Clean Room Ducting
In high-standard clean room environments, clean room ductwork is the core to ensuring air circulation, contamination control and product quality. Senieer® clean room ducting uses high-quality materials and advanced technology to fully meet the stringent requirements of different industries.
Introduction Of Clean Room Ducting
Clean room ducts are an integral part of the clean room environment. They are responsible for transporting air, gases, liquids and other necessary substances. In clean rooms, piping systems need to meet high standards of design to ensure they do not pollute the clean environment. The selection, layout, and maintenance of ductwork are critical to maintaining clean room cleanliness, which directly affecting cleanliness control, system efficiency, and long-term stability of the equipment.
Different clean rooms have different requirements for piping materials, depending on industry standards, application needs and environmental conditions. Choosing appropriate pipe materials not only ensures smooth air circulation and safe transportation of gases and liquids, but also effectively avoids the accumulation of pollutants and the growth of microorganisms.
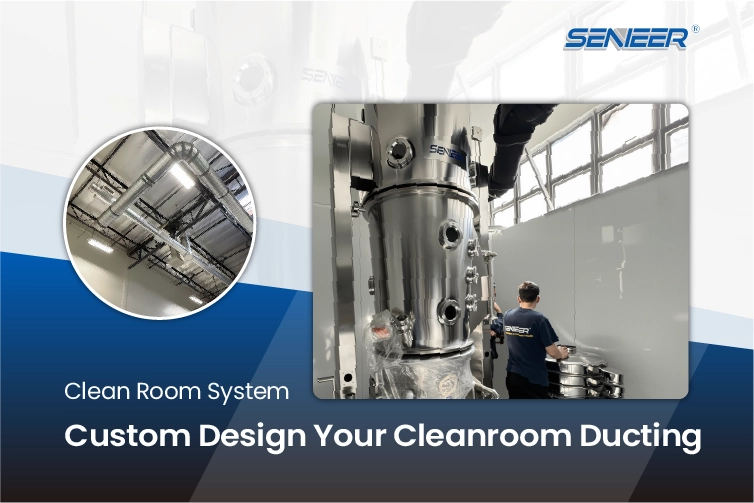
Different Types Of Clean Room Ducting
Senieer offers customized service. If you have specific demands, please let us know, Senieer can custom design for you.
Choose Your Clean Room Ducting
The application of clean room ducts in various industries is crucial. It not only ensures the smooth flow of air and gas, but also plays a role in pollution control and maintaining a clean production environment. The design and functions of clean room piping systems vary according to the specific needs of different industries, and they must meet the strict requirements of cleanliness, hygiene, safety and production efficiency in each industry. Next, is the introduction of the specific applications of clean room piping in different industries such as pharmaceuticals, electronics, food, and medical to help you understand the special needs and solutions of each industry. Senieer clean room ducting is suitable for gas pipeline, material pipeline, etc.
The process design of clean room pipelines is the basis for ensuring the stable operation of a clean environment and involves many aspects such as pipeline material selection, layout, installation and maintenance. The correct process can not only effectively control the spread of contaminants, but also improve the operating efficiency and reliability of the system. The requirements for piping processes will vary based on different clean room standards and industry needs.
Guidelines For Clean Room Ducting
This guide will delve into the key aspects of clean room ducting system design, material selection, installation and maintenance. Clean room ducts are the core component to ensure the stable and efficient operation of a clean environment. Their design not only affects air circulation and air flow control, but is also directly related to the prevention and control of pollutants during the production process. Whether in pharmaceuticals, electronics, food or other demanding industries, understanding clean room piping is critical to establishing a clean room environment that meets standards.
Introduction
Clean room ducting refers to the system of ducts and associated components used to distribute filtered air throughout a clean room environment. It plays a crucial role in maintaining the required air quality and cleanliness standards by ensuring the even flow of purified air while preventing contamination from external sources.
Key Elements Of Clean Room Ducting
The design and maintenance of clean room ducting systems are key to ensuring stable and efficient operation of the clean environment.
