Fluid Bed Granulator
Senieer Fluid Bed Processors offer efficient drying, granulating, and coating solutions for pharmaceutical, food, and chemical industries. Utilizing fluidized bed technology, they ensure high-quality product development, minimal material waste, and GMP-compliant, consistent performance across various processes.
Introduction Of Fluid Bed Granulator
Fluid Bed Granulator is a cutting-edge granulation machine designed to achieve consistent and high-quality granules. The machine uses fluidized bed technology to mix powders, binders, and liquids in a controlled environment, ensuring the granulation process is efficient, reproducible, and scalable. Fluidized bed granulation is an essential process in pharmaceutical manufacturing to create uniform, dense granules for tableting or capsule filling.
Senieer Fluid Bed Granulators are equipped with advanced features to provide precise control over the granulation process, resulting in improved product quality, reduced material loss, and shorter processing times. These machines are GMP-compliant, making them suitable for use in regulated environments like pharmaceuticals and food manufacturing.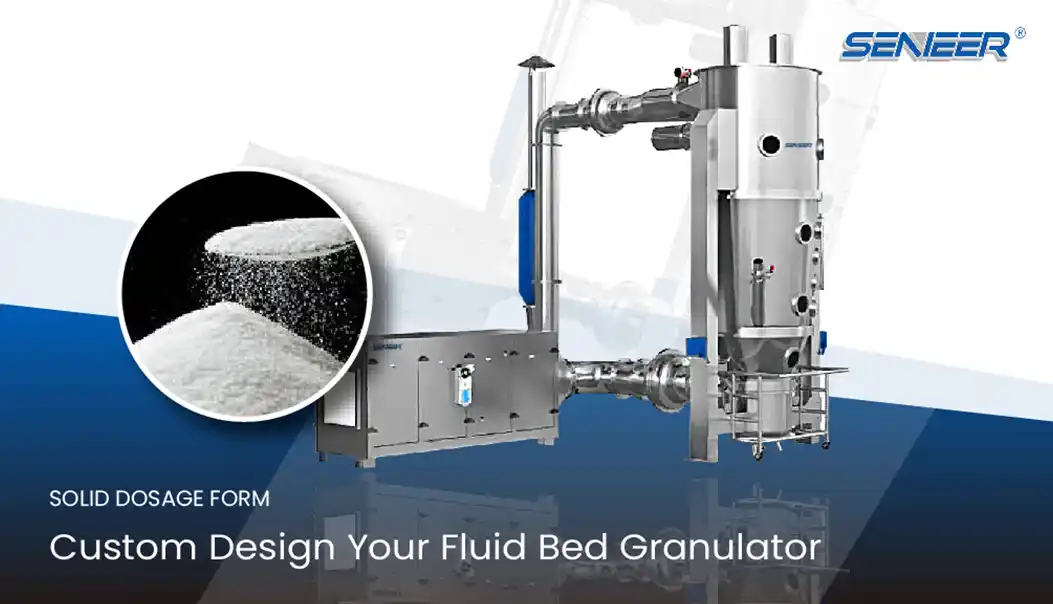
Different Types Of Fluid Bed Granulators
Senieer offers various models of Fluid Bed Granulators to suit different production scales and granulation needs.
Choose Your Fluid Bed Granulator
Senieer offers fluid bed granulators suitable for various industries, including pharmaceuticals, food processing, and chemicals. Senieer machines provide efficient and uniform granulation for powders, improving both product quality and production efficiency.
Fluid Bed Granulator works by using a fluidized bed technique to granulate powders:
Loading: Powders are loaded into the granulation chamber, and air is circulated to create fluidization.
Granulation: A binder solution is sprayed onto the fluidized powder to form granules. The spray rate, binder concentration, and temperature are all carefully controlled to ensure uniform granule formation.
Drying: The granules are dried in the same chamber using heated air to remove excess moisture.
Discharge: Once the granulation and drying processes are complete, the granules are discharged and ready for further processing.
Guidelines For Fluid Bed Granulator
To ensure the best performance of your fluid bed granulator, should consider:
Regularly clean the granulation chamber to avoid cross-contamination.
Ensure that the spray nozzle is properly maintained to avoid clogging and uneven granulation.
Perform routine checks on airflow and temperature settings to ensure optimal conditions.
Always follow recommended safety protocols to prevent hazards during operation.
Features and Advantages Of Fluid Bed Granulator
Senieer Fluid Bed Granulators are equipped with advanced features to meet the needs of a wide variety of industries:
Uniform Granulation: The fluidized bed technique ensures homogeneous granulation with minimal material segregation.
Efficient Processing: Reduced processing time and higher yield through precise control of granulation parameters.
Versatile Applications: Ideal for pharmaceutical, food, chemical, and nutraceutical industries for granulating powders, granules, and fine chemicals.
GMP-Compliant Design: Built with GMP-compliant SS316L stainless steel for all product-contact parts, ensuring high hygiene and safety standards.
