C without discoloration or tackiness.
- Should resist fading, bending, and abrasion.
- Must comply with FDA regulations for safety.
Blister packaging is a crucial solution for industries that require secure, tamper-proof, and cost-effective packaging solutions.
Different Types
Item | Roller Type | Plate Type | Plate Roller Type |
Forming Type | -Roller Type Mold | -Plate Type Mold | -Plate Type Mold |
-Negative Pressure Forming | -Positive Pressure Forming | -Positive Pressure Forming | |
Forming Pressure | small | Large | Large |
Forming Area | Forming area is small | Forming area is Large | Forming area is Large |
Forming depth is shallow | Forming depth more than 30 mm | Forming depth more than 12 mm | |
Sealing Type | Roller-type heat sealing | Plate-type heat sealing | Roller-type heat sealing |
Utilizes line contact | Utilizes surface contact | Utilizes line contact | |
Lower overall sealing pressure | Higher overall sealing pressure | Lower overall sealing pressure | |
Foil Delivery Type | Continuous – Intermittent | Intermittent | Intermittent – Continuous – Intermittent |
Production Capacity | Moderate production capacity | High production capacity | High production capacity |
Low punching frequency | Low punching frequency | High punching frequency |
How To Choose It?
When selecting a blister packaging line, consider factors such as:
- Type and size,shape of tablets/capsules
- Packaging material (PVC, PVDC, PP, Alu-Alu)
- Production speed and capacity requirements
- Compliance with regulatory standards
- Integration with existing production lines
Senieer’s professional team will help design and manufacture blister packaging lines that maximize efficiency and ensure regulatory compliance. Contact us today to find the best solution for your manufacturing needs!