Pharmaceutical Isolator
- Senieer Isolators are designed according to cGMP
- Isolators for high containment designed for OEL
- Custom made designs available
- Material transfer technology
- Containment glove box
- Alarm system
Isolator : Product Description
Pharma isolator is generally in the clean room of Class C or D level, pharmaceutical isolator creates a controlled atmosphere during the production process by scrupulously respecting the different standards required. It can ensure the protection of the product, the operators and the environment at the same time. Isolators provide full containment of highly active and/or sterile compounds thus offering both operator and product protection.
The pharmaceutical isolator is a bacteriologically sealed enclosure used in the medical and pharmaceutical environment for toxic processes and aseptic filling process. It is made of a perfectly sterile main isolator where the products are handled, stored or packaged using shoulder-high gloves placed on one of the walls. It also includes transfer systems that allow the entry and exit of the products and the elimination of waste without breaking aseptic conditions.
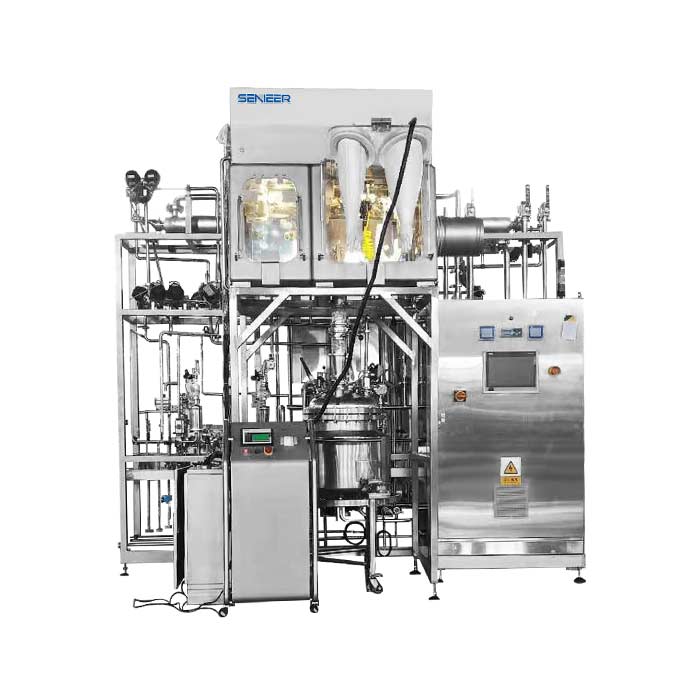
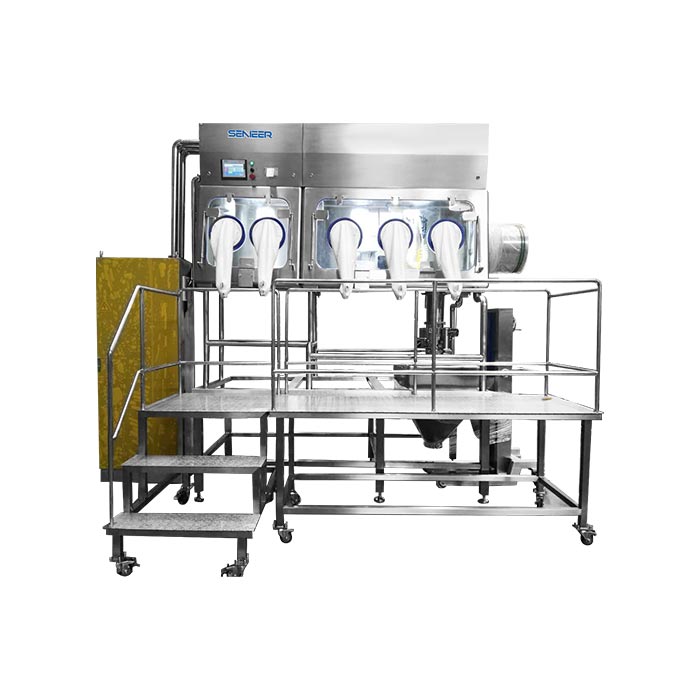
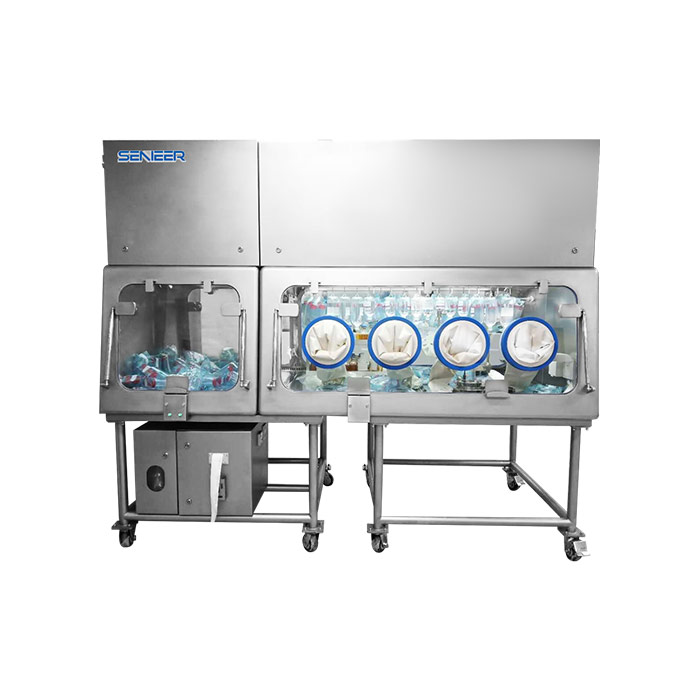
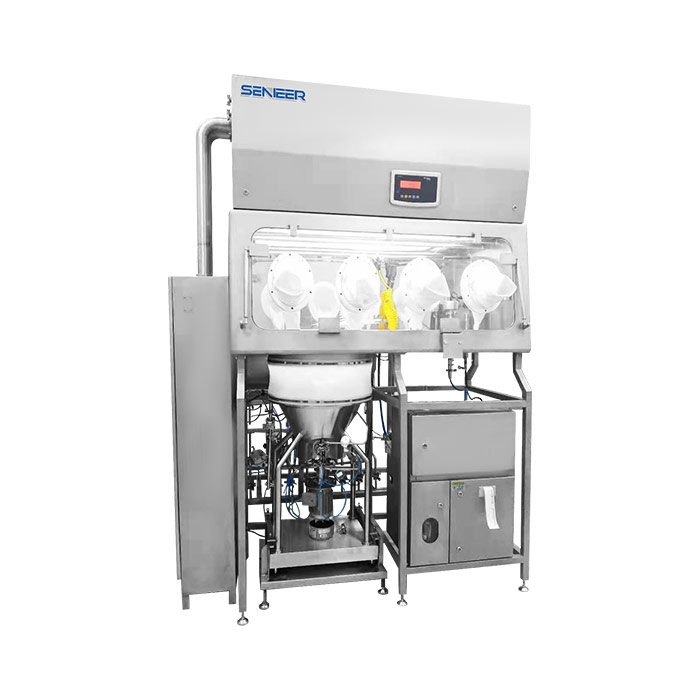
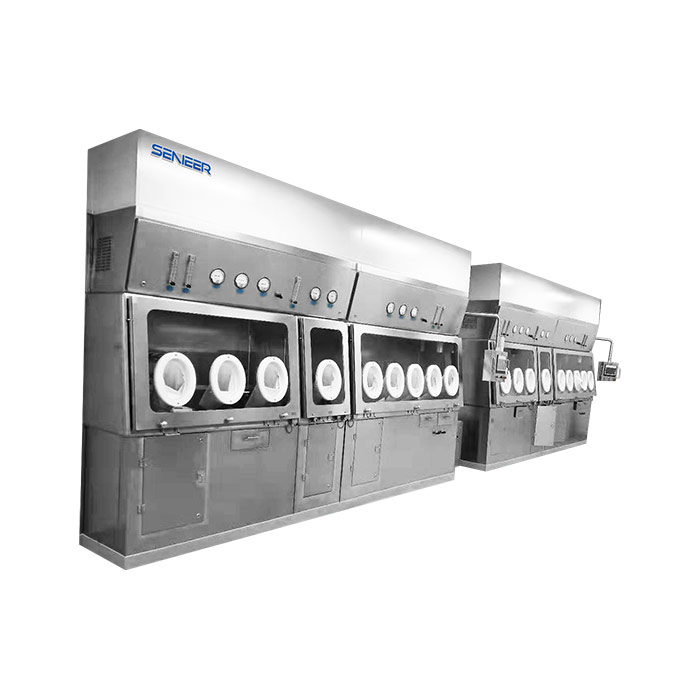
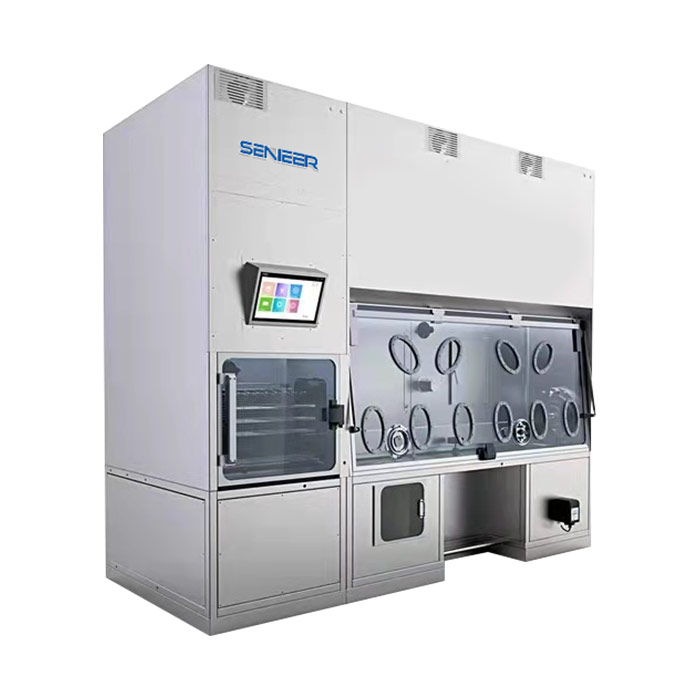
Paramenter of Pharmaceutical Isolator
◈ Made for high grade ss steel (Designed hygienically utilizes stainless steel)
◈ It can be use pharmaceutical, Cosmetics and chemical industries
◈ High containment performance
◈ Radiused corners and seamless surfaces allow for ease of cleaning and decontamination
◈ Integrated aseptic material transfer systems
◈ On-board decontamination/sterilization
◈ Controlled environments for specified set points including temperature and RH
◈ System for continuous monitoring of critical conditions
◈ Advanced ergonomics for the individualized requirements of your workflow
◈ The pharmaceutical industry makes an effort to develop voluntary standards for HPAPI production and handling
◈ Prevent cross-contamination of products.
◈ Safe filtration of exhaust air with double HEPA filters
◈ Inlet filtration HEPA – “A” Class cleanliness
◈ Working chamber and a pair of material airlocks
◈ Chamber interior material stainless steel, powder coated surface
◈ Work surface material stainless steel, polished
◈ Easy-to-clean inner and outer surfaces
◈ An isolator for the pharmaceutical industry reduces costs
◈ The equipment takes up less space, reduces possible refurbishment costs
◈ It offers a superior sterile environment compared to conventional environments such as sterile clean rooms
◈ Positive or negative pressures inside the chamber prevent contamination of the operator or the external environment in case of abnormalities
◈ It ensures long-lasting sterility in accordance with pharmaceutical regulations. It is particularly effective during aseptic processes, procedure validations, sterility tests, etc.
