At present, the purified water system of most pharmaceutical companies adopts the traditional pretreatment process – ultrafiltration (UF) as the purified water pretreatment process, which has been favored by some pharmaceutical companies. With a dosage of 10 t/h, the initial investment, operation cost and effluent quality of ultrafiltration have advantages over traditional processes. This article discusses the pretreatment ultrafiltration process of purified water for pharmaceutical production, but the use of ultrafiltration to reduce endotoxin in purified water after treatment in purified water equipment (EDI) is not within the scope of this article.
1 Introduction To Ultrafiltration Membrane And Process
1.1 Introduction To Ultrafiltration Process
The traditional pharmaceutical softened water system includes multi-media filter, softener and activated carbon treatment, which can be used as the post-treatment process of purified water to prepare raw water. The ultrafiltration process can completely replace the multi-media filter, and its effluent quality completely exceeds that of the multi-media filter, which greatly reduces the burden of the subsequent water treatment process.
A complete ultrafiltration water treatment system generally consists of a pretreatment part, an ultrafiltration membrane device part and an auxiliary equipment part (such as backwashing, gas scrubbing and in-situ chemical cleaning equipment). The ultrafiltration system can remove impurities such as suspended solids, colloidal particles, bacteria, and most viruses and macromolecular organic matter in water. Depending on the requirements of the industry, in order to meet the quality requirements of the final product water, subsequent treatment steps are sometimes required, such as nanofiltration (NF) and reverse osmosis (RO) or ion exchange resin for desalination.
The ultrafiltration membrane device itself includes: ultrafiltration membrane components, feed water pump for ultrafiltration system, backwash pump and gas scrubbing compressed air system to restore ultrafiltration membrane filtration performance, self-cleaning filters, instruments, pipes and valves, etc. Ultrafiltration system design should also include in-situ chemical cleaning equipment for regular chemical cleaning of ultrafiltration membranes.
According to the type of raw water or the fluctuation of the quality of the ultrafiltration influent, other pretreatment techniques can also be used before ultrafiltration, such as coagulation/flocculation, clarification/sedimentation, air flotation or particle media filtration, etc. The quality of the raw water reaches the ultrafiltration influent standard If not, the above pre-processing is not required, and only a pre-filter is required.
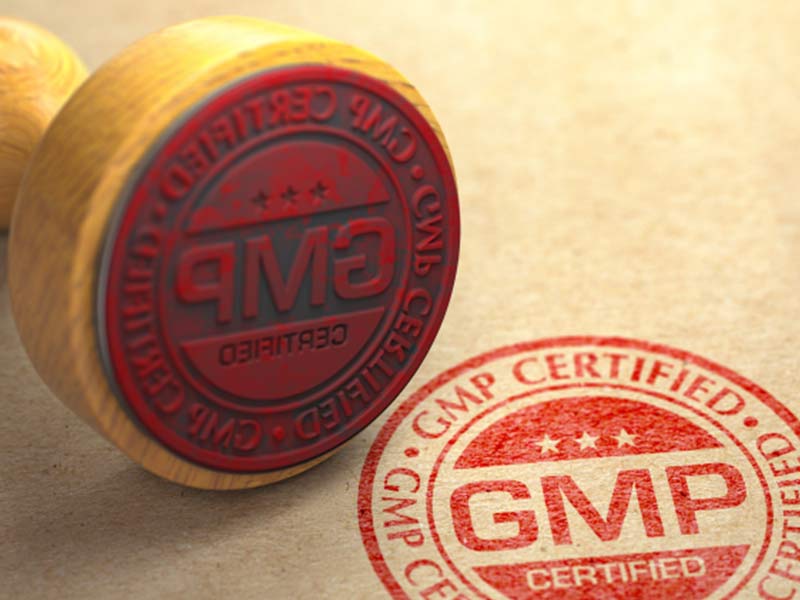
The ultrafiltration process is a water treatment technology with higher filtration precision. It has the characteristics of anti-pollution, less chemical dosage, high water recovery rate and small footprint. It is an ideal choice for the pretreatment process of reverse osmosis systems.
1.2 Performance Characteristics Of Ultrafiltration Membranes
Ultrafiltration membrane modules are made of high-strength, hollow fiber membranes, which have the following advantages:
- The nominal pore size is 0.03 μm, which can effectively filter particles such as bacteria, viruses and colloids to protect the reverse osmosis membrane, etc.
