High Shear Mixer
- Fully automated high shear mixer system
- Vacuum conveyor charging material is available
- Wet cone mill is option item, screen mesh size 3*3,4*4,5*5,6*6,8*8
- Uniform cell suspension with high viscosity compounds
- Custom designs available upon request
- Meets the regulatory standards such as GMP
- Compact design makes high shear mixer easily integrate to any production line
High Shear Mixer : Product Description
The high shear mixer is a high-performance instrument for homogenization, particle size reduction, and mixing. With high throughput capacity, it can also be used as a high-speed blender. It meets the regulatory standards such as FDA and GMP.
The high shear mixer is a fully automated equipment hence minimal human involvement. The high shear mixer can process high viscosity compounds efficiently and quickly with uniform cell suspensions.
The mixer is made of quality material with high rust resistance to ensure durability and high mixing performance. The high shear mixer is designed to meet the customer’s requirement at a low cost.
The high shear mixer has a compact design that makes high shear mixer easily integrate into any production line. It also connect with vacuum conveyor, fluid bed dryer, etc.
Custom high shear mixers are available upon request.
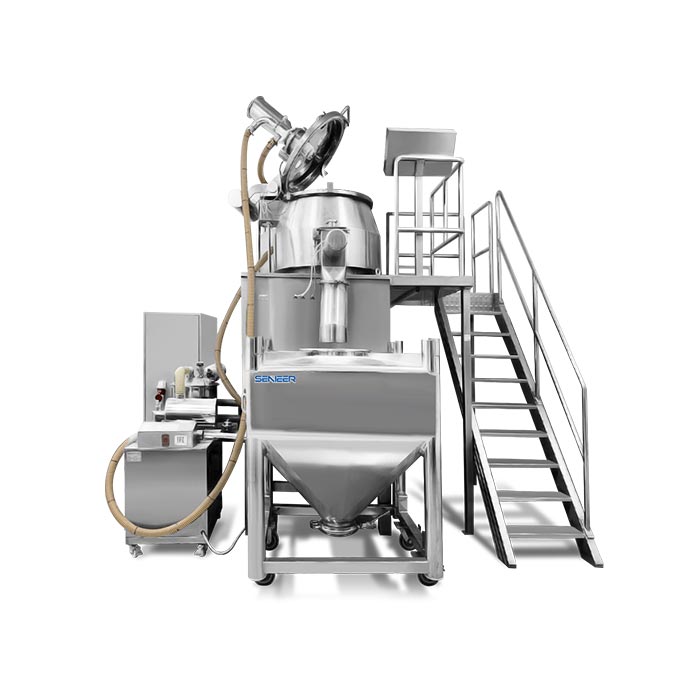
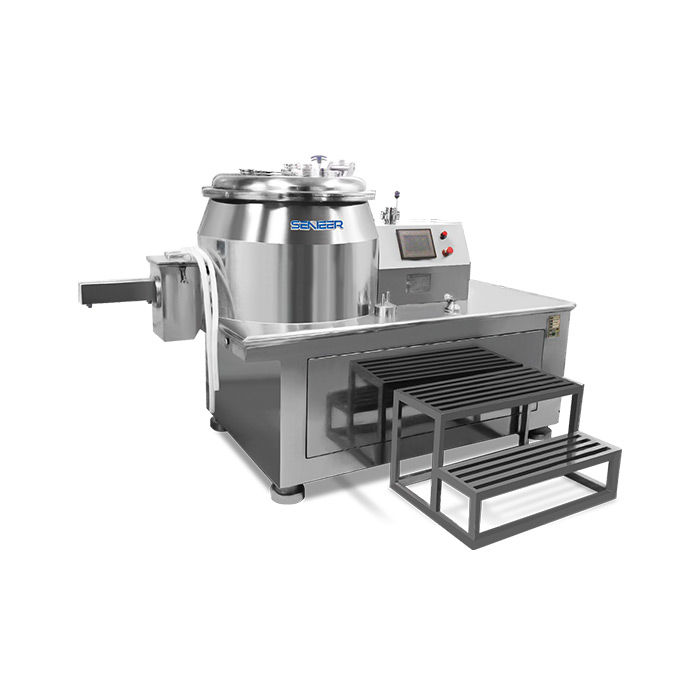
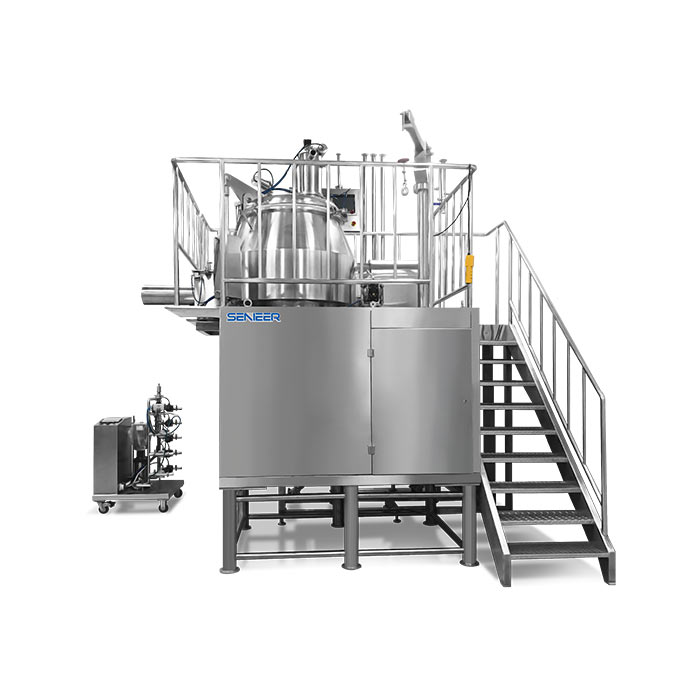
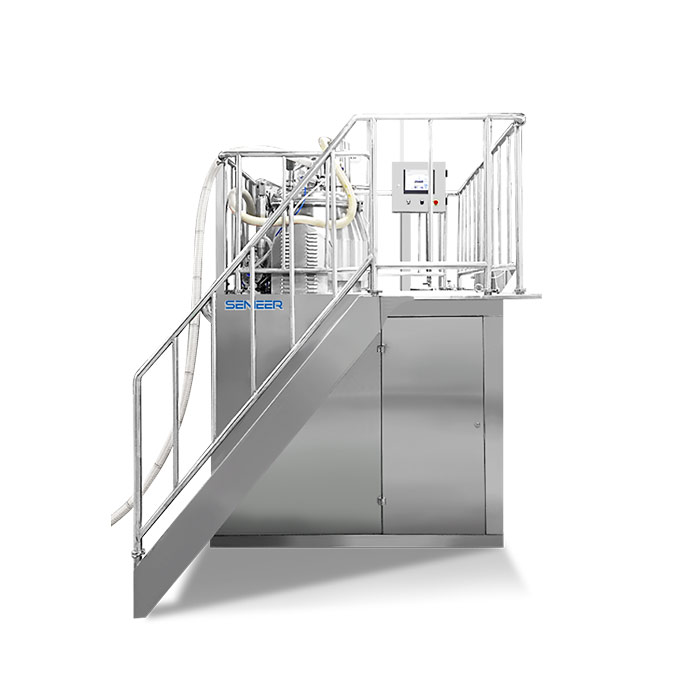
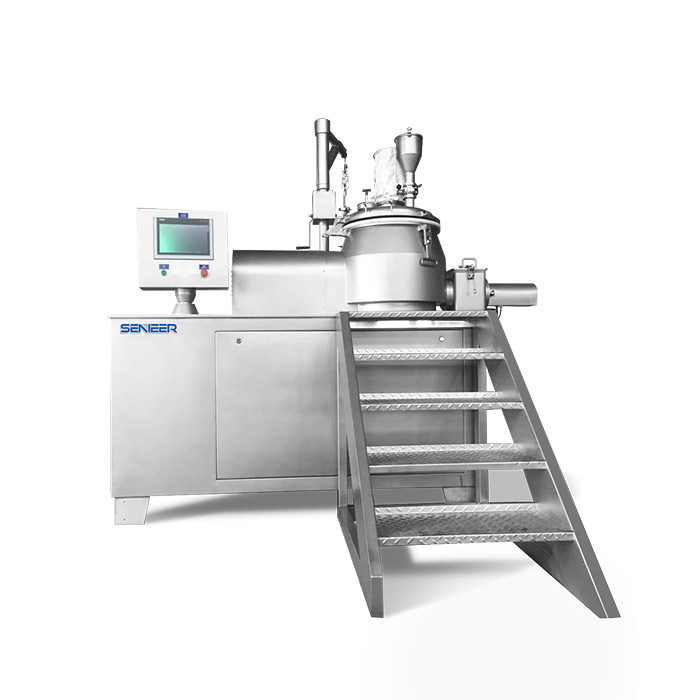
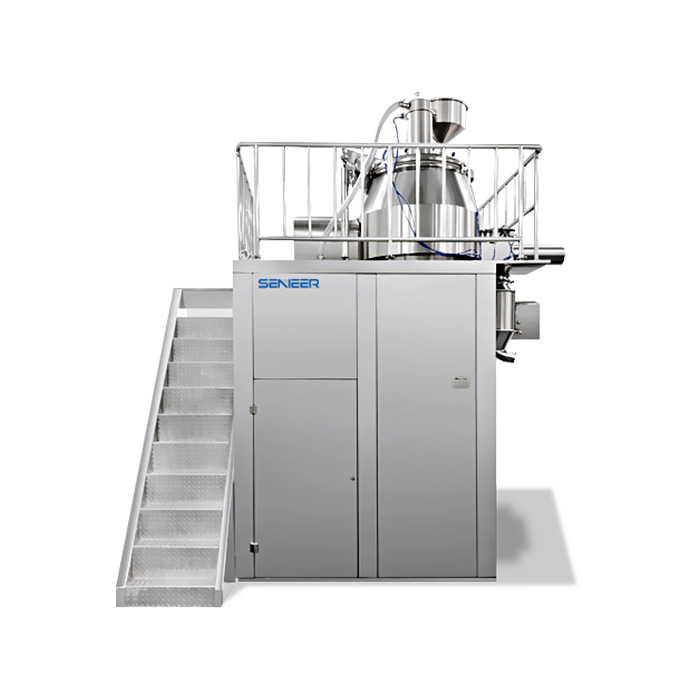
Paramenter of High Shear Mixer
◈ Compact design: The high shear mixer features a compact design. This feature makes high shear mixers easily integrate into any production line.
◈ High throughput: The high shear mixer has high throughput capacity, which enables high-speed blending or small batches of high-shear mixing. In addition, the high shear mixer is useful for high viscosity compound processing.
◈ Automatic operation: The high shear mixer is completely automatic. It allows a high shear mixer to be used as a high-speed blender.
◈ Easy to use: The high shear mixer has a simple operation and design, which keeps high shear mixer from any trouble during the high-speed high shear mixing process.
◈ PLC control features: The high shear mixer has PLC control features. The high shear mixer is the most high-tech high shear mixer available in the market.
◈ Solid construction: The high shear mixer is made of high-quality material, which gives high shear mixer high rust resistance. Consequently, it can be used under various conditions with high shear mixer without any trouble.
◈ GMP/FDA approved: The high shear mixer meets high shear mixer regulatory standards such as GMP and FDA.
◈ Advance technology: The high shear mixer has advanced technology, which makes it high-speed high shear mixer and high viscosity material processing machine. For example, high throughput high shear mixer and easy operation can be achieved with PLC high shear mixer control features.
◈ Pharmaceuticals
◈ Health product
◈ Chemical processing
◈ Food processing
◈ Agricultural products processing
◈ Uniform mixing
◈ Easy to use
◈ Simple and compact designed
◈ Strong and durable
◈ Can be customized to your requirements
More Details of High Shear Mixer
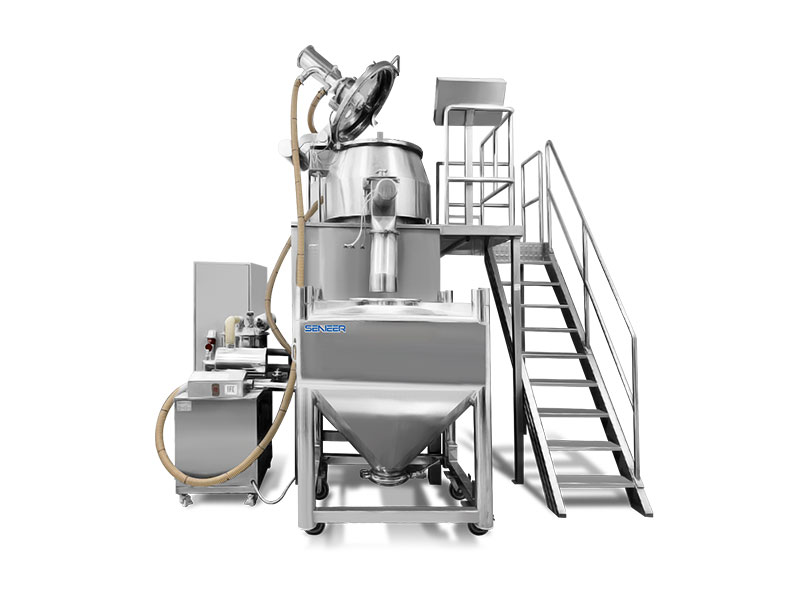
GL100 high shear mixer
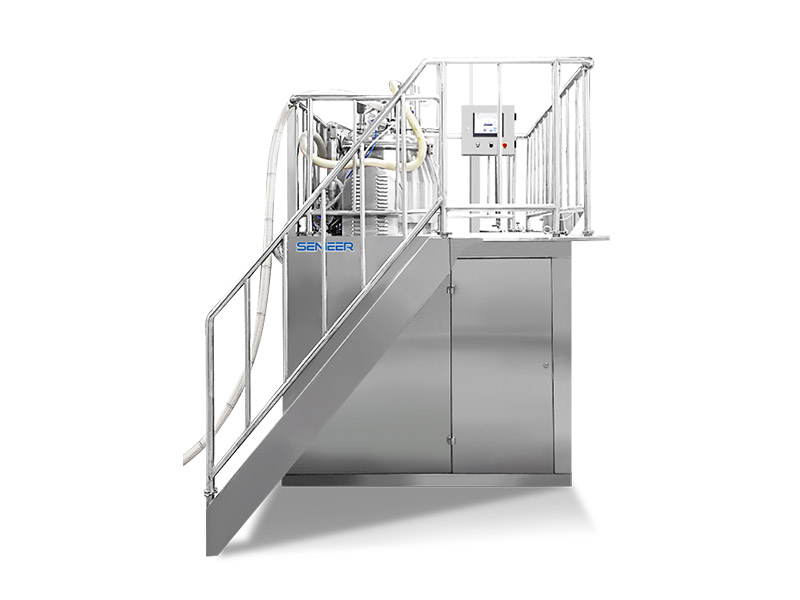
GM200 High Shear Mixer
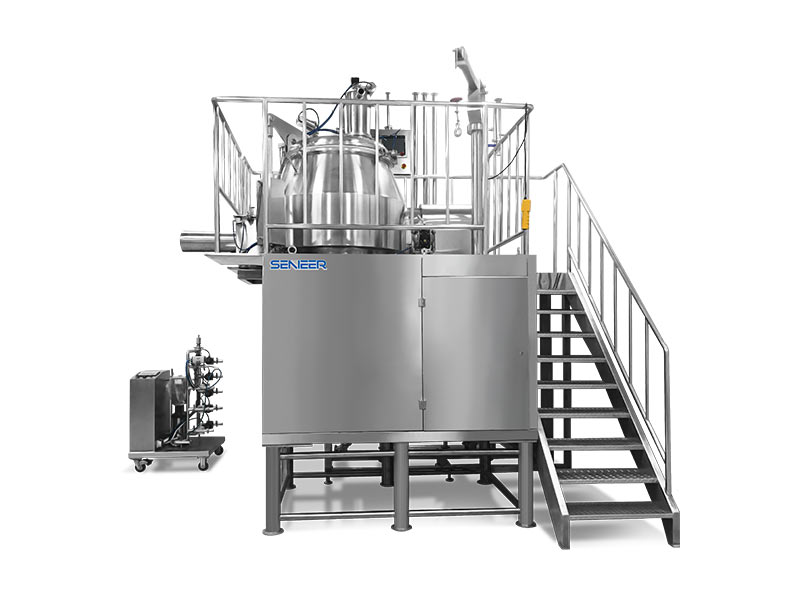
GM300 High Shear Mixer
Any Question About Senieer High Shear Mixer
Why Global Company Trust Senieer
Top Quality Factory Price
We have a quality control department to verify each product at different phases, from the procurement of parts to finished products
As Your Layout, Customize Machine
According to your layout, we can suggest the best capacity and type for you, customize high shear mixer for you
High Shear Mixer Consult & Design Service
Save energy resource for you, professional engineers can improve the best processing solution. We have the experience to help add a tremendous amount of value to your project
ISO.CE Standard Qualified