Automated Control System: Programmable controls for temperature, airflow, spray rate, and drying time to ensure repeatable granulation results.
Minimal Material Waste: Efficient discharge and drying systems ensure maximum yield with minimal material loss.
Specific Applications
Fluid Bed Granulator is widely used in the pharmaceutical, food, nutraceutical, and many other industries.
- Pharmaceutical Industry: Ideal for granulating active pharmaceutical ingredients (APIs) and excipients to improve solubility, bioavailability, and compression characteristics in tablet formulations.
- Nutraceuticals: Perfect for granulating dietary supplements and vitamins, ensuring uniformity in particle size and enhanced product performance.
- Food Industry: Suitable for granulating food ingredients like spices, flavorings, and sweeteners, improving consistency and ensuring optimal powder flow properties.
Key Components Of Fluid Bed Granulator
Fluid Bed Granulator is composed of several key components to optimize granulation:
Granulation Chamber: Where powders are fluidized and granulated using binder solutions.
Spray System: A precision spray nozzle used to evenly distribute binder solutions over the fluidized powder.
Air Distribution Plate: Ensures even airflow to maintain consistent fluidization throughout the chamber.
Control System: Allows users to adjust granulation parameters such as spray rate, temperature, airflow, and drying time.
Safety Features: Equipped with temperature sensors, pressure monitoring, and safety interlocks to prevent overheating and ensure safe operation.
Discharge System: Ensures complete discharge of the granulated material, preventing product loss.
Innovations and Customization
Senieer is committed to continuous innovation in fluid bed granulation technology. It offers several customizations, such as:
Advanced Spray Nozzle Systems: Designed for uniform binder dispersion and controlled granule size.
Integrated Drying System: For reduced drying time and minimal material degradation.
