Home » Capping Machine
Capping Machine
Accurately locking each bottleSenieer® capping machine provides stable sealing for your products, improves production efficiency and quality
Introduction Of Capping Machine
Capping machine is a kind of equipment specially used for sealing bottles, it suits for plastic bottles and glass bottles. It is widely used in beverage, pharmaceutical, cosmetics and chemical industries to ensure the sealing and safety of products. Currently Senieer equipment can seal caps with a maximum diameter of 65mm,if it exceeds 65 mm, you need to customize it. It is a key equipment to ensure product sealing and production efficiency. In order to meet production lines of different sizes and needs, Senieer provides multiple models of capping machines, covering a full range of applications from small batch production to large-scale automation.
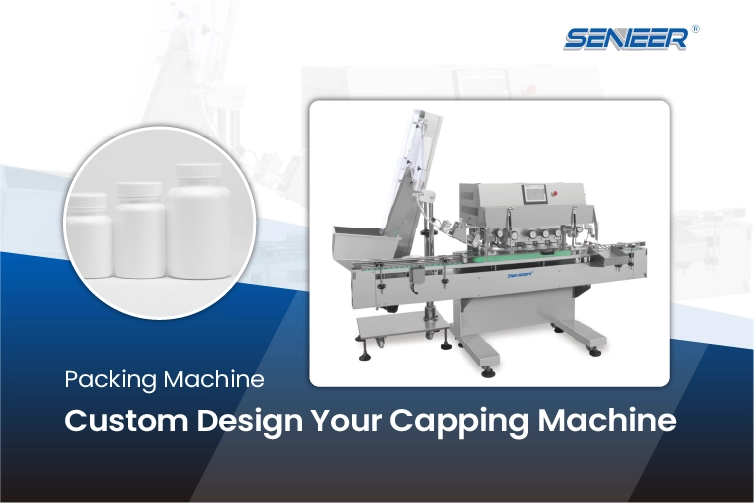
Different Types Of Capping Machine
Capping machines come in various types, each designed to meet specific requirements based on cap style, container type, and production scale.
Choose Your Capping Machine
The wide application of capping machines makes them one of the core equipment in many industries such as pharmaceuticals, nutrition, food, cosmetics, etc. Different industries have different requirements for sealing, efficiency and stability of capping. Senieer capping machines meet various needs with customized service and excellent performance.
The process flow of the capping machine directly affects the accuracy, speed and stability of production. The capping machine Senieer provided not only has an efficient capping process, but also integrates intelligent and precision control to ensure that each bottle cap can achieve the ideal tightness.
Guidelines For Capping Machine
A capping machine is an industrial device designed specifically for sealing caps to containers such as bottles, jars, or vials, which helps maintain product integrity, and prevent contamination. As an indispensable part of the automated packaging line, the capping machine improves the sealing performance and production efficiency of bottled products. This guide not only covers technical details, but also provides solutions for different production needs, making it easier for you to select right capping equipment and empower your company’s production.
Advantages Of Capping Machine
1. No need to replace parts
This machine only requires adjustment of the timing belt, cap wheel spacing, and the height of the frame to adapt to various bottle sizes within the applicable range without the need to replace parts.
2. Compliant with GMP standards
The high-speed capping machine is an automatic packaging equipment designed strictly in accordance with national GMP standards and process requirements. The main drive part of the machine is placed inside the casing, avoiding contamination of the material due to wear and tear of the transmission mechanism. All parts that come into contact with the material have been highly polished.
3. Lightweight and easy to handle
This machine is equipped with safety protection devices such as no-cap stop and cap-on start-up. Most of the components of the entire machine are made of aluminum alloy materials, and the housing is made of high-quality stainless steel plates, achieving a lightweight design and easy handling.
Working Principle
The machine primarily utilizes two synchronous belts to hold and convey the bottle bodies. Meanwhile, four sets of highly elastic and wear-resistant rubber wheels are employed to rotate the bottle caps, thereby achieving the capping objective. This design ensures that the bottle bodies are not easily scratched, and the bottle caps are not easily damaged. Within its applicable range, the machine allows users to adjust freely according to the height and size of their specific bottle caps, as well as the height and size of the bottle bodies. The motors for clamping bottles, capping, cap orientation, and conveying are all controlled by imported brand frequency converters. Users can freely set the production volume within the machine’s design range, providing greater convenience for production scheduling and process formulation.
Main Performance Characteristics Of Capping Machine
1. Independent cap lifter:
Automatic cap sorting, equipped with a block cover photoelectric control start-stop mechanism, and an automatic anti-cap drop-off mechanism to ensure no anti-cap enters the cap drop track
2. Modularized cap drop track:
Easy to adjust and disassemble, equipped with a cap detection photoelectric control bottle motor to ensure that bottles have a cap before entering the capping station;
3. Equipped with a position display
the cap drop track and capping wheel adjustments are clearly visible, making adjustments and recording convenient.