We successfully obtaining the ISO9001:2008 certificate and CE security management system certificate, this is significant for Senieer in building enterprise image
High Shear Mixer Training & Maintance Service
Free high shear mixer training & maintenance service for you, we will provide your team in-depth training on safe operation and high shear mixer maintenance
High Shear Mixer Installation Service
Senieer offers high shear mixer installation & commissioning service for production products, your high shear mixer and control systems are qualified based on the GAMP life-cycle
High Shear Mixer Granulator Complete Guide for Importers
Let’s dive right in:
- Chapter 1: Basics of the High Shear Mixer
- Chapter 2: Parts/ Components of High Shear Mixer Granulator
- Chapter 3: Working Principle of a High Shear Mixer Granulator
- Chapter 4: Technical Specifications of the High Shear Mixer Granulators
- Chapter 5: Factors Affecting the Granulation Process
- Chapter 6: How to Choose High Shear Mixer Granulator
High shear mixers are commonly used in the pharmaceutical and chemical industries for the production of ointments, creams, and other products that are characterized by heavy liquid material. The machine is designed to provide flow and shear on the fluid before it is dispersed into separate phases.
Are you in the market looking for high-shear mixer granulators? Take your time to know the details and specifications of this machine before you buy. Know how it works and the maintenance practices that are associated with the high shear mixer granulators.
In addition to the features and functionality, it is essential to buy from the best high shear mixer granulator manufacturers in China.
This is precisely the purpose of this guide. We are going to open your eyes to everything that you should know about high-shear mixer granulators. At the end of it, you will be in a perfect position to buy the best high shear mixer granulator for your relevant application area.
Chapter 1: Basics of the High Shear Mixer
1.1. What is a High Shear Mixer?
A high shear mixer granulator is an all-in-one piece of equipment that performs various functions, including shearing, mixing, granulation, emulsifying, grinding, dissolving, and dispersing materials in different production phases.
High shear mixer granulators are also known as high shear reactors or simply rotor-stator mixers since they have rotors that speed up the rate of shearing and dispersion of the materials. This is a crucial feature that makes high shear mixer granulators different from ordinary mixers.
The shearing and granulating actions are due to the motions generated by the rotors. The constant movements of other key components of the high shear mixers also account for the action of a high shear mixer. Other parts that are subjected to the constant parts are the impellers and paddles.
A high shear mixer granulator also has some stationary parts. They include the tank chamber, vane, and baffles. They provide a perfect containment for the materials which are subjected to continuous motion.
The materials in the high shear mixers don’t have to be uniform or be of the same type. You can put both solid and liquid into the high shear mixer to achieve a homogenous product such as dispersions, suspensions, and emulsions, among others. These activities set a perfect step for the granulation of the materials.
In addition to the mechanical aspects of the product, the physical designs of the high shear mixer granulators are optimized for the best production. They are completely sealed to prevent contamination of the materials during the mixing and shearing process. The design also allows easy filling and discharge of the materials from the high shear mixer granulator.
1.2. What is granulation?
The main function of the high shear mixer granulation is to execute complete granulation of the materials. So, what is granulation?
The granulation process entails the formation of granules from powder materials. It results in the formation of dense and sturdy granules used in the later stages of product creation. Granulation is essential for the optimal handling of the materials. It is a standard process used in pharmaceutical, chemical, cosmetic, and many other industries.