Customization for Product Requirements: Tailored designs based on material characteristics and production scale.
Easy Maintenance: Clean-in-place (CIP) and quick-release mechanisms make the granulator easy to maintain and clean, ensuring compliance with GMP standards.
Technical Support and After-sales
Selection Advice
When selecting the right fluid bed granulator, should consider:
Production Scale: Choose from batch or continuous models based on your production volume and granulation process needs.
Material Type: Make sure the granulator is compatible with your specific material, whether it’s fine powders, granules, or APIs, as different materials may require different processing conditions.
Customizations: Evaluate the need for features like adjustable airflow, temperature control, and binder spraying systems to optimize granulation results and meet your production requirements.
Why Choose Senieer?
Senieer is a trusted name in the pharmaceutical, food, and chemical industries, providing high-quality granulation equipment for over a decade. Here’s why you should choose Senieer Fluid Bed Granulators for your production needs:
Reliability: Built for long-term performance, ensuring that your granulation process runs smoothly and efficiently.
Customization: Senieer offers tailored solutions for your specific granulation requirements, whether for small-scale R&D or large-scale production.
GMP Compliance: All of Senieer’s equipment is manufactured to meet stringent global hygiene and safety standards.
Global Expertise: Senieer’s Fluid Bed Granulators are used worldwide by leading pharmaceutical, food, and chemical manufacturers.
Customer Support: Senieer provides expert advice, installation, and after-sales support to ensure your equipment continues to perform at its best.
Choose Your Interested Production Line
Bottle Filling Line
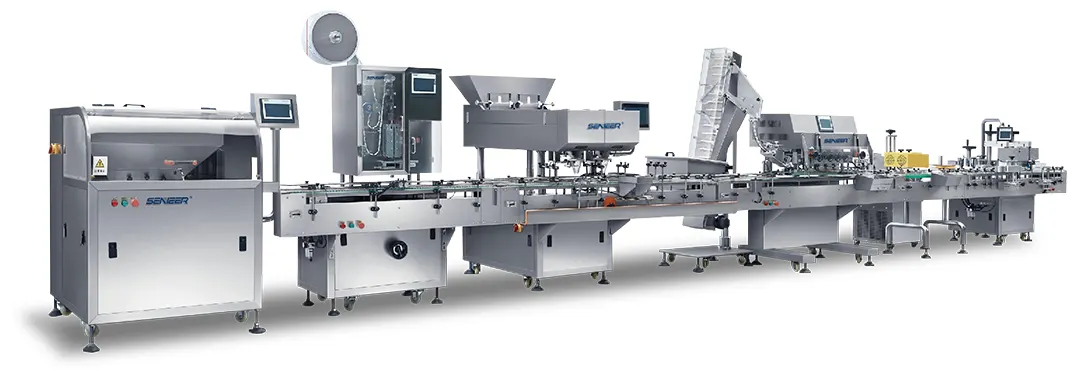
Granulation Line
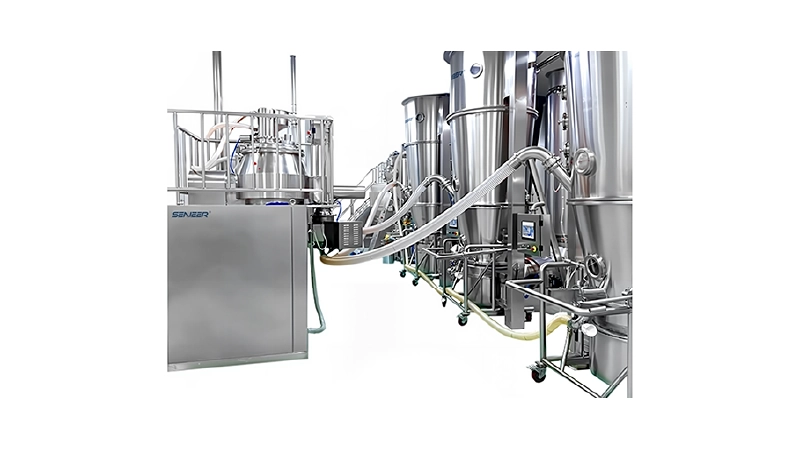
Blister Packaging Line
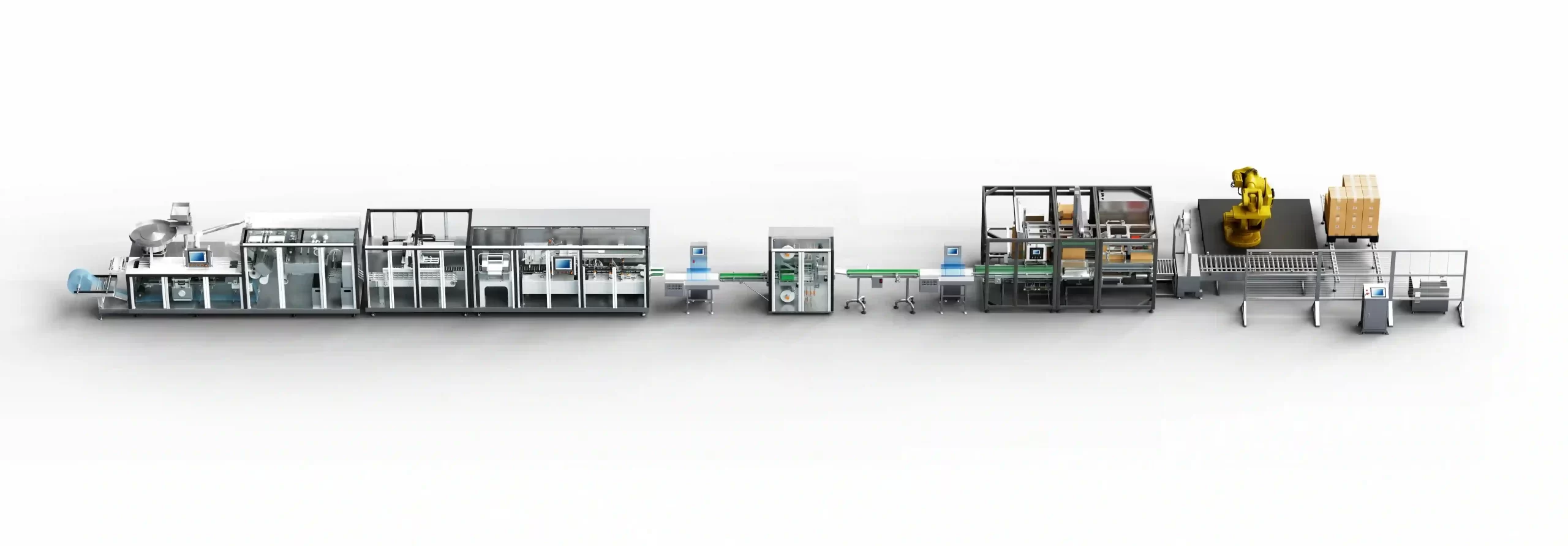
Powder Filling Line
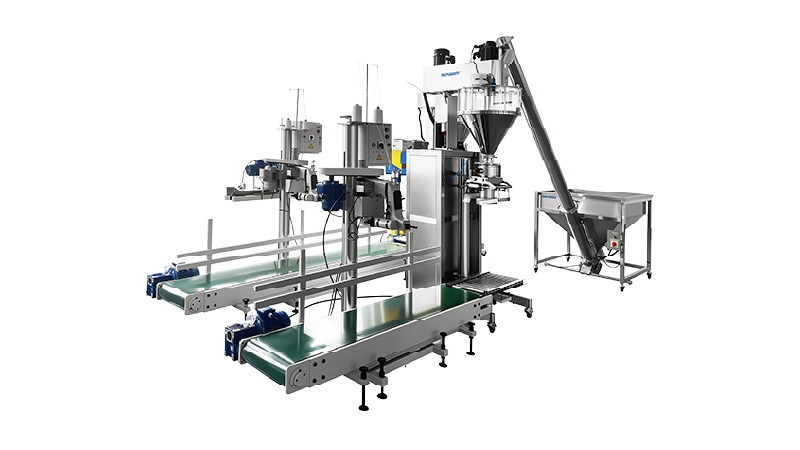