◈ The various controls and monitoring are facilitated due to the integrated options and software. Setting and recording of temperatures, pressures, humidity levels, etc. are possible, as are leakage and sterility controls
◈ The data collected will be useful during inspections by the regulatory authorities
◈ They are cheaper to maintain and service, and that means lower operating costs
More Details of Pharmaceutical Isolator
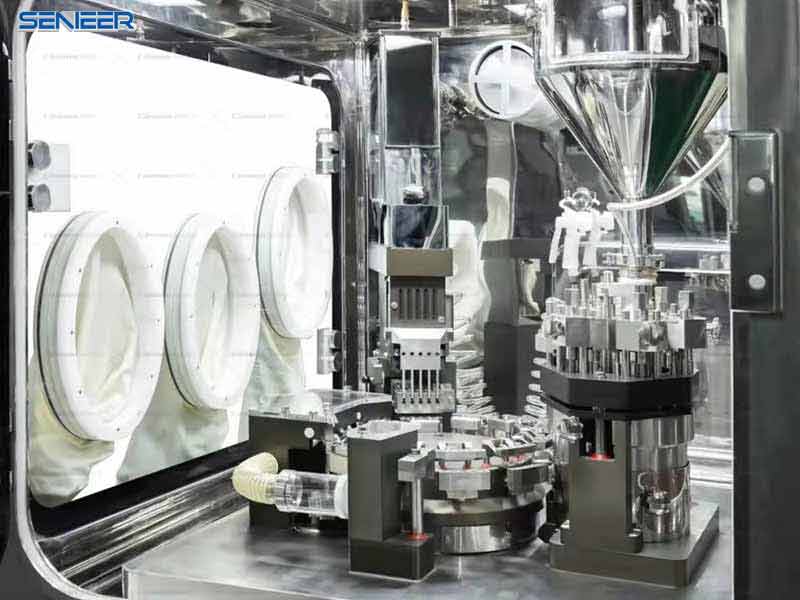
Containment Dispensing Isolator
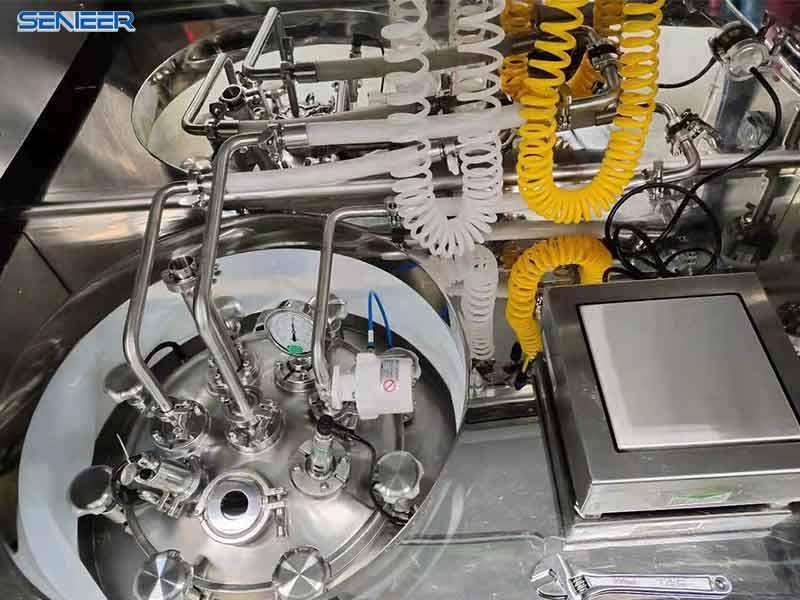
Laboratory Containment Isolator
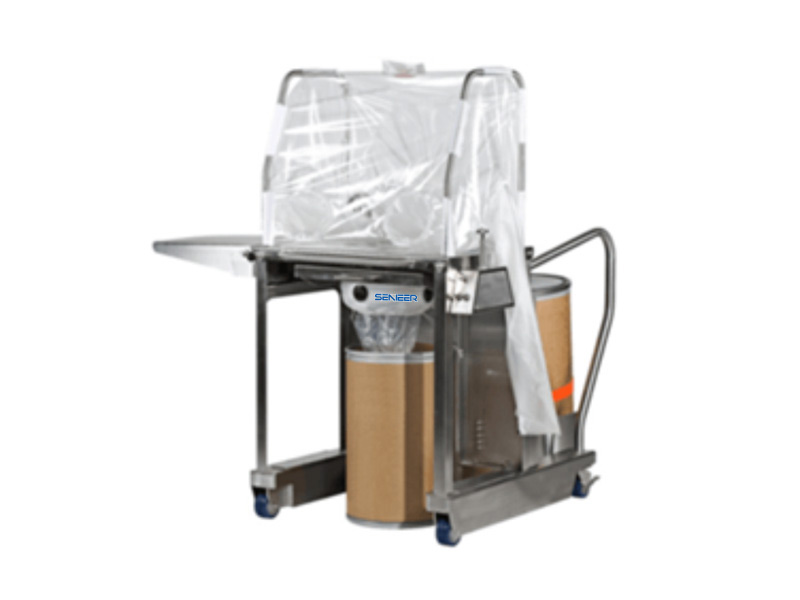
Flexible Film Isolator
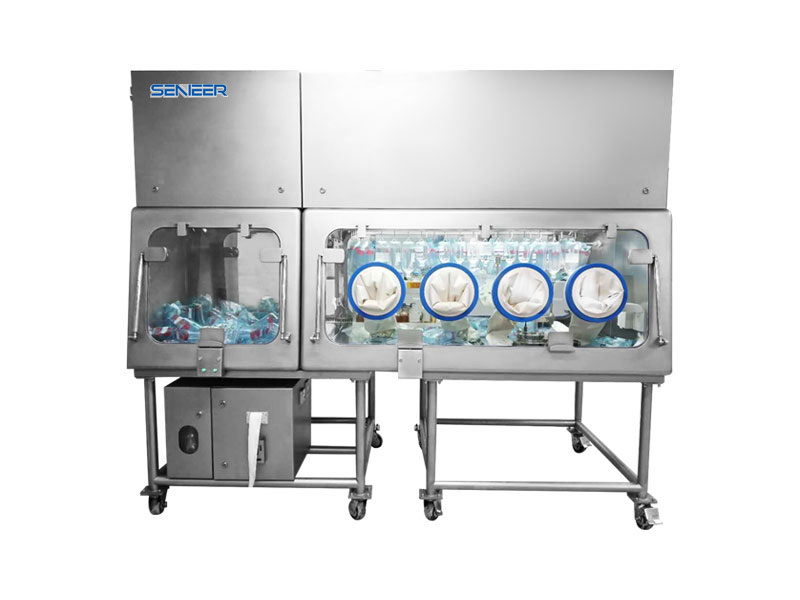