During the granulation process, fine particles and powder are agglomerated to form large granules. The size of the granules may vary depending on what you intend to achieve with the final products and your application area.
There are several factors why manufacturers prefer to undertake granulation as a key step in their product formation. The most common reason is to minimize segregation of the particles and ingredients of the powder.
Usually, powders come in different sizes, shapes, and densities. All these properties need to be segregated when you plan to use them for making homogeneous products. Granules produced from the granulation process tend to have defined shapes and have better flow properties.
The granulation process can be either wet granulation or dry granulation.
Wet granulation is when the binding fluid is added to the mixing chamber to form the granules. The fluid is used to increase the bond between the particles. Water is not used for wet granulation because it will dry up, and this will cause the disintegration of the particles.
On the other hand, dry granulation does not entail the use of fluid or any other liquid. It is mainly used on materials that are sensitive to wetness or high moisture content.
Instead of water, high-impact pressure is exerted on the fine particles until they join to form a contact granule.
A high shear mixer granulator can granulate both large granules and small granules when it comes to granulation. An impressive feature of the high shear mixer granulator is it gives you the option to determine the size of the granules.
1.3. What are the applications of high shear mixer granulators?
Do I need to buy a high shear mixer granulator for my industry? This is a question that you may consider asking before making such a heavy purchase.
High shear mixer granulators are used in an array of fields and industries for granulation purposes. Butt before we dig deep into the application areas, let’s first look at the importance of the granulation process in product preparation and processing.
▣ Improve the flow of the powder.Most manufacturing processes are characterized by the movement of materials from one stage to another. However, powder, in its original forms, can be very difficult to move around. This makes it necessary to turn them into fine granules for easy flow. In other words, it improves the mechanical properties of the powder.
▣ Uniformity of the materials: High shear mixer granulators are vital in enhancing the uniformity of the particles. Large and small particles of materials are aggregated to have the same size. This is an important feature that enhances the quality of the product.
▣ Easy handling and storage:Agglomerated particles, as a result of the granulation, are easy to handle and store. They are better than a fine powder.
Here are some of the most common industries that utilize high shear mixer granulators.
▣ Pharmaceuticals: These are companies that are heavily involved in the manufacturing of drugs and medicinal substances.
▣ Food and beverages: Ingredients for making different food products have to undergo mixing and granulation before they are subjected to further processing.
▣ Cosmetic and toiletries: These are companies that make beauty products and other products used for household cleanliness. The products include soaps, creams, ointments, and detergents
▣ Agricultural products: Companies that deal with agricultural products tend to utilize the high shear mixer granulators fully. They use this pharma equipment for making farm animal and pet feeds.
▣ Chemical manufacturing companies that manufacture heavy chemicals tend to utilize the high shear mixer granulators fully. Such companies include those that manufacture paints, paper manufacturing, and lubricants, among others.
Is your company involved in any of the above production processes? Then, chances are you are a perfect candidate for the high shear mixer granulator. Contact us, and we will get the proper granulator for your application. We may even customize the high shear mixer granulator to be perfect your production field.
