For cleaning verification, what is important is Pharmaceutical Plant Equipment Cleaning Procedure, which is a major premise. Cleaning procedures are necessary before performing cleaning verification. Cleaning verification is to prove the applicability of the cleaning methods specified in the cleaning procedures. During the cleaning process of multi-variety collinear production equipment, it is proved that after the equipment has been cleaned, the potential residues of microorganisms and chemical components have been removed to an acceptable level.
The pharmaceutical equipment cleaning procedure describes the equipment and facilities, and the cleaning procedure for the containers is essentially the same as the process specification, which is a description of the process, and the cleaning procedure is a description of the cleaning process.
Before writing Pharmaceutical Plant Equipment Cleaning Procedure, we should have completed the development of plant facilities and equipment as well as cleaning processes. Laboratory research on cleaning methods for products to be cleaned is the determining factor to ensure the cleaning effect. Through the understanding of plant equipment and products, a reasonable design of cleaning parameters is carried out to ensure the expected cleaning effect. Before formulating the Pharmaceutical Plant Equipment Cleaning Procedure, we should have an understanding of the target cleaning material. We may classify products according to their characteristics, and the steps to define the design space for a cleaning process may be slightly different than the steps for defining the design space for a production process, since the design space for each production process is unique with respect to each specific process ( e.g. fluid bed granulation process).
However, many companies want to design a cleaning process for a specific set of equipment, and no matter what product is produced, this can be done by identifying worst-case contaminants and using those contaminants to define the design space for the cleaning process. But the question to consider at this point is that is there only one cleaning program for a piece of equipment? No, different products will use different cleaning agents and cleaning methods due to their different physical and chemical properties. We can use water to clean water-soluble products. For alcohol-soluble products, we can use ethanol and weak acid and alkali, etc., choose different cleaning agents according to the nature of the product to be cleaned. This requires grouping products using different cleaning agents, and then formulating their own cleaning procedures, and then selecting the worst varieties from each product group for cleaning verification to prove the applicability of the cleaning procedures.
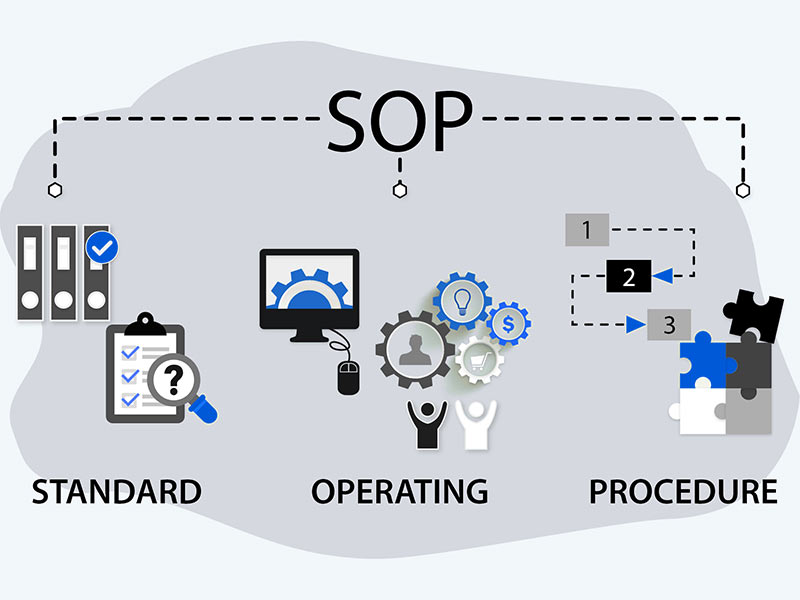
The preparation of cleaning procedures should specify the extent to which a piece of equipment needs to be disassembled. Most equipment, such as filling machines for large-volume injections, one-step granulators for solid preparations, and tablet presses, need to be disassembled to a certain extent before cleaning. The filling machine is almost completely disassembled. There should be written, clear and complete disassembly instructions, preferably with schematic diagrams, so that the operator can easily understand.
Pre-washing of cleaning steps: The purpose of pre-washing is to remove a large amount of (visible) residual product or material, creating a substantially consistent starting condition for subsequent cleaning.
Pre-washing is required, since cleaning procedures are often not dedicated and they need to be suitable for the generic equipment for production of a variety of products and concentration or dose specifications to simplify management and operation. The function of pre washing is to establish a relatively consistent starting point to improve the reproducibility of subsequent steps.
Requirements for pre-washing, the water quality used for pre-washing does not need to be strict, usually drinking water or drinking water that has been purified (such as filtered) by a certain procedure is sufficient. Use a water pipe or a hand-held high-pressure spray gun to rinse the equipment with fresh running water to remove residues. For large differences in the physical properties of the residue, a simpler and more practical approach is to have the operator check for visible residue and have them continue to spray the equipment until the visible residue disappears, which is the end point of the pre-washing. The judgment of the end point must be as clear as possible, especially the site to be examined. For example, it can be stipulated in the regulations that all surfaces of the machine are continuously sprayed with hot drinking water so that all visible residual particles disappear, paying particular attention to inspection of difficult-to-clean areas.