- PVDF polymeric hollow fiber has high strength and good chemical resistance, which can prolong the service life of the membrane.
- Hydrophilic fiber membrane, easy to clean, good wettability, helps to maintain long-term stability of performance.
- External pressure design allows solids with larger particle size to enter, which can reduce the requirements for pretreatment process.
- U-PVC housing eliminates the need for costly pressure vessels.
The hollow ultrafiltration membrane is shown in Figure 1, and its related parameters are:
- Structural parameters: the nominal membrane pore size is about 0.03 μm; the nominal cutting molecular weight MWCO is about 150 000 dal; the filtration method is external pressure type or internal pressure type.
- Membrane material: polyvinylidene fluoride (PVDF) or hydrophilic polyethersulfone (PES): Usually, the chemical stability of modified PVDF is better than that of PES in terms of resistance to oxidants.
The performance parameters are as follows:
- Product turbidity ≤ 0.1 NTU; > 2 µm particle removal > 4 log; bacterial removal > 4 log; Sludge Density Index (SDI) ≤ 2.5.
The operating parameters are referenced as follows:
- Filtration flux@25℃40~120 l/m2/hr; pH value during operation is 2~11; temperature is 1~40℃; maximum NaOCl tolerance concentration is 2 000 mg/l; degrees) is 300 NTU.
1.3 Operating Conditions Of Ultrafiltration Membrane Modules
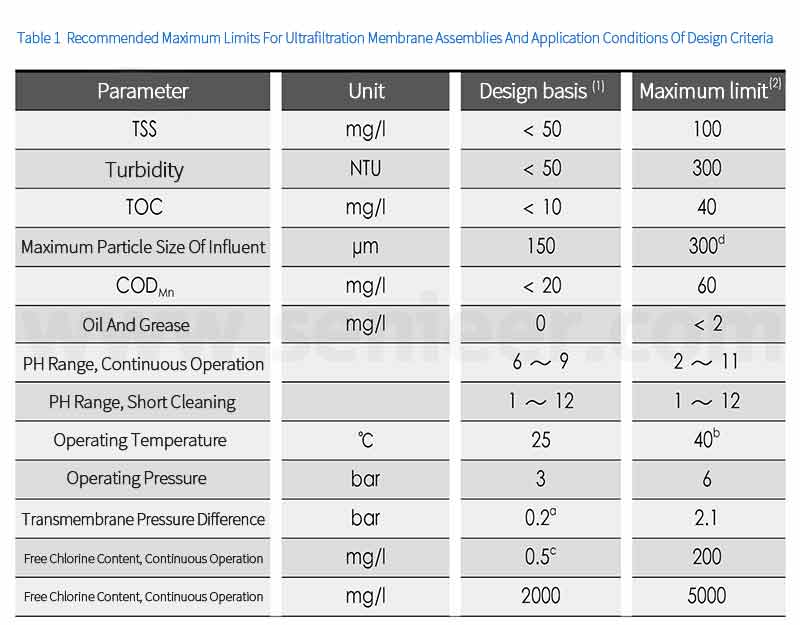
1.4 Ultrafiltration Membrane Running Sequence
Ultrafiltration membranes usually use full-flow filtration mode, which greatly saves operating energy consumption. Since its operation is controlled by keeping the permeate flow constant (ie, constant flow), the transmembrane pressure difference (TMP) of the ultrafiltration membrane will continue to increase as the filtration process proceeds. This requires a gas scrubbing auxiliary backwash every time interval to control the increase of TMP. The solid particles trapped on the surface of the membrane filaments are removed by regular gas scrubbing assisted by backwashing. This backwashing does not need to add any chemical cleaning agent. Solid contaminants are removed during regular gas scrubbing assisted backwashing, thus avoiding their deposition on the filament surface. The pollutants that are adsorbed on the surface of the membrane and cannot be removed by backwashing can be removed by on-line chemically enhanced backwashing. In the process of chemically enhanced backwashing, a small amount of chemicals are added to the backwash water, and after a short period of immersion (usually 5-10 minutes), the chemicals are discharged, and the ultrafiltration membrane can be restored to its original state. In addition, regular in-situ chemical cleaning (CIP) of the ultrafiltration membrane system is required to thoroughly remove contaminants and restore ultrafiltration membrane performance. CIP agents can be sodium hydroxide, sodium hypochlorite, hydrochloric acid, citric acid, etc. The operation of the ultrafiltration membrane system mainly includes several steps: filtration, gas scrubbing, bottom drainage, upper backwash, lower backwash, positive wash, chemically enhanced backwash and in-situ chemical cleaning.
