What is a high shear Mixer?
The high shear mixer is a pharmaceutical machine which is used to produce granular, emulsion, and suspension products. It can also be used to emulsify, homogenize, and decrease particle size, it is frequently used in the food, pharmaceutical, and cosmetic industries.
The use of a high shear mixer allows for the emulsification, homogenization, dispersion, grinding, and/or dissolution of immiscible mixtures that contain components from the same or separate phases. High rotor tip speeds, high shear rates, localized energy dissipation rates, and increased power consumption are all features of these devices compared to standard mixers.
A homogenizer is a high-shear mixer used to combine different-density liquids, solids, and powders into a homogeneous mixture.
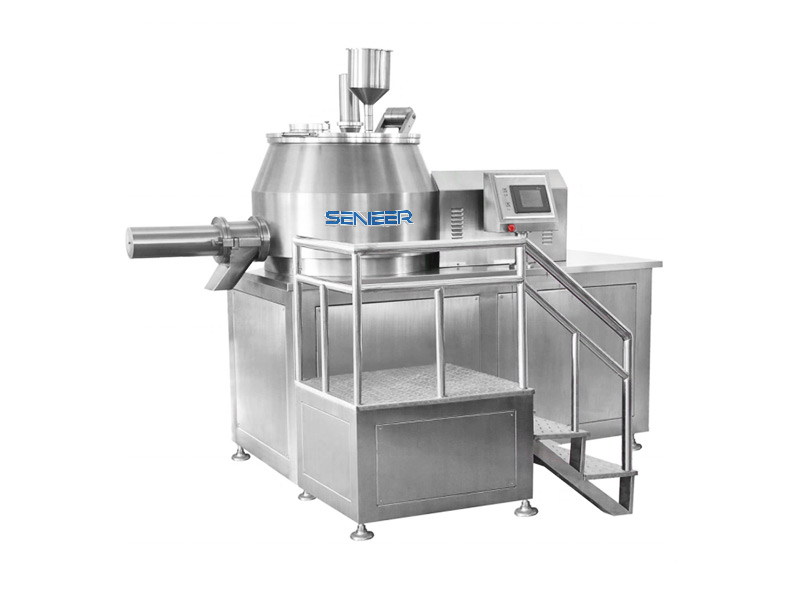
Importance of High Shear Mixer in Pharmaceutical Manufacturing:
High shear mixers have different advantages such as:
- Less binder solution is used during the granulation process, an advantage of high-shear granulators.
- Granulation is accomplished quickly.
- More densification and the creation of granules that are less brittle.
- The granulator creates uniformly sized, repeatable grains that are less friable.
- Because less process dust is produced by high-shear granulators, workers are exposed to less medication dust.
- A high-shear mixer produces reliable granulation endpoints.
- Needs quick drying times.
Disadvantages of a High Shear Mixer:
- When compared to low-shear granulators, high-shear granulators create granules that are less compressible.
- The conditions in which it can operate are limited.
- The creation of big lumps may result from overwetting the granules.
- Materials that are thermolabile may undergo chemical degradation as a result of temperature rise.
- When it comes to fragile particles, mechanical degradation is a possibility.
High-shear mixers provide a variety of advantages over other types of mixers and granulators, whether they are used for dry powder mixing, granulation, melt coating, etc. Most crucially, this includes the ability to process particle kinds that are challenging to process with other machinery. High-shear mixers may also disperse highly viscous binders and create tiny grains with a diameter of less than 2 mm. Agglomerates made from these granules often have a denser and more compact structure than, say, agglomerates made in fluid beds. The pharmaceutical, agrochemical, and detergent industries all frequently use high-shear mixers.
Applications for High Shear Mixers:
All sectors that need to blend components use high shear mixers. Here are some uses for high shear mixers.
Food industry
This category includes a wide variety of high shear mixer applications. In the food sector, high shear mixers are used to make emulsions, suspensions, powders, and granules. The production of pastes, dressings, and sauces is a common use. The majority of the elements are made up of immiscible liquids like water and oil as well as solid particles.
Some ingredients, such ketchups, mayonnaise, and doughs, are more challenging to process. Due to their viscoelastic qualities, these liquids and semi-solids require little force to flow. Specialized rotor-stator mixing heads are needed for this.
Pharmaceutical industry
The pharmaceutical industry works with a variety of combinations. Because they have a closed system that prevents pollutants from getting in, inline high shear mixers are used. All pharmaceutical goods, which can range in viscosity and particle size and include tablets, syrups, suspensions, injectable solutions, ointments, gels, and creams, are put through a high shear mixer.
Wet granulation
Using a suitable non-toxic granulating fluid, such as water, or ethanol, small powder particles are agglomerated or brought together into larger, stronger, and more durable structures called granules in the wet granulation method . A solvent-containing binder or granulating agent may be employed in addition to or instead of the granulating fluid. The qualities of the materials to be granulated play a major role in the choice of the granulating fluid.
Conclusion
- When mixing is in equilibrium, further effort from the mixer has no significant influence on the product’s characteristics.
- High shear mixers come in four different varieties: batch, in-line, powder injection, and granulators. The two primary types are batch and in-line high shear mixers, while the other two are variations. Large volumes can be processed quickly using batch high shear mixers. On the other hand, in-line mixers may be effectively controlled and are less prone to contamination.
- When two impermeable liquids, such as oil and water, are combined, an emulsion is produced. Oils can float on the surface because they are lighter than water and hydrophobic, which makes them hydrophobic. The distributed droplets in this mixture must be divided into smaller ones to avoid their natural separation in order to homogenize it.
- These devices work by shearing a mixture made up of a continuous phase and a scattered phase. Smaller scattered particles or droplets that are simpler to dissolve and merge during the shearing process result in a homogenized, continuous phase.
- The rotor and the stator are the two essential components of a high shear mixer. The mixing head or generator is the name of this component. The shearing of the mixture occurs in the shear gap, which is the space between the rotor and the stator.
- When compared to an emulsion, where the dispersed particles are solid, a suspension is different. The high shear mixer also serves the purpose of dispersing the solids into smaller particles.
- High shear mixers can also be used for granulation and particle size reduction. High shear mixers can aid in combining constituents into more substantial and dense agglomerates. Once the desired size is obtained, these agglomerates are next divided into smaller, more precise particles.
- A vacuum system sucks the powdered components straight into the mixing head in powder injection high shear mixers, which are a variation of the previous two and allow for better mixing.
- In order to create big agglomerates, high shear granulators combine finely ground goods while utilizing a binder liquid. The desired particle size granules are subsequently created by dissolving these agglomerates.
- When processing a mixture that is too challenging, expensive, or time-consuming for regular mixers, high shear mixers are used to emulsify, homogenize, disperse, grind, and/or dissolve components of the mixture.
Why choosing senieer?
Equipment like the Rapid Mixer Granulator (RMG) or High Shear Mixer Granulator is particularly helpful for both industrial and laboratory applications. Nevertheless, China likely has hundreds of high shear mixer suppliers and manufacturers. You can now clearly see that no one can match the excellence of Senieer’s Rapid Mixer Granulator (RMG) or High Shear Mixer Granulator goods and services.
Get a free, quick quote from us right away if you’re looking for a high shear mixer for sale in China that will be delivered right to your door.
Additionally, if you need any assistance with ordering high shear and having it delivered to your home, please get in touch with Senieer right away, we will respond immediately. We are here for you.
For more information check our website: www.senieer.com