The granulation process refers to the adhesion of powders or fine particles to each other to produce large multi-particulate entities or particles. The dry granulation process usually refers to the granulation process that does not need to add liquid in the granulation process. During this process, the roller compactor process has a vital role in the granulation process.
In the dry granulation process, the dry granulation method is a method in which the powders of drugs and excipients are mixed uniformly, compressed into large flakes or plates, and then made into particles of the desired size through the step of pulverizing and granulating. The method relies on compressive force to generate binding force between molecules, and its preparation methods include a tableting method and a rolling method.
Tablet Method
The tableting process adopts the method of entering powder into a cavity with a fixed volume, compacting it into a tablet, and then breaking the tablet into particles of the desired size. However, because it is difficult for the material with poor fluidity to enter the cavity smoothly and the density of the material fluctuates, the weight of the tablet pressed each time varies greatly, and the density of the compacted tablet is uneven. Therefore, the properties of the particles formed by the final crushing are also difficult to control.
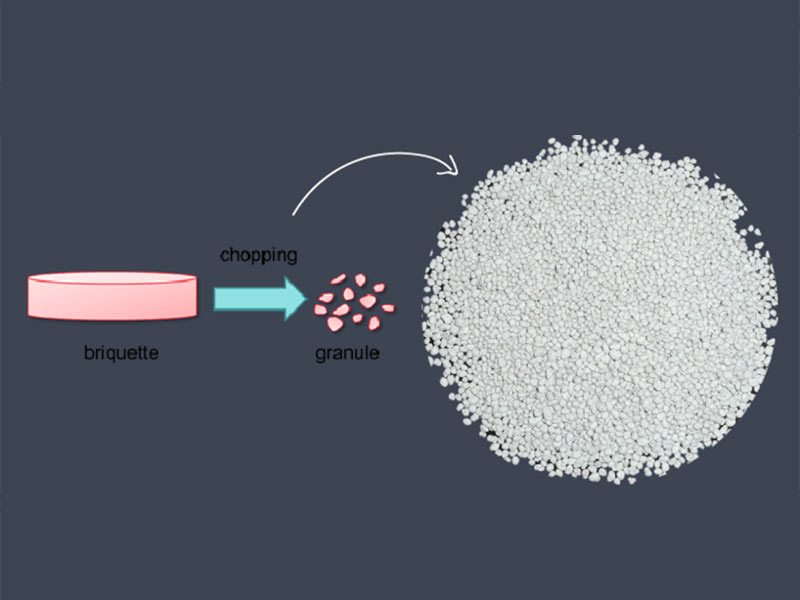
Rolling Method
The rolling method is the mainstream method of the dry granulation process. The Fitzpatrick dry granulator adopts the rolling method, and the equipment generally consists of three main components:
- Feeder: Conveys powder to the compaction area between the pinch rollers.
- Compactor: Force is applied between two counter-rotating pinch rollers to compact the powder into a strip or sheet of hard flakes.
- Pelletizing device: used to crush the hard flakes into the desired particle size.
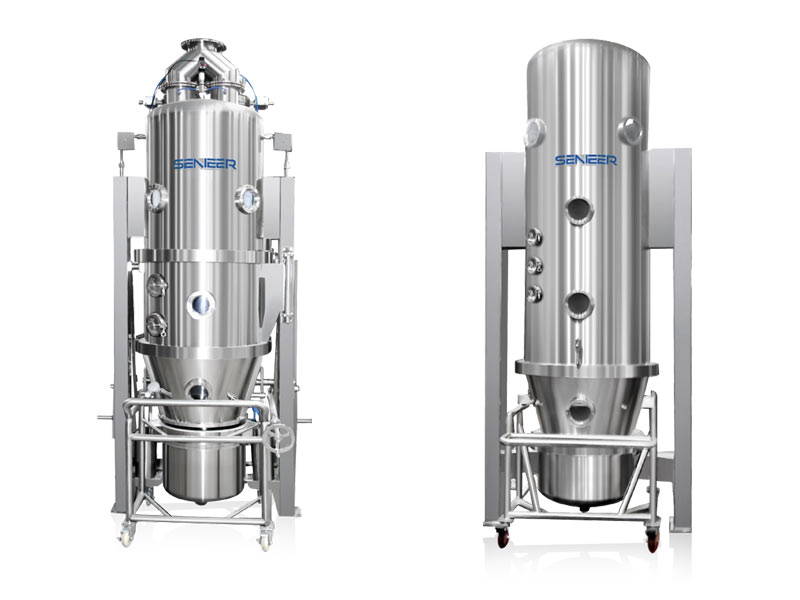
Granulation Quality Control
Dry granulator is capable of online control and measurement of all product quality related parameters (such as force, gap and roller speed) to meet the pharmaceutical industry requirements for process control and documentation of production processes, and all parameters are calibrated and verify.