1.4. Features of the High Shear Mixer Granulators
Let’s look at some of the most outstanding features of the high shear mixer granulators. These are the key aspects of the product that determine the overall performance of the shear granulator;
▣ One-step mixing and granulation: The mixing and granulation of the materials in a high shear mixer granulator are completed in a single cycle. There is no need to transfer the materials from one stage of production to another to achieve complete mixing. This feature comes in handy when you want to save time for the production process.
▣ Automatic discharge of the materials: After the materials have been thoroughly mixed, they will be automatically discharged from the high shear mixer granulator. Of course, a connecting tube facilitates the transfer of the materials from the high shear mixer to the next stage of production. The automation process also helps to save time and minimize wastage of the materials due to spillage.
▣ Equipped with Z-blades: Senieer the rapid mixer granulators are well-equipped with a set of special Z-shaped blades. The operational parameters of these blades ensure that they exert equal force on the materials during the mixing process. The blades also ensure that the forces are equally distributed throughout the mixing chamber.
▣ Fully enclosed production chamber: Our high shear mixer granulator is enclosed, and this complies with the GMP standards. The enclosed environment minimizes contamination from external factors. It also protects the working environment from pollution in case you are mixing toxic materials.
▣ Easy access and monitoring: Despite the production taking place in an enclosed chamber, you can easily access the content of the materials that are in the high shear mixer granulator. It has openings and lids that are strategically positioned to give you full access. The device also features a glass hole that is positioned on the door. You can use it to have a clear view of the happenings inside the chamber.
▣ Positioned agitator: The rapid mixer granulator features a well-positioned agitator that is designed for causing the movements of the materials. It ensures that the materials produce strong vortex movements. Keep in mind that the movements of the materials will determine the quality of the mixing and granulation.
▣ Features axial sealing: The body of the Senieer high shear mixer granulator is characterized by an axial sealing effect. This feature plays a role in preventing the contamination of the material by the grease.
▣ Simple design: Senieer high shear mixer granulators feature a simple design. All the components of the high shear mixer granulators are accessible to the operator from any point. The simplicity of the high shear mixer also makes them easy to handle and use.
▣ Safety features: Our high shear mixers are equipped with different safety features. One of them is the interlock protection function. Also, the electric components of the high shear mixers are well-labeled and shielded from any risks of electric-related accidents.
▣ Easy interconnection: You can easily connect high shear mixer granulator to other equipment in your production chain. For example, it is easy to connect with bins that will be used for storing the materials that have been mixed and granulated. This also streamlines the integration of the rapid granulator into any stage of production.
▣ Touchscreen and PLC control: You can execute all the actions on the mixer granulator using an elaborate PLC control panel. The user interface of this control system is by a touchscreen pad which is perfectly sized to give a maximum response.
▣ Temperature control feature: You can easily control the operational parameters of the high shear mixer granulator. This is possible by equipping the container with a jacketed pot which is ideal when it comes to both heating and cooling the pharmaceutical machine.
▣ Made of recommended material: The bodywork of the high shear mixer granulator is made of quality material that will support the shearing and mixing activities without any glitches. The material must be able to withstand all the activities that take place in the mixer granulator without getting damaged. Also, the metals must be inert to the chemical reactions due to the materials being processed by the high shear mixer granulator.
▣ GMP and FDA compliant: Senieer high shear mixer granulators are fully compliant to the Good Manufacturing Practice (GMP) standards. In addition to that, they are also compliant with the FDA. These are major standards that the manufacturers of pharmaceutical equipment are required to meet for their products to be accepted in the market. They are sure proof that our high shear mixer granulators are of high quality.
1.5. Advantages of High Shear Mixer
Should I buy the best Senieer high shear mixer granulation in China? This is a question that you are likely to ask yourself before making such a critical purchase. To make this decision, it will be prudent to outline the cons and pros of a typical high shear mixer granulator.
Here are the main benefits and advantages of the high shear mixer granulator;
It saves time and money
If you are in the business, you definitely understand the essence of time. Our high shear mixer granulators can help you save as much time as possible. The timely mixing and granulation of the materials will ensure that you can achieve much in less time.
Also, the ability of the high shear mixers to handle large volumes of the material at any given cycle will help you save on the time required for mixing and granulation. Achieving granulation in a short time will allow you to focus on the other key aspects of production.
Uniform round granules
Would you like all of your granules to have the same shape and structure? We have the right solution for you. You can easily achieve this goal using the best mixer granulator.
The operation and working mechanism of the high shear mixers granulators will ensure that you get well-rounded granules at the end of the granulation process. The good thing is that all the granules will have the same appearance and structure. This will eventually improve the quality of the final product.
Requires less binder solution
Choosing high shear mixer granulators means that you will spend a minimum amount of money on the binder solutions. These are solutions that are used for binding particles of a material. The good thing is you will still achieve dense materials even without using the binder solutions.
Increases density of the granules
It is easy to achieve great densification of the materials by using high shear mixer granulators. The elaborate mixing process of the granulator ensures that the individual particles of the material are properly bonded to each other. This means that even the most brittle materials will have a high density at the end of the process.
Prevents the contamination of the materials
The agile design and precise construction of the high shear mixer granulator limit the exposure of the materials to various forms of contamination.
The fact that the high shear mixer granulator is enclosed keeps off the air-borne contaminants from getting into the mixing chamber.
Also, the construction of the high shear mixer granulator is optimized for the highest levels of sanitation. This minimizes any chances of cross-contamination of the materials.
Prevents pollution the work environment
The construction of the high shear mixer granulator helps to minimize pollution due to the mixing and granulation process. Dust particles will not find their way from the container thanks to an air-tight enclosure of the rapid mixer granulator.
By minimizing pollution, high shear mixers help to promote a healthy and productive working environment. This is vital, especially when mixing and granulating toxic products.
Reduces the drying time
Unlike other mixing and granulation methods, you will spend less drying time whenever you use a high shear mixer granulator. This is because the machine does not involve heavy use of the binding solutions. A short drying time has a direct impact on speeding up the rate of production.
Flexible and versatile
High shear mixer granulator is a highly versatile pharmaceutical machine. It can be used for mixing and granulating different types of materials that have different physical and chemical properties. This explains why granulators have a wide range of applications.
So, next time you have materials and you are not sure which machine to use for mixing and granulating, think about the rapid mixer granulator. It will execute the job as per your expectations.
Accurate production of the granules
Perhaps this is among the top reasons why you should buy high shear mixer granulator in China. It operates with the highest levels of accuracy. At the end of the mixing and granulation, you will get granules with well-defined shapes and structures.
The accuracy of the process also helps to preserve the quality of the granules and particles. High shear mixer granulators do not have any adverse chemical and physical effects on the particles
Predictable results
The high accuracy of the high shear granulator is among the key reasons behind the predictability of the machine. You can easily predict the output of the granules. You will know how the final granules will look like.
This is unlike other granulating machines, where you will not know what to expect at the end of the process. The predictability of the process also gives you time to make plans and arrangements for the product and other phases of production.
Easy to control
You can easily control the performance and control parameters of the high shear mixer granulator. This is possible through the touchscreen PLC control system. Everything that you would like to execute is right there within your reach.
The control feature of the high rapid mixer granulator ensures that you can achieve your desired levels of mixing and granulation.
With these advantages, there is no doubt that buying a rapid mixture granulator is a worthy investment that deserves your attention. Consider getting it for maximum production and profitability.
Chapter 2: Parts/ Components of High Shear Mixer Granulator
Beyond the physical outlook, tons of components make up the high shear mixer granulator. All of them work in unison to deliver a functional system. Let’s have a brief overview of the main parts that make up a high shear mixer granulator;
Rack system
The rack system is the external component that supports the high shear mixer granulator and ensures that it remains in a perfect position to deliver its core functions. It also enhances the safety of the high shear mixer granulator, ensuring that those around don’t get injured when operating it. It also gives access to the rapid granulator.