Sterility Testing Isolator/ Aseptic Filling Isolator
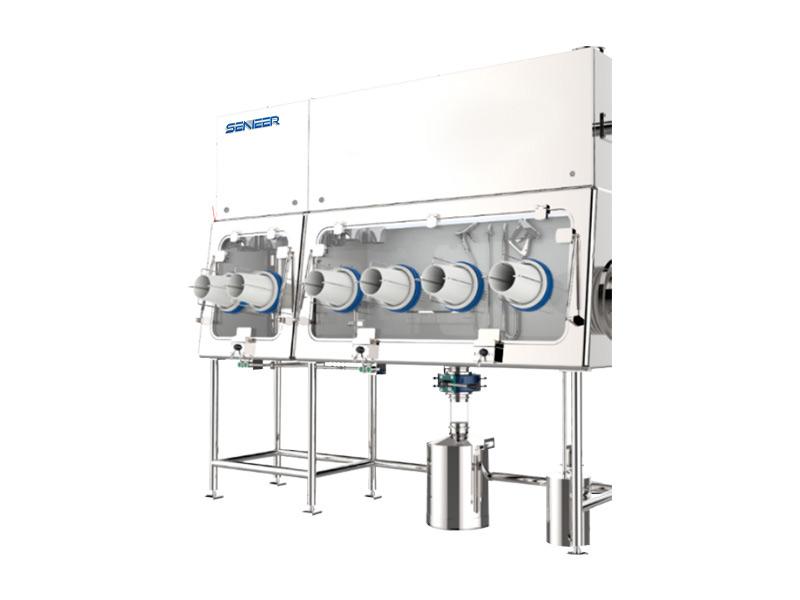
Weighing and Off-Loading Isolator
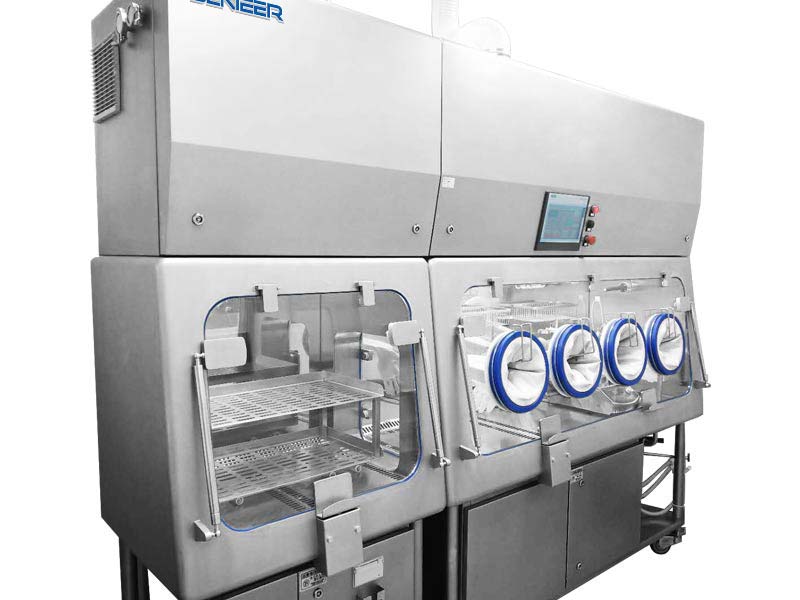
Weighing and Dispensing Isolator
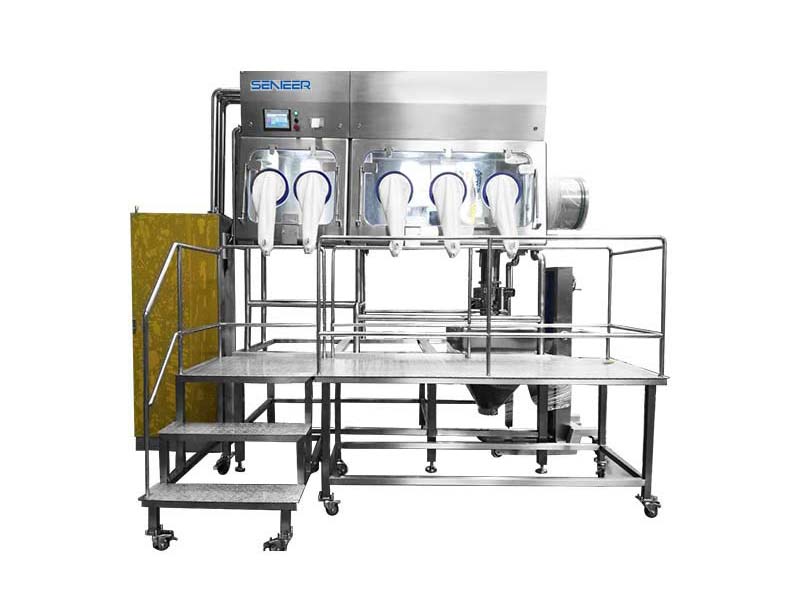
Isolators with Vacuum Dryer
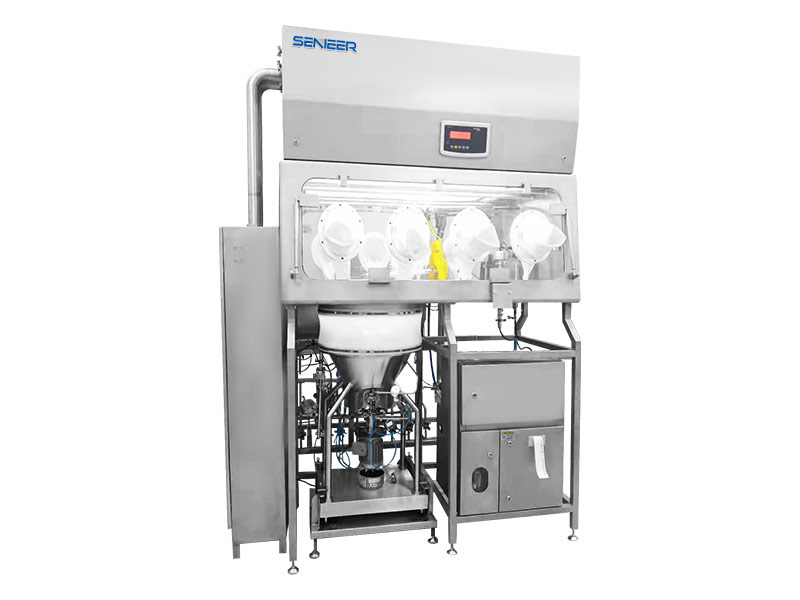
Isolated Lyophilizer Loading
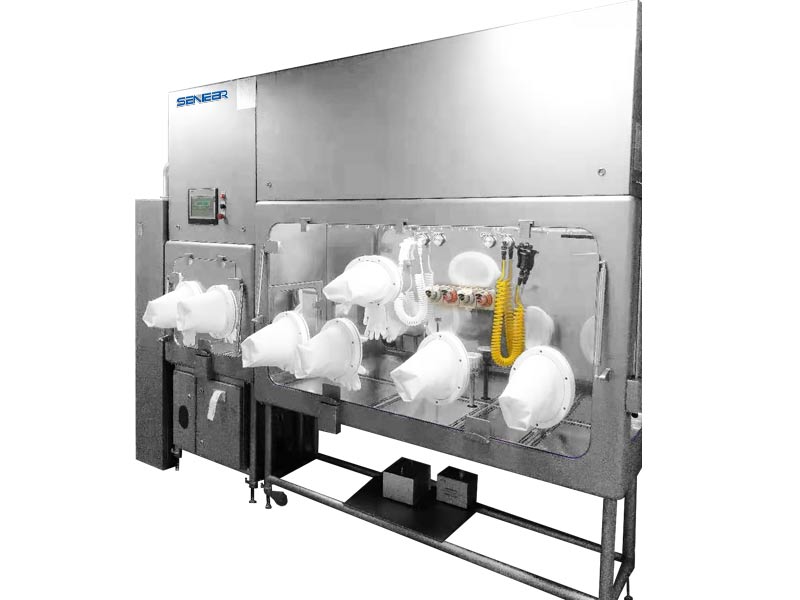
Micronising Containment Isolator
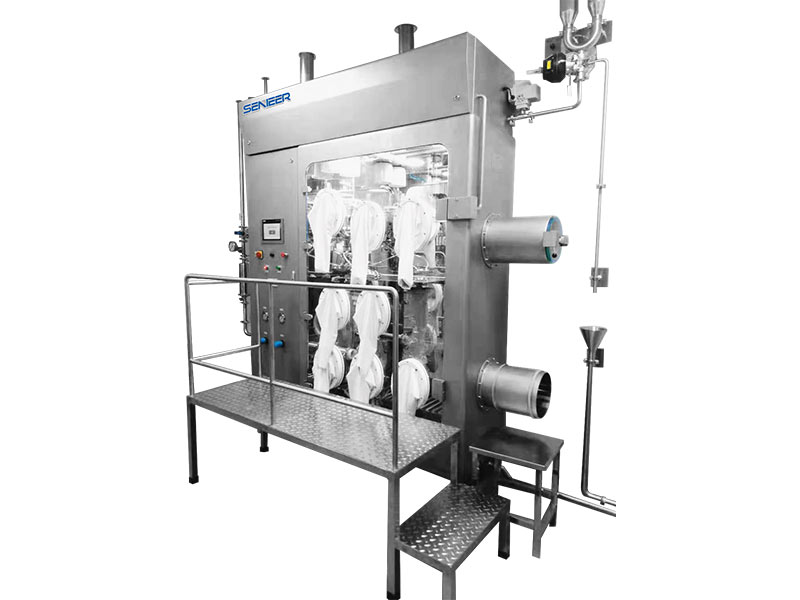
Glove Integrity Tester
Any Question About Senieer Pharmaceutical Isolator
Why Global Company Trust Senieer
Top Quality Factory Price
We have a quality control department to verify each product at different phases, from the procurement of parts to finished products
As Your Layout, Customize Machine
According to your layout, we can suggest the best capacity and type for you, customize pharmaceutical isolator for you
Pharmaceutical Isolator Consult & Design Service
Save energy resource for you, professional engineers can improve the best processing solution. We have the experience to help add a tremendous amount of value to your project
ISO.CE Standard Qualified
We successfully obtaining the ISO9001:2008 certificate and CE security management system certificate, this is significant for Senieer in building enterprise image
Pharmaceutical Isolator Training & Maintance Service
Free pharmaceutical isolator training & maintenance service for you, we will provide your team in-depth training on safe operation and pharmaceutical isolator maintenance
Pharmaceutical Isolator Installation Service
Senieer offers pharmaceutical isolator installation & commissioning service for production products, your pharmaceutical isolator and control systems are qualified based on the GAMP life-cycle
Pharmaceutical Bin Ultimate Buying Guide for Importers
In the synthesis of highly potent active pharmaceutical ingredients (HPAPIs) filtration and drying of the moist products is an important process step where isolators can be recommended for optimal workplace safety and full recovery of the expensive materials.
