Clean Room Floor
Dust-free and germ-free. Epoxy and PVC are available
Designed to meet strict hygiene standards, Senieer® clean room floors offer excellent chemical resistance, abrasion resistance and ease of cleaning, ensuring your production process runs smoothly and hassle-free.
Introduction Of Clean Room Floor
A clean room floor refers to a specialized flooring system designed for use in clean rooms, which are controlled environments where pollutants such as dust, airborne microbes, and chemical vapors are minimized. These floors are essential in industries that require stringent cleanliness standards, such as pharmaceuticals, nutrition, biotechnology, electronics, and aerospace, etc.
In modern industries and laboratories, clean room floor is an important part of ensuring a clean environment and product quality. With the continuous improvement of clean room standards, different kinds of clean room floor have appeared on the market to meet the needs of different industries and applications. These floors not only provide excellent cleaning performance and chemical resistance, but also effectively control static electricity to ensure safe and efficient production processes.

Different Types Of Clean Room Floor
Senieer offers customized service. If you have more detailed specifications, please offer to us, Senieer can custom design for you.
Choose Your Clean Room Floor
Clean room floor plays a vital role in various industries, especially in environments where strict control of contamination and high levels of cleanliness are required. Whether in the pharmaceutical, electronics, aerospace or food processing industries, clean room floors are designed and materials designed to meet specific industry standards and requirements. Not only do they provide a safe, hard-wearing work surface, they also effectively resist chemicals contamination, reduce static electricity and prevent the build-up of particulate matter. Next, we will discuss the specific applications of clean room floor in different fields and gain an in-depth understanding of its importance in improving production efficiency and ensuring product quality.
Clean room floor’s craftsmanship is key to ensuring it operates effectively in a clean room environment. Not only do these floors need to meet strict hygiene standards, they must also be durable, chemical resistant and easy to clean. During the design and construction process, the choice of technology directly affects the performance and service life of the floor. Generally, the process of clean room floor involves many aspects such as material selection, surface treatment and installation technology.
Guidelines For Clean Room Floor
Welcome to read this product guide, which aims to comprehensively introduce the key features, models, processes and applications of clean room floor in various industries. As the requirements for clean room environments continue to increase, choosing a suitable clean room floor is essential to ensure production quality and maintain environmental hygiene. This guide will provide you with in-depth insights, including the pros and cons of different models, process flow details, and specific application examples in industries such as pharmaceuticals, electronics, food, and more. Whether you are a purchasing decision maker or an industry professional, this guide will help you find the best clean room floor solution for your needs.
Introduction
A clean room floor is a specialized flooring system designed specifically for clean room’s—controlled environments where the concentration of airborne particles, contaminants, and other pollutants must be minimized. These floors are essential in various industries, including pharmaceuticals, biotechnology, electronics, aerospace, and food processing, where cleanliness and contamination control are critical.
Features Of Clean Room Floor
Clean room floor plays a vital role in modern industry and scientific research, especially in industries such as pharmaceuticals, electronics, and food processing. These flooring systems not only ensure a clean working environment, but also play an important role in preventing contamination and improving production efficiency. The main features of clean room floor are described in detail below.
1.Smooth surface
Clean room floors are usually designed with a smooth surface to prevent the accumulation of dust and particles. The smooth surface not only facilitates cleaning, but also reduces the growth of bacteria and other microorganisms, ensuring a hygienic production environment. This design makes the cleaning process more efficient, reducing the use of detergent and water.
Chemical resistance
In many industrial settings, floors can be exposed to a variety of chemicals and solvents. The materials used in clean room floors generally have excellent chemical resistance and can withstand the attack of common chemicals. This feature ensures that the floor is less susceptible to damage in the event of a chemical spill, extending its service life and reducing maintenance costs.
Static electricity control
Electrostatic discharge (ESD) can cause serious damage in the electronics and precision manufacturing industries. Many clean room floors incorporate anti-static materials or coatings to reduce the risk of static electricity build-up. This design protects sensitive equipment and components and ensures the safety and stability of the production process.
Wear resistance
Clean room floors must be able to withstand frequent walking and equipment use and have good wear resistance. High-quality clean room floors can withstand the weight of heavy objects and constant friction, maintaining good appearance and performance. This feature allows clean room floor to maintain a long service life in high-traffic working environments.
Easy to clean
Clean room environments require strict hygiene standards, so the clean room floor must be designed with ease of cleaning in mind. The floor’s materials and surface treatment enable it to withstand high frequency cleaning and disinfection, reducing the risk of contamination. Even when demanding cleaning is required, these floors remain clean and tidy, meeting industry standards.
Anti-slip properties
In a clean room, safety is a key factor. Clean room floors feature non-slip surfaces to reduce the risk of slips and falls. This is critical for employee safety and product integrity, especially in humid or high-use environments where cleaning agents are used.