The rack system comprises other key components, including the frame, ladder, and access door. In addition, the design of the rack system ensures that it supports the aprons connected to the main granulator container.
The rack system features notch cuts on its edges to ease the connection with the rapid granulator. However, some sections have bolted for tightening the connections and enhancing the stability of the granulator.
The design of the granulator’s rack system is such that you can easily install and uninstall the high shear mixer granulator without putting too much struggle into the process. It will take you less than 10 minutes to do the job.
Also, since the rack system plays a supporting role, we ensure that we use quality material for the system. It is made of stainless steel.
The mixing container
This is where the actual mixing and granulation takes place. It is a large container designed to accommodate the materials and support different activities that will result in refined granules.
The mixing container has a conical design that supports the easy flow of the materials to the rounded bottom section of the container. The design is continuous and devoid of dead spots to ensure that the materials don’t stick inside. This is further enhanced by the well-polished surface to minimize adhesive force between the walls of the container and the material.
The mixing container of a high shear mixer has a significant level of thickness that will easily support the mixing and granulation process. Of course, this is in addition to the high-grade stainless steel that makes up the container’s body.
Mixing containers for the rapid granulators come in different capacities to accommodate different production needs. They are usually labeled in liters, and you should choose one that will match your needs.
The air-tight construction of the container is to prevent leakage of the materials during the mixing and granulation. This is vital given that these processes you are characterized by high pressure and vigorous physical activities.
It has lids that control the entry and extrusion of the materials from the container. The lids also preserve the quality of the materials by preventing contamination due to the foreign objects getting into the container.
Other than the lid, the main mixing container has other ports that are used for different purposes. For example, there is a port that is connected to the washing ball. This port ensures that you can easily clean the container.
The container has a port that links to the feeding funnel. This is usually applicable in the automatic operation where the materials will be fed into the container automatically. Other ports can be connected to the exhaust air system when necessary.
The mixing system
The mixing system of the high shear mixer granulator executes the actual mixing of the material. The primary goal of this system is to achieve a homogeneous material that is ready for granulation.
Image of the mixing system of the high shear granulator
The system executes numerous tasks to achieve the desired uniformity of the materials. One of them is crushing the large particles into the desired sizes.
The mixing system has Z-shaped blades that move rapidly to cut and slice the materials that get in through the feeding system. This component is usually significant when the materials contain large particles. They will have to be sliced into small sizes before they are used for making granules.
The blades rotate, creating centrifugal force in the container. This force allows the sliced materials to pass through the sieve plate. Meanwhile, the sieve plate will continue granulating the particles.
The performance effectiveness of the blades is determined by their rotating speed. The faster they rotate, the more abrasive they will be on the materials. However, this will depend on the materials in the shear granulator. The good news is you can control the speed of the blade using the PLC control panel.
Mixing rotor/Agitator
The function of the agitator in a high shear mixer granulator is to mix the materials. They mix the materials by rotating at different speeds. They are also aligned at specified angles that allow them to exert optimum force on the materials for the maximum mixing of the particles.
Like the blades, you can also adjust the speed and torque of the agitator. These two parameters will affect the quality of the mix. The agitator rotors are driven by rotors. This means that they don’t run independently.
Agitators usually come with a defined speed that is indicated by the manufacturer. The speed can range from 53 rpm to 500 rpm. This is usually determined by the specifications of the current motor. You can control the speed using the speed controller at the control panel.
The mixing rotor is designed to prevent incidences of air purging. Also, its air purge system prevents the material from getting into the agitator to slow down the rate of mixing.
The discharge unit
The discharge unit if a high shear mixer granulator plays the role of extruding the granules from the machine. By the time the materials reach this stage, they will be ready for the next stage of processing.
The discharge unit operates by the pneumatic force. It also has cylinders and valves that facilitate the movement of the products from the machine.
The discharge unit is also designed to minimize the contamination of the materials as they exit the system. This ensures that the material’s quality and purity are preserved for subsequent use.
The discharge unit has valves that open to allow the materials to exit. Otherwise, it will always remain closed during the normal operation of the high shear mixer granulator.
The capacity of the discharge system matches the production capacity of the high shear mixer. The manufacturer can also customize the discharge unit to suit your production needs. It is also strategically positioned to facilitate the free flow of the materials.
Control system
A high shear mixer granulator has an elaborate control system. The primary function of this system is to control the actions and operations of the whole machine.
A typical control system comprises the hardware component, software parts, and electrical auxiliary parts.
Sample image of the control system;
The control hardware encompasses the whole system that supports t buttons, touchscreen, and PLC system. It also houses the electrical components of the rapid mixer granulator. The hardware gives the operator easy access to the control system of the high shear mixer granulator.
Graphical User Interface is another distinct aspect of the control system. As the name suggests, it provides an interface between the operator and the machine. It provides the operational parameters of the machine.
On the GUI, you will be able to see the speed of mixing, temperature, granulation rate, volume, and much other valuable information that you need to know about your high shear mixer granulator.
The software aspect of the rapid shear granulator controls access to the system. It is programmed to allow and restrict access to the machine by different users. The software also works with different sensors to relay relevant information regarding the operational parameters of the high shear granulator.
The software also allows you to choose different operational modes rapid granulator. You may be required to update the software regularly according to the manufacturer’s specifications.
Motor driver
This is the main driving system of the high shear mixer granulator. It is responsible for driving all the other operations of this rapid shear granulator.
The motor driving system determines the movements of the agitator, blades, and impellers of the mixer granulator.
Auxiliary parts
There are other parts that, even though they are not the main components, assist in the normal operations of the high shear mixer granulators. They ensure that the mixing and granulation process happens smoothly and effectively.
These complementary components include;
Data recorder system
Normally, you would like to keep track of the operation of your rapid granulator. A data recorder system can help you do this job.
It comprises a recording module that records the data and a printer interface that allows you to read the data.
UPS for the control module system
The UPS device comes in handy whenever you are facing frequent disruptions of power supply onto the device. It ensures that the mixer granulator continues to operate for some period after the main power supply has been cut off. It is mainly used for shielding the control system from mechanical and electrical damage after the interruption.
Remote diagnosis module
How can you tell that the high shear mixer granulator has some mechanical, electrical, or software problems? Simply use a remote diagnosis modem. Plug the modem into the device, and it will collect all the necessary information regarding any flaws in the machine.
However, before you buy any of these auxiliary device for your high shear mixer granulator, ensure that it has been recommended by the manufacturer. This is to avoid issues relating to the incompatibility of the high shear mixer granulators, which may eventually cause serious damage to the machine. ‘
It will also be prudent to ask if the high shear mixer granulator manufacturer has all the relevant spare parts for the machine.
Chapter 3: Working Principle of a High Shear Mixer Granulator
A rapid mixer granulator has a simple working principle that you can easily understand. It accepts materials of different particle sizes and transforms them into well-defined granules that can be used for various applications.
The granulation of the particles in a high shear rapid granulator is executed due to the mixing, whirling, and tumbling of the materials. The actions are subjected to both dry and wet materials. The rapid mixer granulator uses its impellers and choppers that rotate at high speed to mix and cause the granulation of the materials.
Other than the primary materials, binder solutions are added into the impeller, which at this time operates at a relatively slower speed. This results in the formation of a wet mass. The rotating speed of the chopper and impeller then increases to chop and slice the damp mass into small-sized granules.
The mixing and granulation process takes approximately less than 10 minutes, depending on the nature and properties of the materials. The process takes longer for the wet granules than for the dry granules. At the end of the process, you will be able to achieve granules of different sizes.
To make things clearer, here are the steps for the rapid mixer granulator;
Step 1: Preparing the materials for the rapid granulation
It all starts by verifying that the materials and ingredients meet the minimum standards for the high shear mixer granulator. If not, they are subjected to numerous procedures that are designed to make them machine-ready.
Preparing the materials is an important step as it guarantees quality output at the end of the mixing and granulating process. It also helps to protect the rapid mixer granulator from mechanical damage in case the material contains dangerous impurities such as metallic objects.