Material selection
The materials of clean room pipes must meet anti-pollution requirements. Commonly used materials include:
- Stainless steel: It has good corrosion resistance and easy cleaning, and is suitable for high-demand clean rooms, such as pharmaceuticals, food processing and other industries.
- Galvanized steel: used in some clean room environments with low requirements, lower cost, but not as corrosion-resistant as stainless steel.
- Plastic (such as PVC, PE): suitable for transmitting non-corrosive gases or liquids, has good corrosion resistance, and is widely used in some lower-level clean rooms.
Pipeline design and layout
- Fluid control: Pipe design needs to ensure smooth flow of air and reduce resistance and pressure loss. Avoid excessive turns and intersections to keep the system efficient.
- Zoning design: According to the needs of different areas of the clean room, rationally plan the piping system to ensure that the cleanliness requirements of each area are met.
- Flow direction and airflow management: When designing the duct layout, the direction and speed of the airflow should be considered to ensure that the air flow in the clean room helps to discharge particles and pollutants.
Sealing
The connections and joints of theclean room ducting system must have good sealing properties to avoid leakage and the penetration of external contaminants. Every connection point in the duct system should be rigorously tested to ensure that the air flow is not contaminated by the outside world.
Easy to clean
The inner wall of the pipe should be smooth and without dead corners to facilitate cleaning and disinfection. Since the air and gas in the clean room may contain trace amounts of pollutants, the smoothness and cleanliness of the inner wall of the pipeline directly affects the cleanliness level of the system.
Filtration system
Clean room ductwork is often equipped with high-efficiency filters (such as HEPA or ULPA filters) to filter airborne particles and bacteria. The design and installation location of the filter are crucial to ensure that the air can be effectively purified as it passes through the duct to meet the air quality requirements of the clean room.
Pipeline support and isolation
Piping systems need to be secured to avoid vibration or movement during work. Especially in environments with high cleanliness requirements, vibrations in pipes may cause uneven air flow or the release of pollutants.
Temperature and humidity control
For some specific clean room environments, such as pharmaceuticals, electronics manufacturing, etc., the piping system also needs to be equipped with a temperature and humidity control system to ensure that the air reaches specific temperature and humidity requirements and avoid air quality problems caused by changes in temperature and humidity.
Regular maintenance and monitoring
Duct systems need to be cleaned, inspected and disinfected regularly to prevent the build-up of contaminants. Regular airflow testing and tightness inspections ensure that duct systems remain compliant with clean room requirements and avoid potential contamination risks.
Comply with industry standards and regulations
The design, installation and maintenance ofclean room ducting systems should comply with relevant industry standards and regulations, such as GMP, FDA and ISO standards. These standards specify performance indicators that piping systems must meet to ensure product quality and employee safety.
Application
Clean room ducting plays a vital role in different industries as it not only affects air circulation but is also directly related to contamination control and product quality.
Pharmaceutical industry
In the pharmaceutical industry, clean room ductwork is used to ensure a dust-free, sterile environment for the production of high-quality drugs and medical devices. Pharmaceutical production environments must strictly control particles, bacteria and other contaminants in the air, and clean room duct systems help achieve this goal through efficient filtration and airflow management.
- Air filtration: Remove airborne particles and pathogens through HEPA or ULPA filters.
- Air flow control: Ensure the proper direction and speed of air flow to avoid cross-contamination.
- Sterility requirements: The design of the pipeline system requires no dead corners and no dust accumulation to reduce the accumulation of pollutants.
Electronics industry
In the electronics industry, especially in the manufacturing of semiconductor and microelectronic products, clean room ductwork is critical. Electronic components are particularly susceptible to the effects of tiny particles in the air, and any particle contamination can cause product failure.
- Particle control: Strictly control the concentration of particles in the air through the clean room duct system.
- Humidity and temperature control: Certain electronic manufacturing processes require precise temperature and humidity conditions, and ductwork systems coupled with air conditioning and dehumidification systems provide a stable environment.
- Cleanliness standards: The piping system ensures that the clean room meets the requirements of the ISO 14644-1 standard.
