Home » Pharmaceutical Roller Compactor
Pharmaceutical Roller Compactor
Senieer® Roller Compactor is specially designed for the pharmaceutical industry and features excellent compaction and granule forming technology to ensure that powders are uniformly and efficiently converted into granular finished products.
Introduction Of Pharmaceutical Roller Compactor
Pharmaceutical roller compactor is a device that compresses powder into flakes and then breaks it into granules and is mainly used for dry granulation in the pharmaceutical industry. Compared with wet granulation, dry granulation does not require the use of liquid solvents, avoids damage to moisture- and heat-sensitive materials, and is widely used.
Senieer pharmaceutical roller compactor series of pharmaceutical roller compactors, with their precise pressure control and excellent granulation performance, are the reliable choice for powder handling. This series of equipment is suitable for various scenarios from laboratories to industrial large-scale production, meeting different output and process requirements.
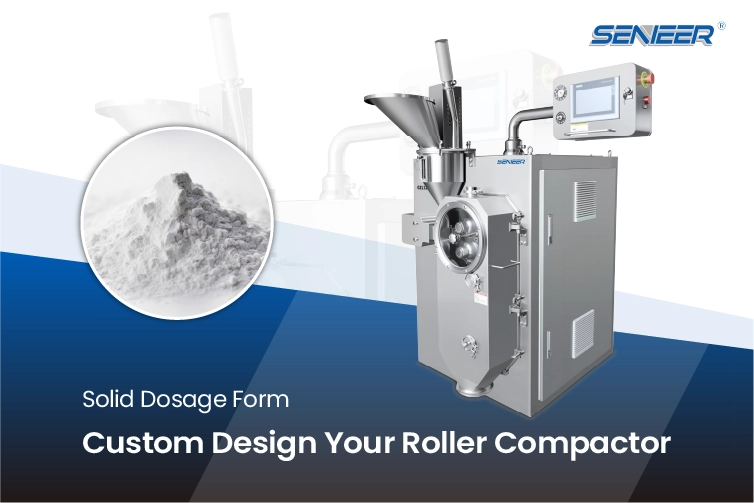
Different Types Of Pharmaceutical Roller Compactor
Different pharmaceutical roller compactor models are suitable for different production scales and application requirements. Typically, selection is based on production volume, particle size, and specific industry needs.
Choose Your Pharmaceutical Roller Compactor
Pharmaceutical roller compactor not only plays a vital role in the pharmaceutical field, but its efficient dry granulation process and precision control technology have made it widely used in many industries. Whether it is the production of food, chemicals, or agricultural products, pharmaceutical roller compactor s bring high-quality solutions to granule preparation in various industries.
Senieer range of pharmaceutical roller compactors are designed for the different needs of the pharmaceutical industry, from laboratory research and development to large-scale production, ensuring efficient and precise granule preparation at every production step. Whether you are looking for solutions for innovative process validation, or equipment for mass production, Senieer has a model to suit you.
Guidelines For Pharmaceutical Roller Compactor
This guide will comprehensively introduce the key elements of the pharmaceutical roller compactor, including its working principle, operating procedures, model selection and applications in different industries. Whether you are new to pelletizing equipment or looking for solutions to optimize production, this guide will provide you with the core information you need to gain insight into how to improve production efficiency and product quality with the pharmaceutical roller compactor.
Introdution
Pharmaceutical roller compactor is a device that compresses powdery materials into flakes or granules through mechanical extrusion. It is widely used in pharmaceutical, food, chemical and other industries. It adopts a dry granulation process without adding liquid solvents or heat treatment, and is suitable for processing moisture-sensitive and heat-sensitive materials. The pharmaceutical roller compactor can improve the fluidity and density of the material, ensure the quality of the granules, and help users achieve efficient and precise tableting or filling in the subsequent production process.
How Does Pharmaceutical Roller Compactor Work?