Other pharmaceutical and industrial machines may e used during the preparation stage of the materials. For example, you may have to use a Senieer bin blender to blend the materials before granulating them. Conical mill and vibrio sifters are just other equipment that may come in handy whenever you are preparing the materials for rapid granulation.
In most cases, the activities at the preparation stage are determined by the nature of the materials and what you intend to achieve from the rapid granulation process.
It will be better to outline all the key properties of the material, including rigidity, corrosiveness, the moisture content in the material, the bulkiness of the material, compressible, temperature range, among others.
Once you are satisfied with the level of the preparations that have been done, you can proceed to the next stage of rapid granulation.
Step 2: Charging the materials
The second step of the process entails loading up the materials into the rapid mixer granulator. This process is straightforward as the quality of the material has already been verified at the previous stage of production.
It is easier in the automatic rapid granulator as you only need to press a couple of buttons, and the materials will start flowing into the mixing container.
The opening of the granulators is usually located at a high position to facilitate the free fall of the materials into the container. The force of gravity will do the rest of the job.
The flow of the materials into the container will stop once you have achieved the desired volume of the materials to be granulated. Fully automatic rapid granulators have sensors that will automatically stop the inflow of materials.
Step 3: Commencement of the mixing and granulation
After all the ingredients have been deposited in the rapid mixer granulator, the stage is set for the actual mixing and granulation process. The vacuum valve will close to stop any further charging, and the exhaust valve will open.
At this point, the high shear mixer granulator will start working on the ingredients or the materials. The choppers and impellers will begin moving to act on the material. The repeated motions of these components are what we refer to as the mixing and granulation process.
You can use the control system of the rapid mixer granulator to determine the motion of the chopper and impellers. For instance, you can increase or decrease their rotation speed. You can also adjust the degree to which the choppers and the impellers hit the material.
All the settings that you perform on the control system will depend on the type of material that you are trying to subject to the rapid granulation. If you are not sure of what settings to use, then you may consider working with the standard settings.
Step 4: Adding a binding solution to the material
As the mixing and granulation processes continue, it will be necessary to add a solution binder to the material. The addition usually happens automatically, at least for the automated high shear mixer granulators.
A binder solution is an essential ingredient for the agglomeration of the particles to form granules. A nozzle is opened to spray the solution evenly in the mixing container.
Different types of binder solutions are used in the high shear mixer granulators. They include;
Organic solutions: These solution binders are mainly made of organic compounds. They are ideal for materials that are sensitive to moisture. You can use them if you want to achieve fast drying of the granules after the granulation process.
Aqueous solutions: This solution is widely used in rapid mixer granulators due to various reasons. One of them is availability. Aqueous solutions are easily available. They are also cheaper than organic binder solutions. Pure water is just one of the aqueous solutions that are used for binding the ingredients. The main issue with this type of binder is it takes a long to dry. Also, it cannot be used on materials that are sensitive to water.
The solution binder is introduced into the materials continuously until they form sizable agglomerates. You will start noticing large lumps in the main container. This is the time that you may stop mixing and granulation.
Step 5: Discharging granules
After the granules are fully formed, the next stage is the discharge process. The process is activated by the sensors which reduce the activities of all other components. For instance, the speed of the impeller will be very slow.
The discharge door will open to allow the granules to pass through. Thereafter, the granules will exit the system through the milling unit. The granules will move to the milling chamber where they will be further crushed into smaller sizes.
Once the granules have been fully discharged, they will be prepared for the next processing stage. In most cases, they are dried.
Step 6: Drying of the granules
As we have seen, the mixing granulation process entails the use of the binder solution. This means that the output of the process will eventually be wet. However, it will be difficult to use these granules in their wet or moist state. This is why they must be dried.
Some mixer granulators are embedded with a drying chamber that is responsible for the drying of the granules. Alternatively, the granules are moved to the fluid bed dryer where they will be subjected to a complete drying process.
The dryer will ensure that the granules achieve the minimum level of moisture. From here, it will be easy to store the granules for future use.
Chapter 4: Technical Specifications of the High Shear Mixer Granulators
When buying high shear mixer granulator, the first thing that you will look into is the physical aspects of the machine. These are things like the design, size, and weight of the pharmaceutical equipment. From there, you will start looking at the technical aspects of the product.
Technical elements tend to affect the performance and usability of the high shear mixer granulators. They determine the quality of work that you will get from the granulator.
Also, the technical characteristics of the high shear granulator will affect the handling of the machine. They have an impact on whether you will have an easy time when using the mixer granulator or you will strain when using it.
Let’s look at some of the key technical aspects of the rapid granulation mixer that you should know before you proceed to buy one;
1. The rated output
This is the volume of the granules that can be extruded from the high shear mixer granulator at any given time. The rated output is usually calibrated in the weight per batch or kg/batch.
This specification is important as it determines the volume of the granules that the high shear mixer will be handling. It also has a direct impact on your productivity.
The rated output is also calibrated in terms of density. This defines the density of the granules in each batch of production.
2. Mixing time
High shear mixer granulators are usually rated according to their mixing time. This is also another technical specification that has a direct impact on the level of your productivity. There is a high chance that you will prefer a high shear mixer that takes less time to mix and make the granules.
3. Mixing speed
The speed usually determines how fast or slow the high shear mixer granulator operates. The speed is usually calibrated in terms of the rpm. This affects the rate at which the impellers will be mixing the materials inside the mixing and granulation chamber.
The speed is usually labeled in range. You can find a rapid granulator that has been labeled 200-1100rpm.
Also, the rapid granulator is labeled according to the copping speed. This is the speed at which the machine can slice and trim the granules into different sizes. The speed can range between 500rpm-3000rpm.
4. The motor power
Rapid mixer granulators are powered by different types of electric-driven motors. These include the mixing motor and the chopping motor. So, the manufacturer must label the power capacity of the motor.
Check the power output of both the chopping motor and mixing motors.
5. Compressed air
Find out the pressure of compressed air that I the rapid granulator requires in every processing batch. Also, check the volume of the compressed air that the granulator consumes per minute. This is labeled in terms of m3/min.
6. Noise level
Since a rapid mixer granulator is mechanical equipment, you should expect some level of noise from the machine when it is in operation. This is why the noise level is another technical specification that you should check out on the equipment. The noise is usually labeled in terms of decibels (dB).
7. Dimension
The dimensions define the physical size of the rapid mixer granulator. The dimensions are usually calibrated in terms of length, width, and height of the equipment (L×W×H). They will give you a clue about the handling capability of the high shear mixer granulator.
8. Equipment loading scheme
The loading scheme defines the mode of charging and discharging the material into the rapid granulator. There are two main types of loading schemes. These are manual and automatic loading.
For the manual scheme, an operator or technician physically discharges the materials into the rapid granulator. The process is slow and tedious. You can choose it if you are operating on a smalls scale.
In the automatic scheme, the transfer of the material is aided by other equipment and external forces. They include a vacuum transfer system and the force of gravity. The automatic loading scheme is fast efficient and ideal for large-scale production.
9. Discharge scheme
This defines the methods and techniques of discharging the materials from the high shear mixer granulator. Some granulators have an automatic discharge scheme while others have a manual system. Again, your choice will depend on your production levels and preferences.
10. Monitoring panel
The main function of the monitoring panel is to allow see the shearing and granulation process. These panels come in different forms and specifications. Some have lamps that illuminate inside the mixing chamber. Find out the type and specification of the observation panel that is embedded on the high shear mixer granulator before you buy.
11. Rapid granulator operation modes
Most high shear mixer granulators in the market have two main modes of operations. These are;
Manual operation: this mode gives the operator maximum control over the key functions of the high shear mixer. You are free to adjust or alter some operational parameters for the sake of achieving the desired levels of mixing and granulation.