Adaptable
The design of clean room floor usually takes into account the needs of different application scenarios. Depending on the industry, flooring thickness, material and color can be adjusted to meet specific job requirements. For example, the pharmaceutical industry may require thicker, more chemical-resistant flooring, while the electronics industry may focus more on anti-static properties.
How Does Clean Room Floor Work?
Clean room floor plays a vital role in a clean room environment, aiming to control and reduce the presence of particles, microorganisms and other contaminants in the air. Understanding the working principle of clean room floor can help us better understand the importance of its design, material selection and maintenance.
Smooth surface and non-porous structure
The surface of a clean room floor is usually smooth and non-porous, which makes it less likely for particles and contaminants to accumulate on its surface. The smooth design not only facilitates cleaning, but also reduces the growth of dust and microorganisms. The non-porous structure prevents liquid penetration and ensures floors are less susceptible to staining, keeping the cleaning process efficient and effective.
Material selection
The materials used in the clean room floor are critical to its performance. Common materials include:
- Epoxy: This material is wear-resistant and chemical-resistant, making it suitable for high-traffic work environments. Epoxy floors have a smooth surface and are easy to clean and disinfect.
- Polyvinyl chloride (PVC): PVC flooring has good chemical resistance and antibacterial properties, making it suitable for places where strict pollution control is required.
Static electricity control
In many industries, electrostatic discharge (ESD) can cause damage to electronic equipment and sensitive materials. Clean room floors usually use anti-static materials or coatings that can effectively dissipate static electricity, thereby protecting equipment and products from damage. This static control feature is an important consideration in clean room design.