Food processing industry
In the food processing industry,clean room ducting systems are used to ensure the hygiene and safety of the food production environment and prevent microbial contamination and foreign matter from entering the production line. Whether during the processing, packaging, or storage stages, piping systems need to maintain strict hygiene standards.
- Air Purification: Clean room ducting helps filter microorganisms and contaminants from the air.
- Airflow management: Design reasonable air flow paths to prevent air pollutants from spreading to other areas.
- Hygiene requirements: The materials and design of the piping system need to be easy to clean and disinfect to ensure the hygiene of the food production environment.
Medical equipment manufacturing industry
Medical device manufacturing requires a high degree of cleanliness, as any tiny contamination may affect the safety and effectiveness of the device. Clean room duct systems are used to ensure air quality and prevent microorganisms, dust and other sources of contamination from entering the production area.
- Air quality management: Control particulate matter and bacteria in the air through a high-efficiency filtration system.
- Sterile environment control: The pipeline design must meet the standards of aseptic production to avoid the accumulation of contaminants.
- System maintenance: regular cleaning and testing to ensure long-term and efficient operation of clean room pipelines.
Do your factory have the need for clean room ducting? If you have or want to learn more information about it, please feel free to contact us.
Choose Your Interested Production Line
Bottle Filling Line
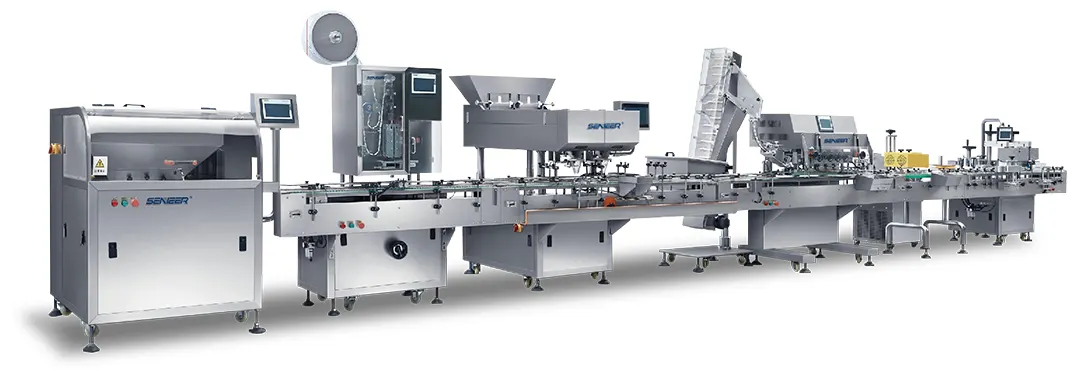
Granulation Line
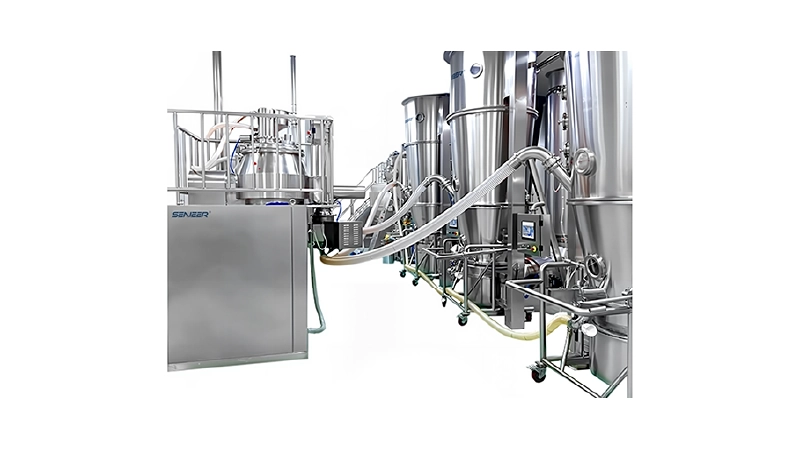
Blister Packaging Line
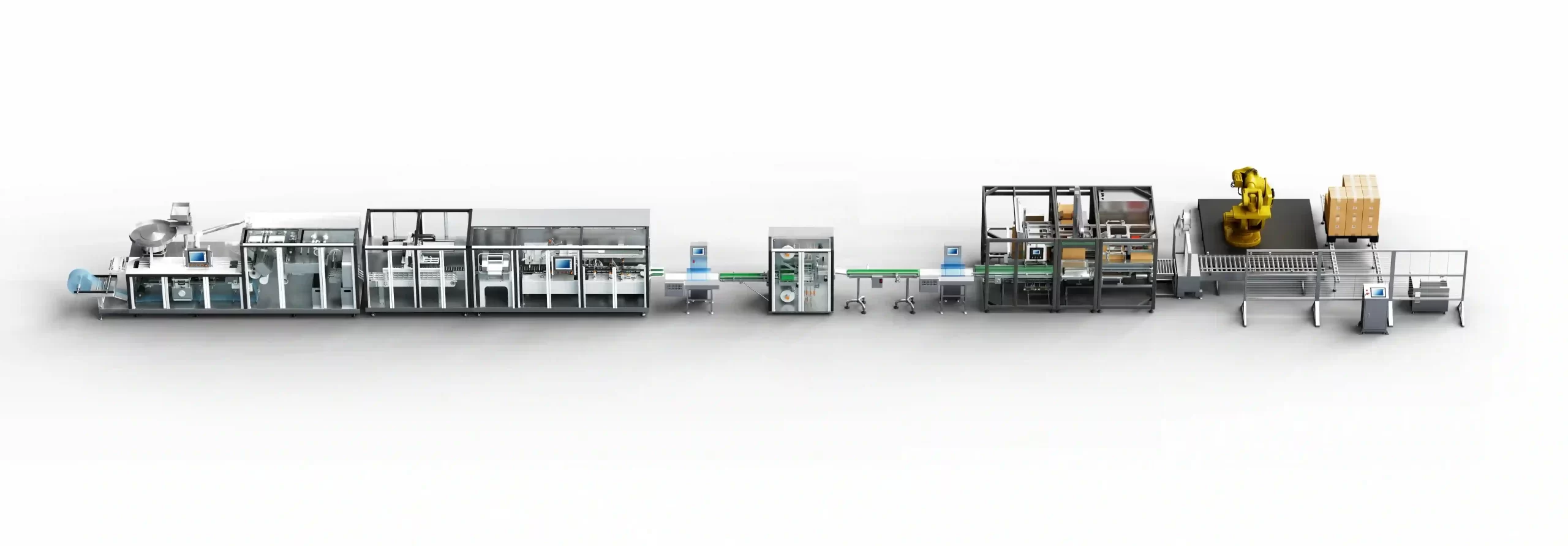
Powder Filling Line
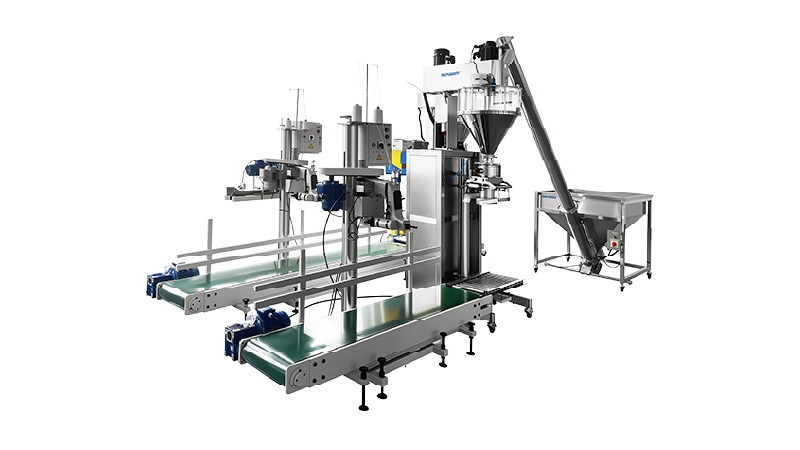