2 PW process Flow And Discussion
The pre-treatment process and post-treatment process can refer to the schematic diagram of the purified water preparation process, as shown in Figure 2.
2.1 Cleaning And Disinfection
Since the membrane flux will be attenuated when solid substances accumulate on the membrane, the membrane module can recover the flux by periodic and frequent backwashing. The membrane itself has the characteristics of good chemical stability, pollution resistance, residual chlorine resistance and chemical cleaning resistance, which can meet the needs of chemical cleaning and chemically enhanced backwashing.
Because the activated carbon treatment process is usually not configured in the ultrafiltration process, the entire purified water pretreatment is in a state of residual chlorine (Figure 3). Ultrafiltration cannot be pasteurized, because the hollow ultrafiltration membrane is not resistant to high temperature, so chemical disinfection is required.
2.2 Removal Of Residual Chlorine
Residual chlorine must be removed before entering reverse osmosis (RO) membranes because RO membranes are not tolerant of residual chlorine. Ultraviolet (UV) method will be used to remove residual chlorine in the ultrafiltration process. The ultraviolet intensity can be calculated and checked by the residual chlorine meter to check whether it meets the standard. If the residual chlorine does not meet the standard, it will be supplemented by dosing (NaHSO3), so the process of activated carbon treatment is no longer used. After the activated carbon removes residual chlorine, it is easier to breed microorganisms, but it is undeniable that it also has the effect of removing odor and organic matter. Total organic carbon (TOC) content can be reduced by effectively removing tiny particles, colloids, bacteria, viruses and removing macromolecular organic matter.
2.3 Softener Settings
The traditional softener is still installed after the ultrafiltration process. The setting of the softener can reduce the hardness of the water, which is beneficial to better protect the reverse osmosis membrane, and adopts the same method of thermal disinfection as the traditional process, which is also a safer practice. At present, there are also processes that do not use a softener, but use a descaling agent. Its chemical composition and residues need further observation. Currently, it is not recommended to introduce more chemical substances.
2.4 Other Design Considerations
The two-channel ultrafiltration design can use 50% of the load at the same time. When one ultrafiltration channel needs to be cleaned, replaced or the membrane is damaged, the other ultrafiltration channel can also be operated alone to achieve production guarantee. Of course, through the online integrity test and transmembrane differential pressure monitoring, the redundant design of one ultrafiltration can find the damaged membrane, close the valves at both ends of the damaged membrane, and use other undamaged membranes to achieve the required capacity and the purpose of designing risk controls.
In the two-stage RO, the first-stage RO uses a non-high-temperature-resistant membrane as the pretreatment, and the second-stage RO membrane and EDI are the post-treatment processes, which is also an idea, so that the non-high-temperature-resistant RO can be used to reduce the membrane cost. Even if only the first stage RO and EDI are used in the post-processing, it will not violate the requirements of GMP. The post-processing section still uses high-temperature RO and EDI to maintain the ability to pasteurize (Figure 4). Therefore, there is no risk of violating regulations by setting the first stage RO in the pretreatment.
The post-processing process is still recommended to be carried out by traditional RO and EDI methods, which will not be repeated in this article.
Concluding Remarks
At present, the ultrafiltration process is not widely used in the pharmaceutical industry as a pretreatment for the preparation of purified water. Most companies still use the traditional pretreatment process for purified water. The reason is that the ultrafiltration process is used as a pretreatment for the preparation of purified water. The cost is slightly higher than that of the traditional multi-media filter, and it is only possible to achieve a balance of input costs in factories with higher water treatment volumes. In addition, engineers are accustomed to traditional processes and are reluctant to make new attempts, worrying about process risks, or not fully understanding the ultrafiltration process and the risk control methods of the overall process design. The effluent quality of the ultrafiltration process is significantly better than that of the traditional multi-media filter, which also reduces the pressure of the subsequent process and ensures the quality of purified water or water for injection. The maintenance of the ultrafiltration process is relatively easy. The backwashing is carried out automatically and continuously, and chemical cleaning is carried out according to the transmembrane pressure difference and the degree of production capacity decline. The ultrafiltration membrane can be replaced in about 3 to 5 years. Membrane technology is also constantly developing. At present, the mainstream pharmaceutical water purification machine suppliers have mature ultrafiltration pretreatment processes, and new projects of domestic pharmaceutical companies have been put into use one after another.