Solid Dosage Forms: Intelligent Turnkey Solution
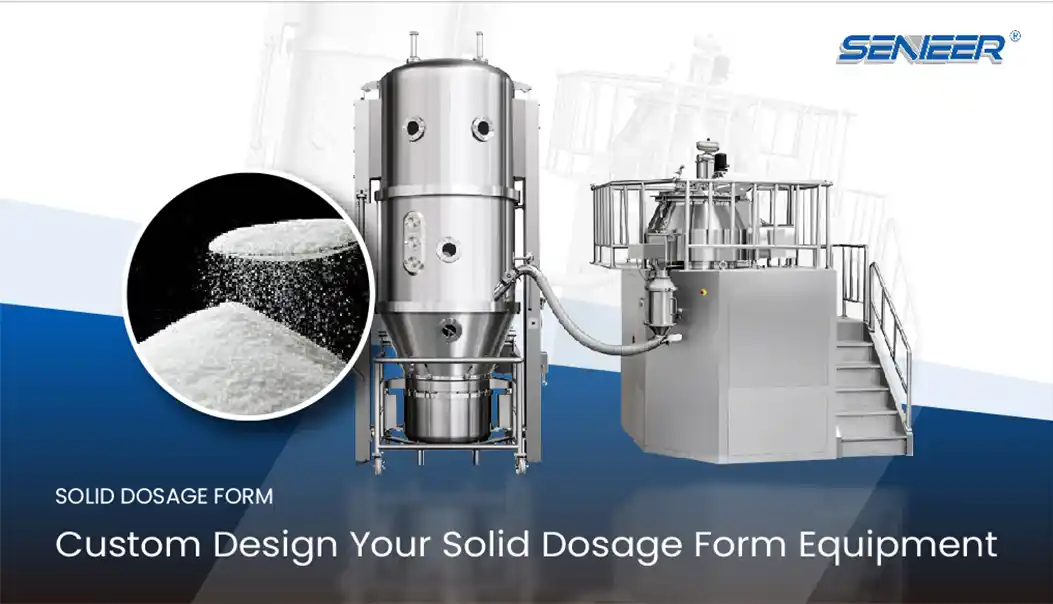
Solid Dosage Forms
Senieer Pharmaceutical Equipment Turnkey Solution: Driving Innovation with Technology, Defining New Production Standards
In the precise chain of the pharmaceutical industry, the enhancement of efficiency in each link is crucial to the core competitiveness of enterprises. Senieer, with its deep expertise in the pharmaceutical equipment field, utilizing core equipment such as fluidized beds, granulators, and coating machines as core points. Relying on its comprehensive turnkey service , it pushes the synergistic efficiency of cost, quality, efficiency, labor productivity, and safety to the extreme.
Features Of Senieer Turnkey Solution
- We are well aware of the essence of lean production — controlling the loss rate from the source..
- In the quality dimension, Senieer implements the concept of “zero compromise” throughout the entire lifecycle of the equipment..
- The art of balancing efficiency and safety is the core expression of Senieer technology..
- With mature experience as the foundation and technological innovation as the engine.
Browse Chapter
Chapter 1: Senieer Solid Dosage Forms Turnkey Projects?
Chapter 2: Rapid Mixer Granulator
Chapter 3: Fluid Bed Processor
Chapter 4: Dry Cone Mill
Chapter 5: Vacuum Conveying With Cone Mill
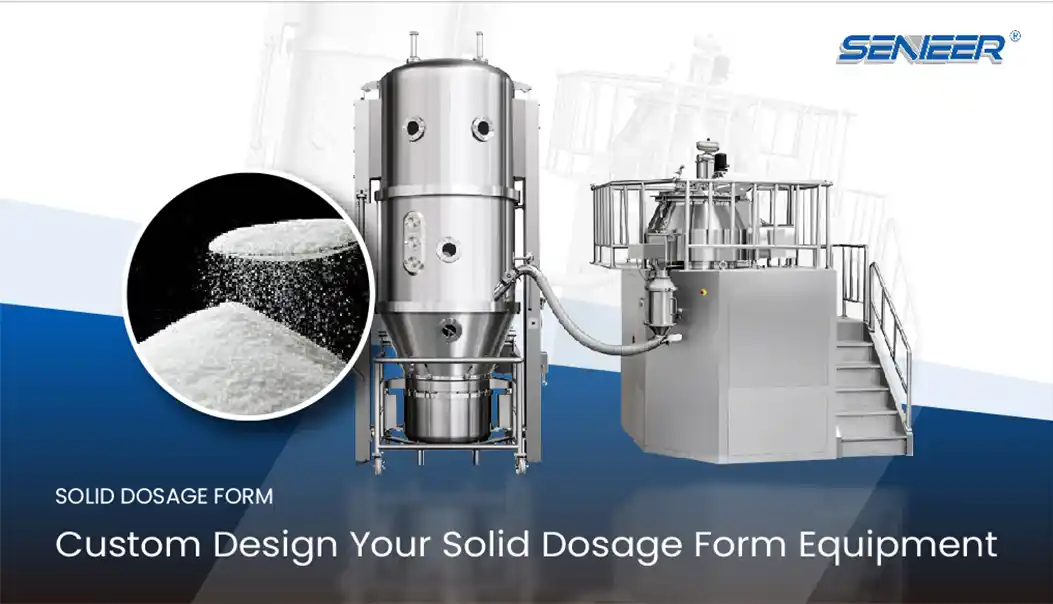
Chapter 1: Senieer Solid Dosage Forms Turnkey Projects?
We deeply understand the essence of lean production — controlling loss rates from the source.