The working principle of the pharmaceutical roller compactor is based on the physical processes of extrusion and granulation. The equipment compresses powdered materials into sheets through two rotating rollers, and then converts the sheets into granules through crushing and granulation devices. Its core principle is to use mechanical pressure to reduce the void ratio between powders to form dense particles, which are easier to store, transport and process.
1.Feeding system: Through the screw feeding system, the material is continuously and evenly fed between the rollers.
2. Compaction process: Two rotating rollers apply high pressure to compress the powdery material into dense flakes. The speed and pressure of these rollers can be adjusted to suit different materials and process requirements.
3.Crushing and screening: The pressed flake materials are crushed through the crushing device, and then passed through the screening system to obtain particles of the required size. Oversized particles are returned to the system for re-compaction.
This process does not require the participation of water or solvents, avoiding stability problems that may occur during wet granulation. It is especially suitable for processing moisture-sensitive or heat-sensitive materials.
Model selection Of Pharmaceutical Roller Compactor
Different pharmaceutical roller compactor models are suitable for different production scales and application requirements. Typically, selection is based on production volume, particle size, and specific industry needs.
1.Experimental type: suitable for small batch testing and new product development. It is usually small in size, easy to operate, and suitable for use in R&D laboratories.
Small: Suitable for small-scale production and pilot testing, small in size but capable of mass production, suitable for small-batch customization.
2.Medium size: Suitable for medium-scale production, capable of meeting medium-volume production requirements, and often used in routine production in the pharmaceutical and chemical industries.
3.Large: Designed for large-scale industrial production, suitable for high output and large-scale production, especially suitable for the continuous production needs of pharmaceutical, food and other industries.
Applications
pharmaceutical roller compactor plays a vital role in several industries, especially in the pharmaceutical, chemical, food and metallurgical fields. With efficient dry granulation technology, it can compress powdered materials into uniform particles, which not only enhances the operability of the materials, but also improves the stability and consistency of the product.
pharmaceutical industry
In the pharmaceutical industry, pharmaceutical roller compactor is a key equipment for dry granulation and is widely used in the production of tablets and capsules. This equipment can compact drug powder into stable particles, effectively improve the uniformity and fluidity of the particles, and ensure the dosage consistency of the drug.
- Tablet production: Roller granulation technology can effectively control the size and density of drug particles, so that tablets have ideal dissolution speed and bioavailability. Through roller granulation, the fillers and active pharmaceutical ingredients required for tablets can be more evenly distributed, thereby avoiding the problem of uneven dosage.
- Capsule filling: The granules prepared by pharmaceutical roller compactor have good fluidity, enabling precise capsule filling, avoiding material waste, and reducing the risk of capsule shell rupture.
- Moisture-sensitive drugs: Compared with wet granulation, roller granulation does not require the use of water or solvents. It is suitable for the granulation of moisture-sensitive and heat-sensitive drugs, ensuring the stability and activity of drug ingredients.
chemical industry
In the chemical industry, pharmaceutical roller compactor is used for particle preparation of a variety of chemical products, especially chemical products that require high material stability and finished product consistency, such as catalysts, fertilizers, pigments, and detergents. This equipment helps chemical companies improve production efficiency and ensure the physical properties and chemical stability of products.
- Catalyst production: Catalysts require strict particle size and shape requirements. Particles prepared by pharmaceutical roller compactor can achieve uniform specific surface area and pore structure, thereby improving catalyst activity and reaction efficiency.
- Fertilizer granules: Powdered fertilizer raw materials are made into granules through dry granulation, which is convenient for packaging, transportation and storage. Compared with wet granulation, roll granulation avoids the introduction of moisture, avoids subsequent drying steps, and saves energy.
- Pigments and dyes: The granular pigments produced by roller granulation can be more evenly dispersed in application materials and are not easily lost during storage and transportation, ensuring product quality.
Food industry
In the food industry, pharmaceutical roller compactor is mainly used to process powdery or poorly fluid food raw materials into particles to enhance the processing performance, storage and eating convenience of food. Typical applications include:
- Nutritional powders and additives: Many food nutrition powders, condiments and additives are in powder form. These powders can be made into granules through roller granulation, which reduces dust flying and improves fluidity, making them easier to handle during mixing and packaging. .
