Home » Extruder And Spheronizer
Extruder And Spheronizer
Efficient extrusion, precise granulation and spheronization- Senieer extruder and spheronizer makes your production process smoother,
ensuring that every granule reaches perfect standards, bringing you stable, reliable and high-quality output!
Introduction of Extruder and Spheronizer
An extruder and spheronizer system is a type of processing equipment designed to transform raw materials(wet/dry) into uniform, manageable pellets or granules. This setup is commonly used in industries like pharmaceuticals, plastics, food processing, and chemicals, where consistent shape, size, and quality of the output material are crucial. Through different diameters of holes in the granulating cylinder, different densities and diameters of granules and pellets can be produced, and the granulating cylinder is also changeable to get the specified diameter granules.
According to different production needs and process requirements, Senieer offers extruders and spheronizers of different sizes, usage and capacity, to satisfy client’s specific production and lab needs.
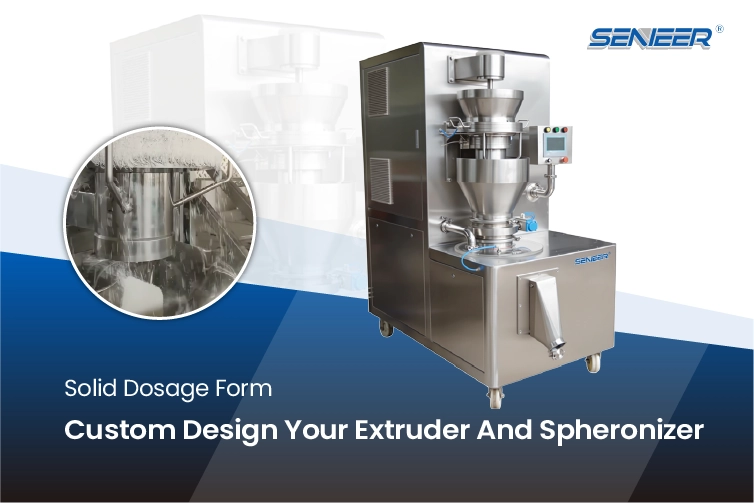
Different Types of Extruder and Spheronizer
Senieer offers wet/dry extruders and spheronizers suitable for wet or dry granulation applications. The dry extruder and spheronizer is specially suitable for the granulation of thermo-sensitive and moisture-sensitive materials, and is widely used in the processing of various active drugs. Senieer also offers extruder and spheronizer for wet granulation, which avoids the occurrence of dust during production process because materials are processed in a wet condition. Due to modular design, it is convenient to disassemble, wash and assemble accessories and parts such as granulating cylinder, pressure cylinder, etc.
Find Extruder And Spheronizer according to your industry or process
Extruders and spheronizers have been used in many industries due to their efficient and precise balling capabilities, providing solutions for the production of different products. Senieer offers screw, rotary, dry/ wet types of extruder and spheronizers, satisfying different production requirements and needs of clients. It is widely used in pharmaceuticals, food processing, rubber auxiliaries, plastic auxiliaries, catalysts, pesticides, dyes, pigments, daily chemicals and other industries that need granulation.
The process flow of the extruder and spheronizer is the key to achieving high-quality spherical particle production. It combines the extrusion, shaping and spheronization of materials to ensure that the product has the ideal shape and density. Different types of extruder and spheronizers have different processes. For example, screw extruder and spheronizer has two forms of extruding: pre-discharge and side discharge. In the rotary type extruder and spheronizer, the powder and solvent are made into a batch of irregular wet agglomerates containing water through the mixer process, which go through auxiliary bin, screw machine, vertical rotary extruder, timing valve bin, centrifugal spheronization machine in turn and finally pellets with the same particle size are made.
Guidelines For Extruder And Spheronizer
From the basic structure and working principle of the equipment to practical application areas and maintenance techniques, this guide covers all aspects of the extruder and spheronizer machine, helping you optimize your production process and improve pellet quality to achieve ideal processing results in the pharmaceutical, chemical, food and other industries.
Applications
Extruder and spheronizer are foundational in various industries due to their ability to handle diverse materials.