Automatic mode: This mode automates most of the activities during the mixing and granulation processes. There is minimal human involvement in the operation.
Find out the operational mode that comes with your high-shear mixer granulator or whether the equipment will allow you to switch from one operation mode to another.
12. The control system settings
The control system is part of the technical features that you should know about the high shear mixer granulator. Find out the key characteristics of the control settings and their usability.
Check the user interface of the control system. Is it touchscreen or does it have buttons? Between these two interfaces, which one are you more comfortable with?
Also, find out the operational parameters that are in the control settings. These include temperature regulation, pressure monitoring system, and timer.
13. Material specifications
As we have seen, the high shear mixer granulator comprises different components. Each component is made of a unique type of material. Verify the material that is used on each component before you proceed to buy the best rapid mixer granulators in China. The key components and their materials include;
-Main mixing compartment: This part of the rapid mixer granulator should be made of high-grade stainless steel material. The 316L stainless steel is an ideal material for this component. It is strong and resistant to both physical and chemical damage due to granulation.
Filter bag: The filter bag should be made of a medical-grade antistatic material. This material filters off the particles from escaping during the mixing and granulation process.
Ducts: the ducts facilitate the flow of material from one section of the rapid granulator to another. The duct is also made of grade 304 stainless steel.
Apart from these, verify to ensure that all the other components are made of quality materials Keep in mind that the nature of the material will determine the durability, effectiveness, and safety of the rapid granulator.
14. Safety features
Another critical specification is the safety feature of the high shear mixer granulator. These are devices that make it safe to use the equipment. The external components of the rapid mixer granulator should be made of a flame-proof material.
Other safety features that the equipment may include an alarm system. This will alert you in case of any abnormalities in the system. Also, check out whether the rapid mixer granulator has an emergency stop system. This safety feature allows you to turn off the granulator at any time in case of an emergency.
15. Heat protection feature
Mixing and granulation entail the generation of heat. The manufacturer should specify the methods and tools for heat management. This is vital because high heat can cause severe damage to the materials and degrade the quality of the products.
There should be an insulation system to shield the rapid mixer granulator parts from the adverse effects of heat.
16. Rapid mixer granulator cleaning system
Cleanliness is among the key tenets of using a rapid mixer granulator. Ensure that it is clean before you use it for processing any type of material. So, it will be prudent to check out the type of cleaning system that the granulator has.
Check if the rapid mixer granulator has a WIP automatic washer. This is a well-known cleaning system that is known for its reliability when it comes to cleaning the equipment.
Chapter 5: Factors Affecting the Granulation Process
After buying a rapid granulation mixer, the next thing that you will think about is getting the best granules from it. However, sometimes you may not end up with the best granules. This could be due to various reasons. Here are some of the key factors that end up affecting the granulation process.
Formulation variables
These can be defined as the ingredients that make up the materials to be subjected through the mixing and granulation process. The physical arrangement and properties of the particles will determine the final result of the granulation process.
Also, keep in mind the chemical properties of the formulation variables. Will the mixing and granulation process have an impact on the variable? If so, then you should expect some issues on the final granules. It will be prudent to know all the properties of the formulation variables before feeding them into the high shear granulator.
Another aspect of the variable formulation is the density of the variables. Some have high density and others are less dense. How the mixer granulator will handle their densities will affect the quality of the final granules.
Physical properties of the ingredients
This is another key property that directly affects the quality of the granulation process. One such property is particle size. Some ingredients have large-size particles while others have small particles. The rapid mixer granulator will have to break down these large particles to smaller sizes before they are subjected to further processing.
Also, the distribution of the different particle sizes matters. The high shear mixer granulator will easily granulate materials whose particle sizes are uniformly distributed.
Binder materials used
The binder materials that you use in the high shear mixer granulator will determine the final quality of the granules. As we have seen there are different types of binder solutions and each type has its chemical properties.
The interaction between the binder solution and the particles will determine how the granules will form. The binder may foster the accretion and coalescence of particles. This is when the particles become tacky and form solid granules. On the other hand, poor coalescence will lead to the tumbling of the granules.
A good binder solution will also enhance the strength of the granules. Such granules tend to have well-defined shapes and sizes.
Chapter 6: How to Choose High Shear Mixer Granulator
So you are looking for the best high shear granulation mixer in China? Here are some of the most effective tips that can help you to end up with the right equipment for the job.
6.1. Brand reputation
The brand is everything when it comes to buying valuable equipment such as the best mixer granulator. Choosing a reputable rapid mixer granulator manufacturer is the surest way of ensuring that you end up with the best high shear mixer granulator.
Reputable high shear mixer granulator manufacturers and suppliers have built a name in delivering reliable equipment. These are strong durable and functional mixer granulators.
Also, customer service is one of the key characteristics of a reputable high shear mixer granulator. Such companies are dedicated to meeting the needs and aspirations of their customers.
But, how can I tell that a particular rapid mixer granulator manufacturer is reliable or not? There are several ways of weeding out the best brands from the rest. One way is by finding out the previous customers that have bought from the manufacturer. What opinions do they have about the company?
The easiest way is to read the high shear granulator reviews. They will give you deep insights into what you should expect from the company.
6.2. Go for flexibility
There are various ways of interpreting the flexibility of a rapid mixer granulator. One way is the ability of the mixer granulator to be used for granulating different materials. The mixer should be able to accommodate large and small granules dense and light granules.
Another way of interpreting the flexibility is the ease of moving and transporting the rapid mixer granulator within your premises. The machine should not be too heavy such that its mobility is greatly limited.
The flexibility of the Senieer rapid mixer granulator allows it to be easily used for a wide range of applications. Also, the lightweight construction of the high shear mixer granulator comes in handy when you want to move the equipment around.
We can also view the flexibility from the ability to connect and integrate the rapid granulator with other pharmaceutical equipment such as a fluid bed dryer and conical mills.
6.3 Ease of using
The usability of the high shear mixer granulator is a key factor that you cannot afford to ignore. You don’t want to have complex equipment that will give you hard time when it comes to using it in your industry.
Several factors determine the ease of using or usability of a high shear mixer granulator. One of them is the equipment design. The design should be simple and easy to understand. The operator should be able to access all the key components of the machine with ease.
The user interface and control mechanism of a rapid mixer granulator is another aspect that determines the ease of using a high shear mixer granulator. The control panel should allow you to execute all the key operational parameters.
6.4. Safety features
Check whether the rapid mixer granulator has all the essential safety features. These are components and properties that enhance the safety of using the equipment. The last thing that you can think of is getting injuries and accidents when using your high shear mixer granulator.
There are several things that you should look at when assessing the safety of the rapid mixer granulator. One of them is the equipment design. It should be designed with the safety of the user in mind.
Heat management is another tenet that determines the safety of using a high shear mixer granulator. The material of the equipment should minimize excessive radiation of heat to the surrounding especially when it is in operation.
The rapid mixer granulator should also be shielded from electric-related accidents. All the electric cables should be insulated. It should have a self-regulatory mechanism to protect against the effects of the current upsurge.
Of course, the safety features can be implemented only if you ensure that only qualified personnel operate the rapid mixer granulator. Some of this equipment has a locking mechanism that prevents unauthorized users from handling the machine.
6.5 . Cost-effectiveness of the rapid mixer granulator
You cannot ignore the cost factor when planning to buy the best rapid mixer granulators in China. You would like to end up with the most cost-effective rapid mixer granulator. There are different ways of looking at the issue of cost.
The most common way is by looking at the price of the rapid mixer granulator. Do you afford the high shear mixer granulator? Compare the prices of different high shear mixers then choose one that easily fits into your budget.
However, when doing a price analysis, do not overlook other factors at the expense of the price. For instance, the high shear mixer granulator may be cheap because it features poor quality build or has limited functionality.
Another aspect of assessing the cost-effectiveness of the high shear mixer granulator is by analyzing its running expenses. What is the cost of running the high shear mixer granulator? Find out the power consumption of the mixer granulator as this will be a major issue when doing the cost analysis. You may also inquire about the cost of maintaining the high shear mixer granulator.