Process Control
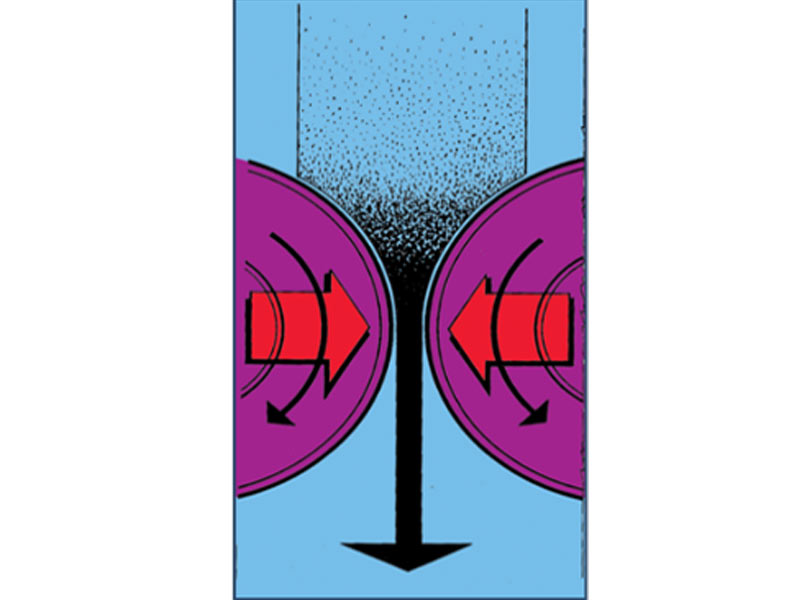
Pressure Control
During dry granulation, the powder passes between two pinch rollers and is compacted by the applied force between the pinch wheels, the pressure being the most important parameter. The applied force is expressed in kN/cm, that is, the force per centimeter of the width of the roller. On older equipment, pressure is also expressed in hydraulic units, BAR. However, this only represents the pressure within the hydraulic system and is not actually a unit of measure for the force applied to the powder.
At a set force, the powder will be compacted to a pre-set sheet thickness according to the amount of powder delivered to the pinch roller. Precise process control is the key to obtaining uniform particle properties.
Gap Control
The gap control of the dry granulator can be divided into two categories: one is the fixed gap of the pressing wheel, and the other is the floating gap of the pressing wheel. The two control methods differ in the way in which the minimum distance (gap) between the rolls is achieved.
When a fixed gap control is configured, since the amount of powder entering the compaction area between the pinch rollers fluctuates with density changes, the force applied to the powder also fluctuates. This will cause fluctuations in flake density and particle bond strength.
When equipped with floating gap control, the gap between the pinch rollers changes according to the amount of powder supplied, and the force applied to the powder remains unchanged. This ensures that fluctuations in tablet density and particle bond strength are minimized. This suffices through roller compactor process.
Grain Control
On dry granulation equipment, the process unit is an integrated design, and the compacted hard flakes are immediately transferred to the granulation unit, which can be equipped with screens of different apertures. With the accumulated experience of QUADRO and FITZMILL in the field of granulation, according to different material properties, FITZMILL can provide different types of rotors and screens to achieve the optimal particle size distribution effect.
Application Of Dry Granulation
Improve Material Flow
Dry granulation is suitable for increasing the bulk density of powders while increasing the particle size for better material flow, which is a prerequisite for the production of capsules and tablets on high-speed production equipment.
In addition, during the roller compaction processs, the particles with different characteristics are tightly bonded together, which effectively prevents the segregation of powder particles. This will improve the uniformity of the active ingredient (API) in the powder mixture, thereby increasing the dosage uniformity of such dosage forms.
The difference between wet granulation and dry granulation
Compared to wet granulation, dry granulation is a truly continuous production process. At present, the production capacity of dry granulation systems can reach about 400 kg/h.
Dry granulation systems require low capital or facility investment. In addition, maintenance requirements are relatively low, which greatly reduces life cycle costs.
Due to our continuous technological refinement and innovation, almost all dry powders can be processed using the dry granulation system.
The advantages of dry granulation are:
- Small production floor area
- Mass production (high-efficiency process)
- True continuous production process
- High energy efficiency, no need for special air conditioning and hot air drying systems
- High-enclosed equipment design can avoid contamination of production areas and personnel by high-strength active substances
- Low operating costs