4. Capping anti-over-tightening function (capping friction plate);
5. The capping motor, bottle-clamping motor, conveying motor, cap sorting, and cap pressing motor are all driven by Siemens frequency converters, ensuring stable operation and easy adjustment, with frequency settings available on the touchscreen;
6. Standard triple detection for defects is equipped, effectively detecting and rejecting defective caps such as crooked caps, loose caps, missing caps, missing aluminum foil, and inverted bottles. The through-beam photoelectric sensor uses the ultra-thin model from Keyence of Japan, which requires no adjustment and has a high metal housing protection level;
7. The work surface is equipped with an acrylic protective cover, effectively protecting the high-speed rotating wheel assembly and bottle-clamping belts;
8. Standard three-level permission management is provided, with data acquisition functionality预留 at the terminal;
9. Optional servo torque detection function can be equipped.
Purpose and Importance Of Capping Machine
The primary purpose of a capping machine is to seal caps or lids to containers, ensuring a tight and secure seal that preserves the contents.
- Product Preservation: A well-sealed container protects its contents from environmental factors like air, moisture, and contaminants. In industries such as food and pharmaceuticals, preserving the product’s integrity is vital to prevent spoilage or contamination.
- Safety and Compliance: For certain industries, particularly pharmaceuticals and chemicals, product safety and compliance with regulations are paramount. Capping machines ensure each container is adequately sealed to meet industry standards and safety requirements.
- Quality Assurance and Brand Integrity: Consistent capping maintains the consistency of brand’s image and ensures customer satisfaction. A well-capped product looks professional and assures customers of its quality.
- Improved Production Efficiency: Automated capping machines allow for high-speed and continuous production, reducing the need for manual labor and minimizing errors. This efficiency is especially beneficial in industries with high production demands, such as beverages or personal care products.