- Dairy products and plant protein powder: Used for granulation of milk powder, soy milk powder and other products. After being granulated by the pharmaceutical roller compactor, the product has better fluidity and is less likely to clump during packaging, extending the shelf life of the product.
- Condiments and spices: Making powdered spices into granules can improve the dispersion and stability of spices, reduce agglomeration during storage, and ensure the stability of flavor.
Combination Equipment
1.Vacuum feeder: Used to automatically transport powder to the feeding system of the pharmaceutical roller compactor to ensure the continuity and stability of material supply and reduce manual operation and contamination risks.
2.Crusher: When the granulated flake materials need to be further crushed into uniform particles, the crusher is an indispensable auxiliary equipment to ensure that the final particle size meets the standard.
3.Screening machine: After compaction and crushing, the particles need to be sorted and graded by the screening machine to obtain the required particle size. Screening machines help ensure the uniformity and quality of the final product.
4.Dust removal device: In order to keep the production environment clean, the dust removal device can be used in conjunction to reduce dust generated during the production process and ensure safe operation and the service life of the equipment.
Choose Your Interested Production Line
Bottle Filling Line
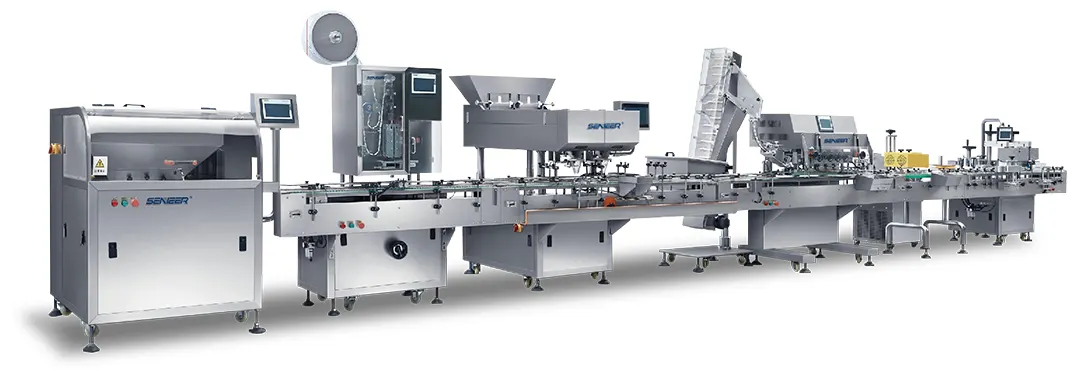
Granulation Line
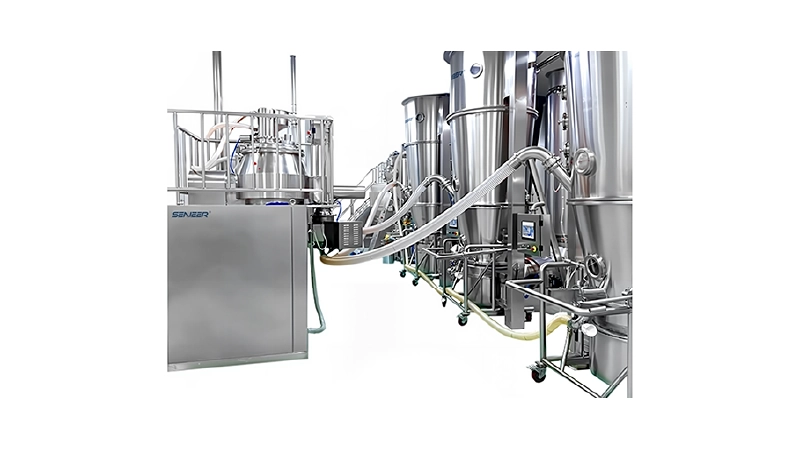
Blister Packaging Line
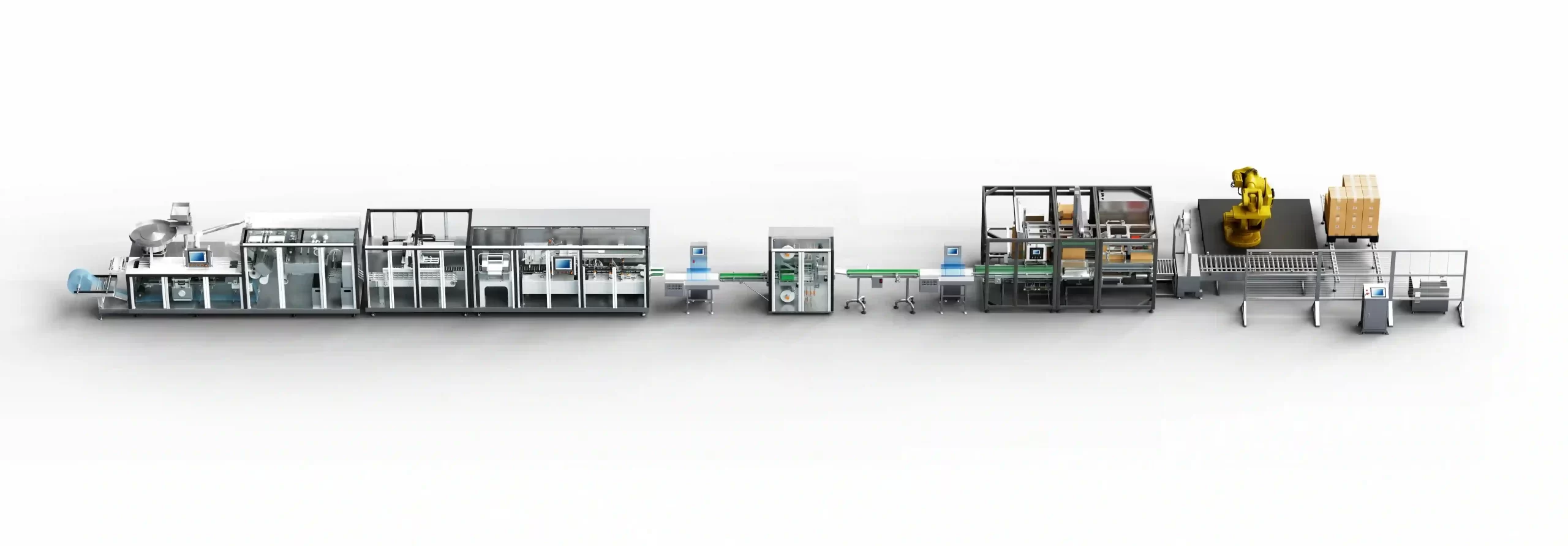
Powder Filling Line
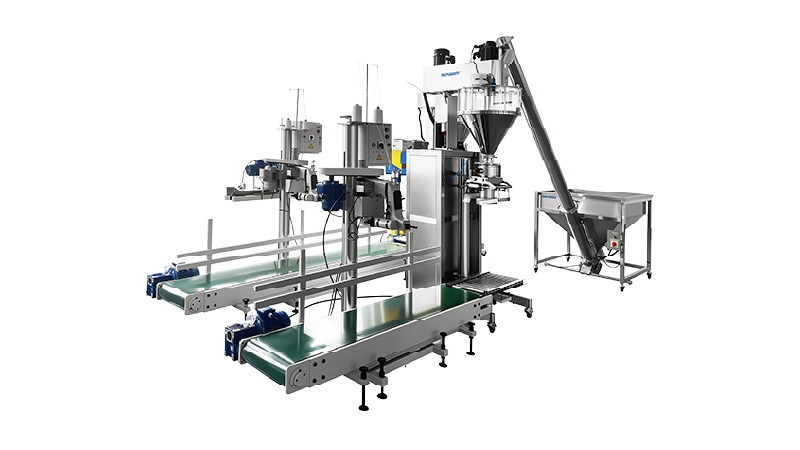