Many of the drugs handled in the isolators are designed to fight cancer cells and, as such, would be dangerous if they came into contact with a healthy individual. Therefore, the isolator’s role is paramount in the safe manufacture of such products.
To ensure that the products are manufactured with the correct background air, isolators require effective, corrosion-resistant ventilation of the process area. The isolators are designed to not only protect the operatives carrying out the task, but to also protect the substances within the chamber. The inbound air is highly filtered to provide a clean atmosphere and minimise the risk of contamination of the medicine or matter being tested.
Active Pharmaceutical Ingredients (API) have the prospect to bring about severe to serious health effects in personnel at very low airborne concentrations. The use of containment systems or equipment, as an integral part of an efficient method to potent compound safety, is recommended to control personnel exposure.
APIs can be classified into control bands based on their potency. Generally, APIs are categorized by occupational exposure limit (OEL) as a classification measure.
Chapter 1: Terms:
OEB – Occupational Exposure Band is a mechanism used to precisely assign chemicals into “categories” or “bands” based on their adverse health outcomes and potency considerations. It also aligns chemicals in groupings based on OEL in order to establish safe handling guidelines.
*Almost every facility has their own version
Chapter 2: Hazard Banding (OEB) Criteria:
These include qualitative, semi‐quantitative, and quantitative data for each toxicological endpoint.
▣ Acute toxicity
▣ Skin corrosion/irritation
▣ Serious eye damage/eye irritation
▣ Respiratory and skin sensitization
▣ Germ cell mutagenicity
▣ Carcinogenicity
▣ Specific target organ toxicity, both single and repeated exposure
▣ Reproductive toxicity
OEL – Occupational Exposure Limit is the airborne concentration of a compound to which nearly all workers can be repeatedly be exposed to for 8 hours a day, 40 hours a week, without adverse effects.
Exposure limits determine manufacturing safeguards | ||
Occupational Exposure Limit | Band | Production Requirements |
>1 – 10 mg/m3 | 1 | Good manufacturing safeguards |
>0.1 – 1 mg/m3 | 2 | Good manufacturing safeguards (with local exhaust ventilation) |
>0.01 – 0.1mg/m3 | 3 | Essentially no open handling (ventilated enclosures required) |
>0.001 – 0.01mg/m3 | 3+ | Virtually no open handling (containment systems required) |
≤0.001 mg/m3 | 4 | No open handling (closed systems required) |
≤0.001 mg/m3 | 5 | No manual operations/human intervention (robotics or remote operations required) |
Chapter 3: Each application must be assessed based on the following criteria:
▣ Product dustiness – the smaller the particle size the more likely it is the powder may get airborne.
▣ Type of product – if the product is cytotoxic/genotoxic and the requirement is in the 1-5 microgram range, consider full containment (isolator) unless the quantity/process is not practical for full isolation. If full isolation is not practical, operators should use additional protective equipment (full air fed suit) and the downflow booth room access must be via an airlock.
▣ The process – if the process imparts high energy to the powder, such as milling.
▣ The time taken to carry out the process – the longer the process time, the higher the potential risk of exposure.
▣ The quantity of powder handled at any one time – the higher the quantity, typically the higher the risk (bearing in mind the above, that is if the powder is granular i.e. sand like, the risk may not be that high).