6.6. Detailed features and functionalities
Put your attention on the deep details of the high shear mixer granulator. Start with the key technical specifications that we have listed above and analyze each one of them. This is the only way of knowing whether the RMG will perform according to your expectations. For example, the rapid mixer granulator capacity will tell you the volume of material that the granulator can handle.
Find out the components that are embedded in the RMG and whether all of them are fully functional. In short, pay attention to all the details that matter with regards to the high shear mixer granulator.
6.6. International standards and regulation
Check out whether the rapid mixer granulator meets international quality standards. One of the most common standards is the Good Manufacturing Practices (GMP) which stipulates the standards that the manufacturer is supposed to follow. Others include FDA, ISO among others.
All these standards prove that the product meets the highest quality for industrial applications.
6.7. Why Choose Senieer High Shear Mixer Granulator?
Senieer is a reputable rapid mixer granulator manufacturer in China. There are solid reasons why you should buy our high shear mixer from us. Here are some of these reasons;
▣ Quality high shear mixer granulator: At Senieer, we don’t compromise when it comes to the quality of the rapid mixer granulator. All the components of our rapid mixer granulators are made of premium quality materials. We also use the best engineering practices for the high shear mixer granulators.
▣ Customized high shear mixer granulators: We design custom solutions for our clients who are looking for the customized mixer granulators. Whether you want a unique design or would like to have extra features being added, we will do it for you. Simply send us the details and we will work on them.
▣ Affordable high-speed mixer granulator: Probably you are looking for the cheapest high shear mixer granulators. At Senieer, we can help you reach close to this goal. We offer the most affordable mixer granulators in China. Our mixer granulators attract low running and maintenance costs.
▣ Experienced and qualified team: We boast of having a large team of high shear mixer granulator engineers. They have in-depth knowledge and everything that entails rapid mixer granulators. We use our experience and knowledge to deliver quality high sped granulators.
▣ Advanced manufacturing technology: Senieer is equipped with high-tech machines that are used in the manufacturing of rapid mixer granulators. The modern equipment ensures that we deliver quality products within a short time. The use of advanced technology in our manufacturing process is also attributed to the accuracy and quality of our rapid mixer granulators.
▣ FDA/cGMP compliant: As a reputable company, Senieer is fully compliant with all the international bodies that are responsible for regulating the manufacturing of pharma equipment such as the FDA and cGMP. This is just proof that all our products meet the expected international quality and safety standards.
▣ Excellent customer care: We pride ourselves on giving our customers the best services. Starting from the time that you inquire about our products, we will give you full information about our rapid mixer granulators. Even strive to ensure that you are fully satisfied with the high-speed mixer after you have already purchased it.
Frequently Asked Questions about High Shear Mixer Granulator
At this point, it is clear that you have acquired adequate information about high shear mixer granulators. You know how it functions and how it will be relevant in your business.
However, you may still have some questions about this pharmaceutical equipment. Here are some of the questions that most people ask about high shear mixer granulators:
What is the difference between the high shear mixer and a fluid bed granulator?
A common feature of this equipment is both are used for granulation. However, there are some differences between them.
All the operations in a high shear mixer take place in a closed unit. The high shear mixer also encompasses an array of activities, including mixing and emulsification of the materials.
The granulation process in a high shear mixer granulator encompasses two steps. The first step is where the binder material is sprayed on the materials, while the second step is where the machines work on the wet materials to form granules.
The materials in a high shear mixer granulator are dried under moderate temperature to protect the physical and chemical properties of the materials.
On the other hand, the operation of the fluidized bed granulators uses fluid bed processing to execute the granulation and drying of the materials. This method entails the use of an air suspension, and the fluidized bed has spray nozzles.
The working mechanism of the fluidized bed granulator entails spraying the fluidized powder, which already has a binding solution, into the bed. The result of the process will be the uniformly shaped granules.
Another difference between a high shear mixer and a fluidized bed granulator is in terms of the shapes of the granules. High shear mixer granulator forms spherical granules while a fluidized bed granulator forms irregularly shaped granules.
The time taken by these two machines also differs. A high shear mixer is slightly faster than the fluid bed granulator when it comes to the formation of the granules.
Why are my granules not of good quality?
Despite having the best high shear rapid granulator, the quality of my granules is not good. What could be the reason for this?
Different factors affect the quality of the granules from the high shear mixer granulators. One of them is the properties of the granules. The physical and chemical properties of the granules have a direct impact on the output of the granules.
Another critical factor that may prevent you from getting the best quality granules is the nature of the binder solution. This is the solution that is used for binding particles to form granules. Therefore, do not expect the best results if you use a low-quality binder solution.
Also, some binder solutions are not compatible with specific materials. This could mainly be because of the chemical properties of the material. So, you should find out this before using it on your material.
The low-quality granules could also be because of a problem with your high shear mixer granulator. A technical, mechanical, or chemical factor could be preventing the machine from producing the best results. Do some scrutiny to uncover the issue in your high shear mixer granulator.
What are the different types of high shear mixer granulators?
When buying rapid mixer granulators in China, it is important to remember that they are not all the same. They are divided into different categories based on their attributes. Some of these categories include;
Type of dosing used: This classification is based on the method that is used for feeding materials into the mixer. Under this category, we have manual rapid granulators and automatic granulators.
Impeller blade design: Mixer granulators come with different impeller designs. Keep in mind that the design of the impeller blade will determine the quality of the mixing. Some rapid mixer granulators have 3-blade impellers while others have tangential blades.
Impeller location: The impeller blades are positioned differently in different high shear mixer granulators. In some, they are positioned horizontally while in others they are vertically positioned.
What is purging air in RMG
Purging is one of the most effective techniques that are used for cleaning the rapid mixer granulator. The method entails flushing a stream of clean air into the system. This pressurized air will remove dirt and debris that might have been stuck on the components of the rapid granulator mixer.
What is tip speed in RMG
Tip speed is the term that is used for measuring the distance that the disperse blade covers within a given time. The speed is usually determined by the diameter of the blade and the rotational rate of the motor. It is calibrated in terms of m/min.
What is ampere load is RMG
Ampere load is the current that passes through or is consumed by the impeller. This current is first transferred to the motor then it rotates the impeller. Usually, the ampere load is high at the beginning then it starts decreasing over time.
What are the advantages of the high shear mixing equipment?
There are numerous advantages of the high shear mixer granulator including:
▣ Achieves mixing and granulation within a short time
▣ Uses less quantity of binder solution
▣ Easy to achieve dense granules
▣ Uniformly shaped granules
▣ Easy to predict the results of the process
▣ Minimal noise during granulation
Which high shear mixer increases efficiency during granulation?
The efficiency of a measured rapid mixer granulator is in terms of the resources used vs. the quality of the granules output. Different operational features are used for increasing the efficiency of the equipment.
The continuous process of the granulator facilitates a smooth transfer process of the material. It also minimizes the wastage of energy in the high shear mixer granulator.
Also, a rapid mixer granulator is designed to minimize the loss of particles from the system. This means that most of the particles will be used for making granules without recording any losses.
How to calculate blender capacity?
The capacity of the blender is usually calculated based on the 50% capacity of the full blender. For example, if the full volume of the blender is 8 cubic meters, the working capacity will be calculated from the 4 cubic meters.
What is the price of high shear mixer granulator?
Rapid mixer granulators come in different price tags. The price is usually based on the detailed features of the mixer granulator. You can contact the manufacturer directly for all the information about prices
Conclusion
I hope that this guide has given you information on everything that you need to know about the high shear mixer granulator. You can now confidently buy this equipment and use it for your relevant application.
In case you have any other questions other than the ones that we have listed above, feel free to contact us for clarification. As a reputable and reliable rapid mixer granulator manufacturer, we are always willing to give the relevant help that you need.