How Does Capping Machine Work?
The operation of a capping machine varies based on its design and the type of cap it applies.
- Container and Cap Feeding: Containers are fed onto a conveyor that transports them to the capping station. Caps are also fed into the machine through a cap feeder or an elevator, ensuring a steady supply of caps ready for application.
- Placement and Positioning of Cap : Once the containers reach the capping station, caps are placed on the container openings. Advanced machines use sensors and alignment systems to ensure that each cap is correctly positioned before sealing begins.
- Cap Application: The machine applies the cap using torque-controlled mechanisms, such as chuck or spindle capping, depending on the machine type. Torque control is crucial for securing the cap tightly without damaging the container or cap itself. Machines can be adjusted for different cap sizes and container shapes to maintain consistency.
- Quality Control and Inspection: Many modern capping machines incorporate inspection systems to ensure that each cap is tightly sealed. If a cap is incorrectly applied, the machine rejects the container, thus ensuring quality control standards.
- Finishing and Conveying: Once capping is complete, containers are transported out of the capping station for further packaging steps, such as labeling or boxing.
Application
Capping machines are versatile tools used across multiple industries due to their ability to adapt to various container shapes, cap types, and production requirements.
- Pharmaceutical
- Food and Beverage Industry
- 3. Cosmetics industry
- Chemical industry
- Daily chemical industry
Choose Your Interested Production Line
Bottle Filling Line
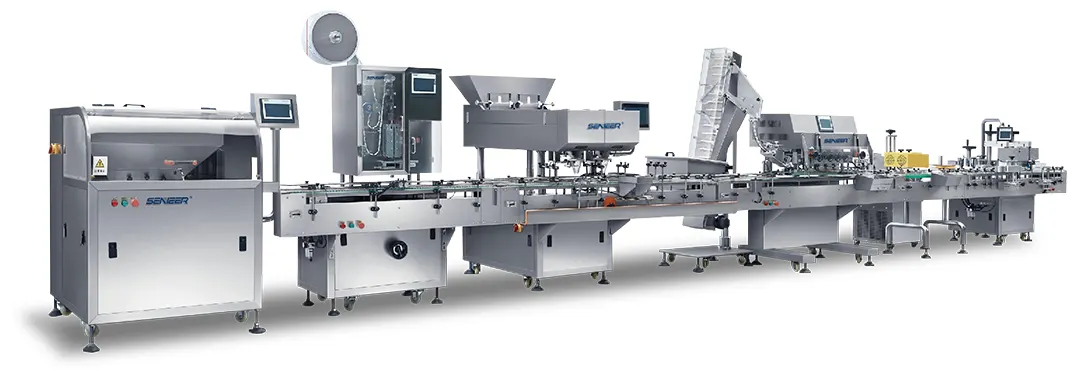
Granulation Line
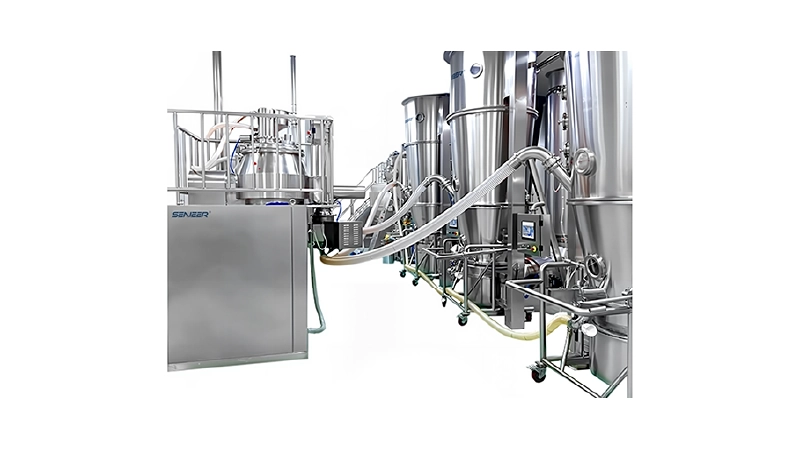
Blister Packaging Line
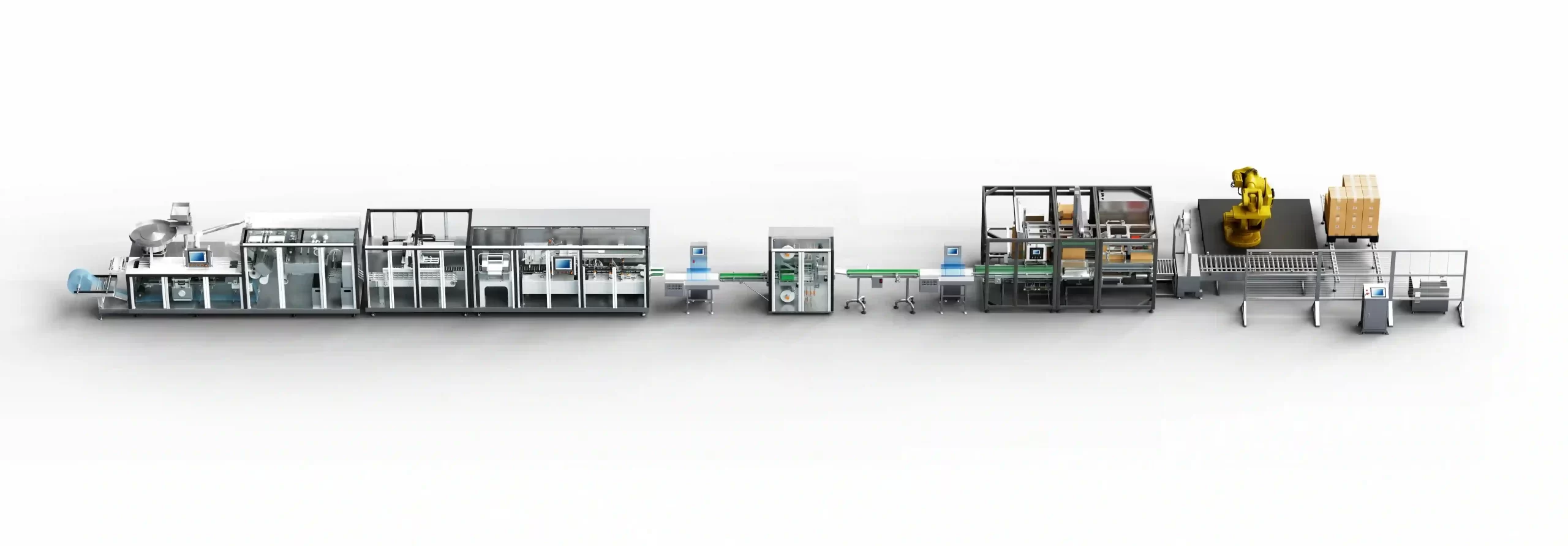
Powder Filling Line
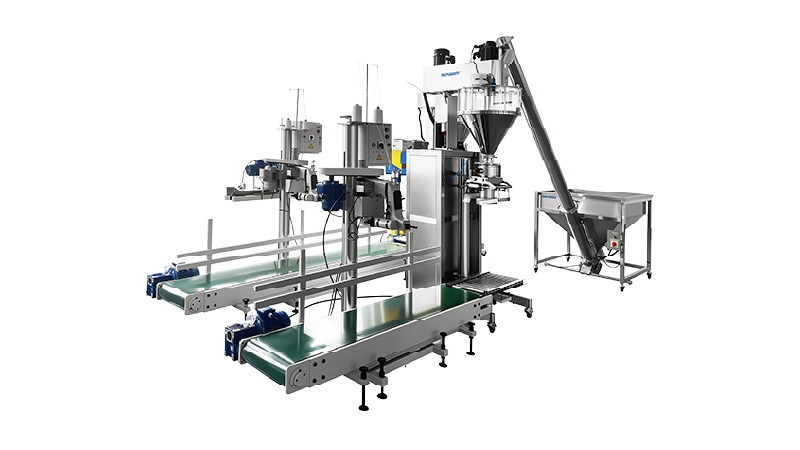