Cleaning and Maintenance
An effective cleaning and maintenance process is critical to maintaining the performance of your clean room floor. Clean room floors need to be cleaned regularly to remove any possible contaminants.
- Routine cleaning: This usually involves the use of a dedicated vacuum cleaner and cleaning agents, and regular mopping of the floor to keep the surface clean.
- Disinfection procedure: Disinfect regularly to ensure that the floor surface is free of bacteria and microorganisms and meets the hygiene standards of clean rooms.
Air flow and filtration
The working principle of clean room floor is also closely related to the air flow and filtration system of the clean room. The air flow design of the clean room adopts laminar flow technology to make the air flow evenly in the room, thereby effectively controlling the sedimentation of particulate matter.
- High-efficiency filtration system: Use high-efficiency air filters (such as HEPA or ULPA filters) to ensure that particles in the air are captured and the indoor environment is kept clean. This filtration system works together with the clean room floor to ensure the overall cleanliness level of the clean room .
Cross-contamination prevention and control
The design and material selection of the clean room floor also help prevent the occurrence of cross-contamination. In a clean room, different areas are usually set up to meet different process needs.
- Area division: By dividing areas, ensure the isolation between sterile operations and non-sterile operations and reduce the risk of cross-contamination.
- One-way flow design: Implement one-way air flow and personnel flow in the clean room to further reduce the risk of contamination and ensure the safety of the working environment.
Interested in it? don’t hesitate to contact us now.
Choose Your Interested Production Line
Bottle Filling Line
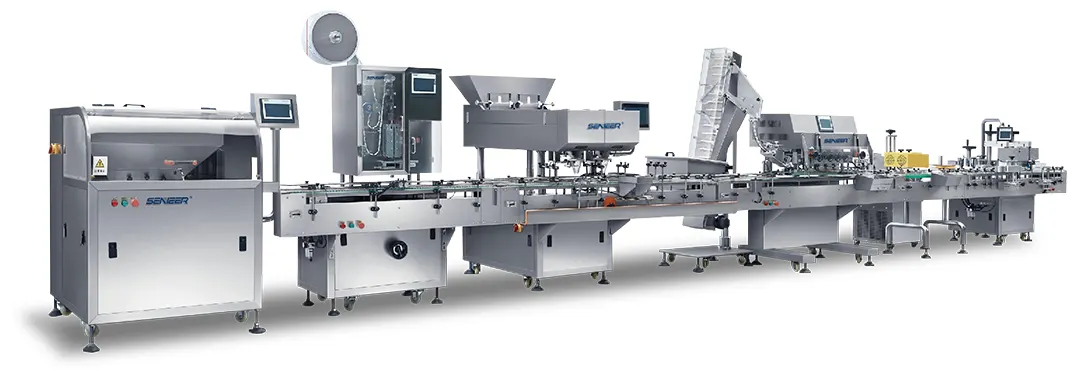
Granulation Line
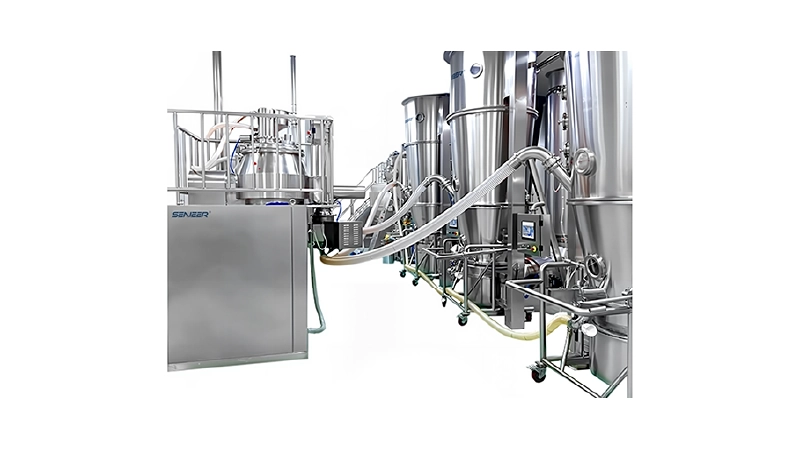
Blister Packaging Line
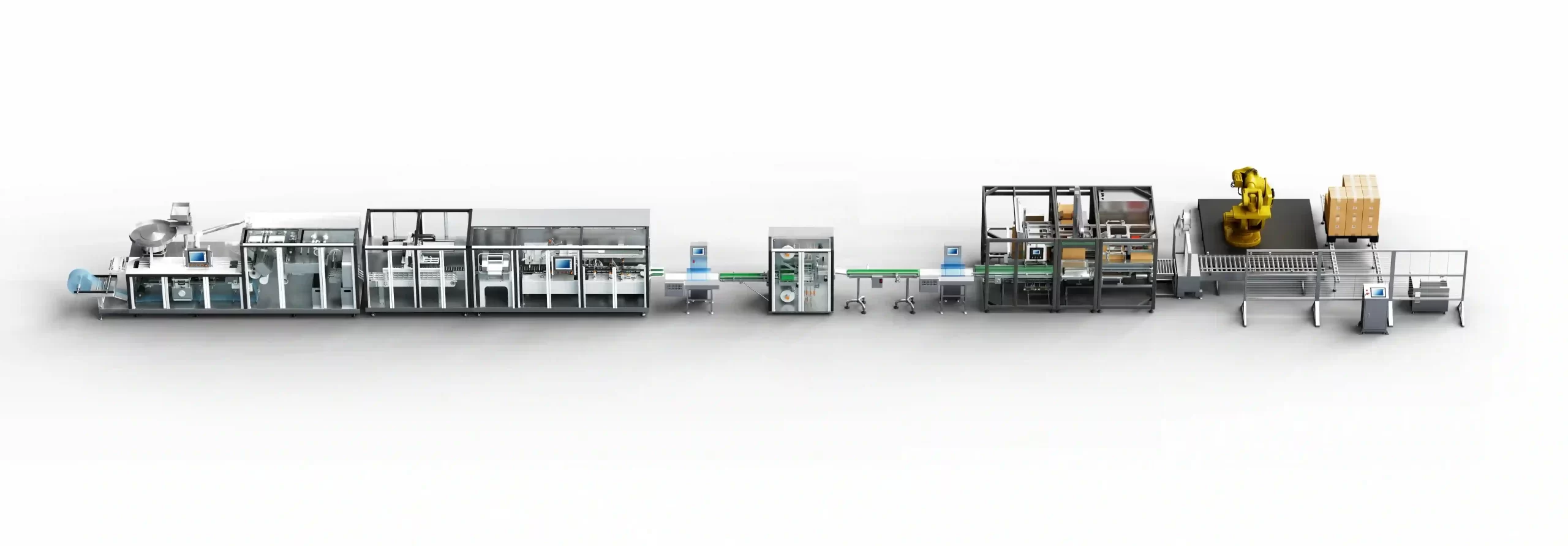
Powder Filling Line
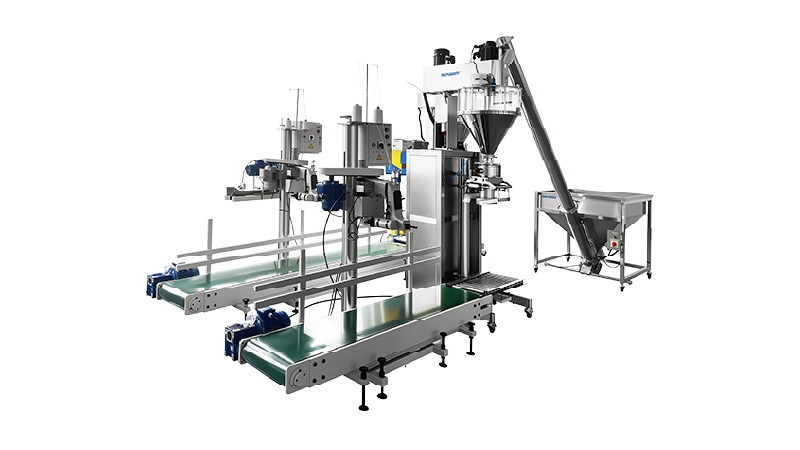