1.Pharmaceutical Industry: Used for shaping tablets and granules, extruders and spheronizers ensure uniform size and density, critical for accurate dosage and controlled-release medications.
2.Food Industry: Extruders shape food items like snacks and cereals, while spheronizers create manageable pellets for easy handling and distribution. In pet food production, for instance, these systems help create kibble with a specific texture and size.
3.Plastics Industry: Extruder and spheronizer convert raw polymers into pellets, which can then be molded or processed further. They are also used in recycling to repurpose plastic waste into usable granules, supporting sustainability efforts.
4.Agricultural Sector: Spheronizers are used to create animal feed pellets, ensuring that feed is of a uniform size for easier digestion and storage.
5.Chemical Industry: Chemical compounding relies on extrusion and spheronization to blend additives or fillers with base materials, creating customized compounds for industrial use.
Benefits of Extruder and Spheronizer Systems
Extruder and spheronizer systems offer a range of advantages that boost productivity and product quality:
1.Consistency: The extruder’s ability to apply consistent heat and pressure ensures a uniform material flow, while the spheronizer’s precision-cutting yields identical pellet sizes, vital for quality control.
2.Efficiency: By integrating extrusion and spheronization processes, manufacturers can streamline production, improving throughput and reducing labor costs.
3.Adaptability: Extruder and spheronizer models can be customized for specific materials and products, making them suitable for specialized applications in diverse industries.
4.Cost Savings: By creating a uniform, manageable product, these machines reduce waste and improve resource utilization, contributing to cost-effectiveness.
5.Sustainability: Particularly in plastic recycling, these systems are instrumental in transforming waste materials into reusable products, supporting circular economy .
How Do Extruders and Spheronizers Work?
The extruder and spheronizer work in tandem, transforming raw materials into consistent, uniform pellets. Here’s a step-by-step overview of how each component operates and integrates with the other:
1. Feeding and Pre-Processing in the Extruder
Material Feeding: Raw material (powder, pellets, or granules) is introduced into the extruder via a hopper. Gravity or vacuum feeders may be used to ensure an even flow.
Screw Mechanism: A rotating screw, or screws, moves the material through a heated barrel, where it gradually heats up and begins to melt. The design and type of screw (s) affect mixing and material flow.
Heating: The barrel of the extruder is divided into multiple heating zones. Each zone has a specific temperature to ensure controlled heating, melting, and softening of the material.
Pressure Building and Shaping: As the material moves forward, it is compressed and pushed through a die at the extruder’s end, forming it into the desired shape, usually a strand.
2. Pelletizing Process
Transfer to Spheronizer: The extruded material exits the extruder as a continuous strand, which is then directed to the spheronizer.
Cutting Mechanism: In the spheronizer, rotating blades cut the extruded material into small, uniform pellets. The cutting can occur in air or water depending on the process differences of extruding.
Cooling and Solidification: Cooling is often applied immediately after cutting to solidify the pellets, maintaining their shape and preventing them from sticking together. Air, water, or cooling belts can assist in this process. Usually, hot-melt extrusion cooling ways include air, water or underwater cooling, which is suitable for thermo-sensitive or density-sensitive materials while wet extrusion cooling(air, fluidized bed or centrifugal drying) is suitable for materials need solvent or binder.
3. Final Output
After cooling, pellets are screened for size uniformity, dried if necessary, and collected, ready for packaging or further processing.
Combination Equipment
When combined with auxiliary systems and specialized equipment, extruder and spheronizer can maximize productivity, quality, and efficiency. Here are some essential combination equipment often used alongside extruder and spheronizer:
1. Feeders
Gravimetric Feeders: Provide a consistent, precise feed rate to the extruder by measuring and controlling the material’s weight as it enters the system, essential for maintaining consistency in sensitive formulations.
Volumetric Feeders: Use a controlled volume to feed material into the extruder, typically for applications where a precise feed rate isn’t critical but flow consistency is required.
2. Melt Pumps
Positioned between the extruder and spheronizer, melt pumps stabilize and control material flow and pressure, reducing fluctuations caused by screw speed variations. They’re especially beneficial in processes requiring highly consistent output.