Establishment of cleaning parameters: operating parameters of cleaning procedures (such as type of cleaning agent, concentration, contact time, characteristics of residues, contamination conditions), also including characteristics of cleaning equipment, automated cleaning paths, sequence of cleaning environments, and the flow rate all need to be confirmed before being put into use. Each step of the cleaning procedure contains 4 parameters: TACT, which are time, action, concentration and temperature. These four parameters are interrelated and have a direct relationship to the success of each stage of the cleaning cycle, such as increased stain removal by heating the cleaning agent. Variables that are cleaning parameters need to be determined, and acceptable ranges for cleaning parameters are established as part of the cleaning program development effort.
The cleaning time is defined as the length of the cleaning step. In a cleaning step, it can be defined and measured in two ways: the direct method and the indirect method. The direct method can be used as a timer in the control system to measure the time. Time can also be measured by indirect methods, for example in the case of rinsing, sometimes by measuring volume instead of measuring time, since time can be determined by volume and flow rate. For final rinse water, it is common to add test requirements such as conductivity.
Action is defined as the fluid action of the cleaning agent. Such as soaking, washing, shock, turbulence. Agitation increases the effectiveness of the cleaner and the effectiveness of the cleaning process. Typical manual cleaning involves soaking and scrubbing to achieve a clean finish. Automated cleaning procedures typically employ impingement or turbulence as the cleaning action. The cleaning program needs to define the cleaning action. Flow rate is an important parameter for cleaning agents and wash water as they flow through equipment and should be specified and confirmed at each step of the cleaning process. The spray equipment should have maximum and minimum flow requirements, and the rinsing flow rate of the pipeline should ensure turbulent flow.
The concentration of the cleaning agent directly affects the success of the cleaning process. The chemical cleaning agent can be used in a concentrated form after dilution. The cleaning effect is related to the concentration of the cleaning agent. Using too little cleaning agent may not achieve the cleaning effect. If using too much cleaning agent, the residue from the cleaning agent may be difficult to remove and require a lot of rinsing. Generally, the method to achieve the best cleaning effect for alkaline cleaners can be to increase the temperature under stirring or prolong the time of turbulent leaching cycle.
Automated systems for cleaning agent addition must be reproducible. Regardless of the method of addition, confirming the cleaning agent concentration helps to demonstrate the consistency of the method. For automated cleaning programs, conductivity testing is the easiest way to test the concentration of strong base or strong acid cleaners. It should be possible to detect abnormal changes in cleaning agent concentration on-line through the chemical composition of the cleaning agent, for example some cleaning agent addition systems are controlled by volume and use conductivity testing as a confirmation method. When the conductivity exceeds the preset value, an alarm is issued, and the allowable range needs to be derived from the data developed by the cleaning program.
Temperature. The optimum temperature range for different steps in the cleaning procedure will vary, but the typical temperature of the initial cleaning agent is room temperature to maximize removal of denaturing or degradation products and to maximum product dilution. The cleaning agent is heated to enhance effectiveness, and the final rinse water is passed through high temperatures to speed drying rates and improve any process and the solubility of cleaning agent residues.
For the relevant contents of standard cleaning of equipment and facilities, it is recommended to specify the cleaning methods and contents of different types of equipment (online cleaning, cleaning station cleaning, containers, auxiliary equipment and facilities, etc.) and different frequencies (shift change, batch change, product change, special circumstances, etc.), and determine the cleaning standards and acceptance standards of each method.
When the equipment and facilities need to be disassembled during the cleaning process, the instructions, sequence, and method of disassembling and reinstalling each part should be clearly defined so that it can be cleaned properly. Make clear regulations on the concentration regulations, configuration requirements, application scope and reasons of cleaning agents and disinfectants used in equipment cleaning. For different cleaning methods and cleaning contents, it is recommended to specify the operation methods in detail according to the operation steps, including the essentials of action, the tools used, the cleaning agents and disinfectants used, and the standards to be met for cleaning, etc.
Provides recommendations for label status, expiration date, etc. before and after cleaning, including requirements for removing or erasing labels such as previous batch numbers. Identify the equipment contents and their cleaning status in an appropriate manner, specify the maximum time interval allowed between the end of the process and cleaning the equipment, the time the equipment can be left after cleaning, etc.
Make provisions on the storage and placement methods, environment, identification, validity period and other suggestions of the cleaned equipment, and make provisions on the temperature, humidity, cleaning grade and other suggestions of the storage environment. Make provisions for personnel and articles in the cleaning area, especially the flow direction and positioning requirements of articles in different cleaning States, so as to ensure the cleaning effect and prevent pollution, cross pollution and mixing.