3. Cooling Systems
Air Coolers: Suitable for lower-temperature applications, air coolers solidify pellets quickly after cutting.
Water Cooling Systems: Commonly used for underwater spheronizers, water cooling systems rapidly solidify hot pellets as they exit the cutting chamber, preventing deformation.
4. Screen Changers
These filtration systems remove contaminants from the molten material before it reaches the die or spheronizer. Continuous screen changers allow for uninterrupted operation, making them ideal for high-volume production lines.
5. Automatic Strand Conveyors
Strand conveyors handle and transport extrudate strands from the extruder to the spheronizer, reducing manual handling and ensuring smooth, uninterrupted flow.
6. Drying Equipment
After cooling, especially with underwater systems, drying equipment removes residual moisture to prevent clumping. Vibratory fluid bed dryers or centrifugal dryers are commonly used for this purpose.
7. Quality Control Systems
Quality control systems with sensors and automated analyzers check pellet size, shape, and density, immediately identifying any deviations. This ensures consistent output quality.
8. Storage and Handling Solutions
Hoppers and Silos: For bulk storage and efficient material handling, hoppers and silos provide a seamless transition from the extruder-spheronizer line to packaging or secondary processing.
9. Control Systems and Automation
Modern extrusion and spheronization lines often integrate with centralized control systems that manage temperature, feed rate, pressure, and cutter speed. Automation enhances precision and reduces the need for manual intervention, boosting productivity.
Want to learn more of our products? Contact to us now.
Choose Your Interested Production Line
Bottle Filling Line
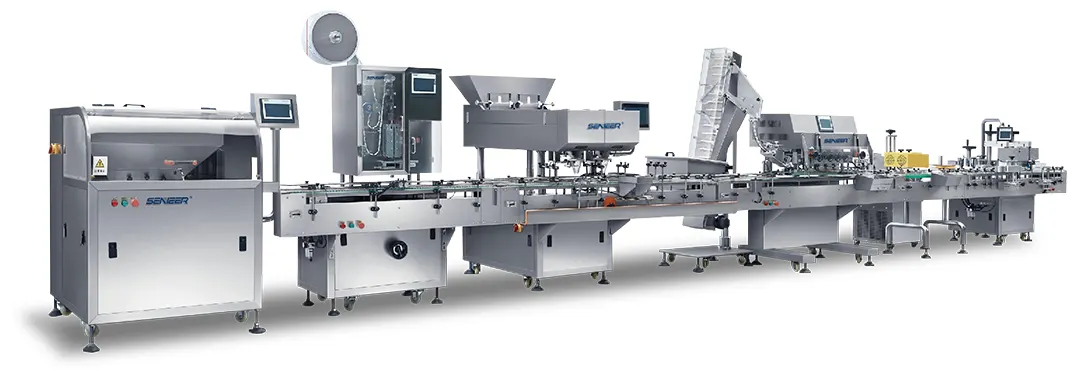
Granulation Line
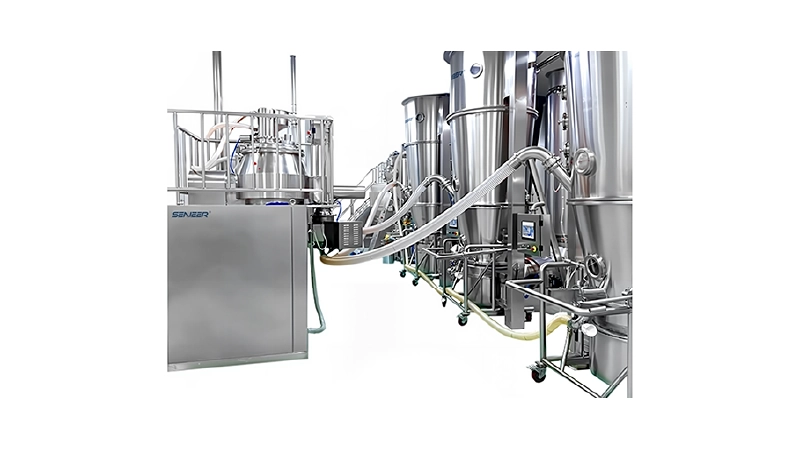
Blister Packaging Line
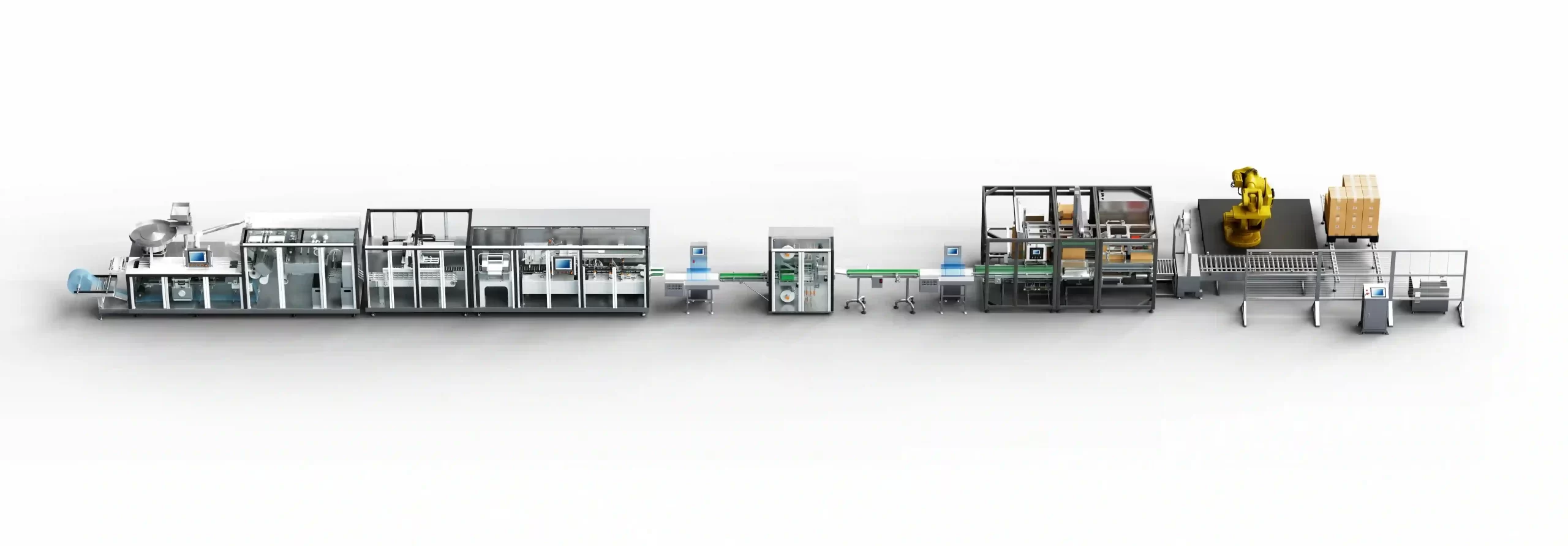
Powder Filling Line
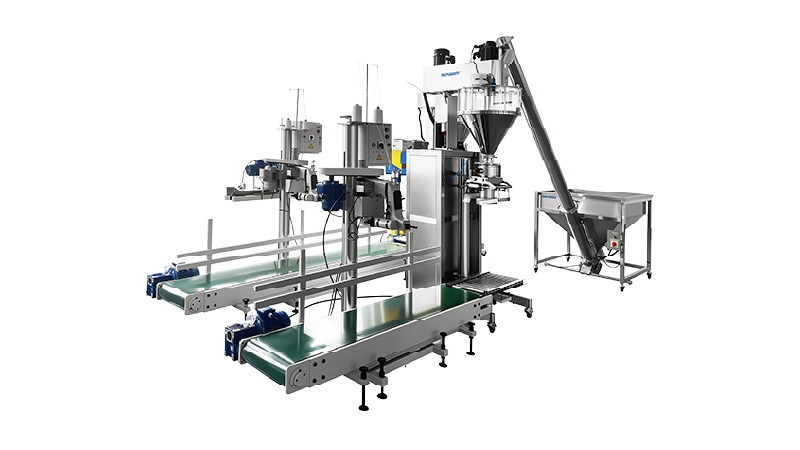