Based on the high-precision mechanical structure and electrical control system of Senieer equipment, from raw material feeding to the critical processes of granulation and coating, through the millimeter-level positioning accuracy of the servo drive system, closed-loop feedback mechanisms, and redundant fault-tolerant design, we achieve full control over the material flow process. The unique modular structure reduces mechanical clearances and residues, combined with multi-level sensors for real-time calibration of process parameters, ensuring that the loss rate is strictly controlled at industry-leading levels, allowing every gram of raw material to be fully utilized.
In terms of quality, Senieer implements the “zero compromise” philosophy throughout the entire lifecycle of the equipment:
from 316L stainless steel material compliant with GMP certification, to the closed-loop control system for micro-environment temperature and humidity, to the millimeter-level precision calibration of process parameters, we safeguard the consistency of pharmaceuticals with stringent quality control logic.
The art of balancing efficiency and safety is the core expression of Senieer technology.
Automated production units can reduce human dependency by more than 40%, while through explosion-proof design, intelligent early warning, and redundant safety mechanisms, we build a production environment of “human-machine isolation, risk preemption.”
Choosing Senieer is choosing a sense of certainty.
With mature experience as the foundation and technological innovation as the engine, we provide reliable solutions for global pharmaceutical companies, from single machines to complete lines, from design to delivery, turning every investment into quantifiable competitive advantages.
Chapter 2: Rapid Mixer Granulator
The rapid mixer granulator is a key equipment that integrates the functions of mixing, wetting, and granulation. Its core advantage lies in improving the flowability, uniformity, and compressibility of powders through the wet granulation process, thereby enhancing the quality of the final product.
Advantages:
1. High quality of granules
- Uniformity: Stirring and shearing forces ensure the even distribution of binders, resulting in consistent particle size.
- Good flowability: Spherical or quasi-spherical particles reduce powder飞扬, improving the efficiency of subsequent tabletting or packaging.
- Excellent compressibility: Moderate porosity of particles enhances the shaping and hardness during tabletting.
2. High process integration
- Integrated operation: Mixing, granulation, and reducing the risk of material transfer contamination.
- Shorter time: Compared to traditional wet granulation methods (such as oscillating granulation), efficiency is increased by 30%-50%.
3. Strong adaptability
- Flexible formulation: Capable of handling powders with different properties (such as hygroscopic, viscous materials).
- Adjustable parameters: Precise control of particle density and size by adjusting the stirring speed, binder amount, and granulation time.
4. Compliance with industry standards
- GMP compatible: Airtight design reduces cross-contamination, easy to clean and sterilize, suitable for the pharmaceutical industry.
- Low dust: The wet granulation process suppresses dust, improves the operating environment, and ensures personnel health.
5. Energy-saving and environmental protection
- Less binder usage: High shearing force makes liquid dispersion more efficient, reducing solvent waste.
- Controllable wastewater: A closed system reduces waste liquid discharge, lowering environmental pressure.
6. Wide application fields
- Pharmaceutical: Preparation of granules for tablets and capsules; granulation of traditional Chinese medicine extracts.
- Food: Granulation of instant beverages and seasonings.
- Chemical: Shaping of catalysts and fertilizer granules.
Chapter 3: Fluid Bed Processor
The fluid bed processor is a versatile equipment that integrates material drying, top spray granulation, bottom spray coating, and cut spray pellet coating processes into one, widely used in various fields such as chemical, pharmaceutical, food, environmental protection, and energy. Its core advantage lies in its multifunctionality, adapting to different production process requirements, significantly enhancing efficiency, flexibility, and cost-effectiveness.
Advantages:
– High efficiency in drying with uniform temperature distribution;
– Multifunctional integration, reducing equipment investment and floor space;
– Easy control of process parameters, high level of automation;
– Energy-saving and environmentally friendly, easy maintenance.
Chapter 4: Dry Cone Mill
Dry cone mill is a device that integrates functions of raw material separation, pre-pressure conveying, roller pressing, and extrusion granulation.
Advantages
- High one-time product yield
- Simple process, large production batch
- Horizontal feeding is continuous, uniform, with high conveying efficiency and precision
- High control accuracy, high degree of automation
- Good sealing performance, easy to clean and maintain
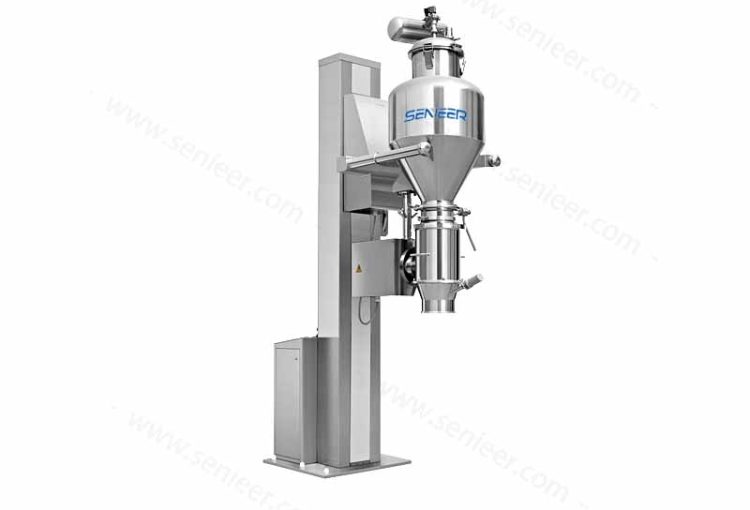
Chapter 5: Vacuum Conveying With Cone Mill
Vacuum conveying with cone mill is a device that combines material conveying and granulating functions, mainly used in pharmaceutical, food, chemical, and other industries, capable of efficiently completing material transfer and particle optimization processing in a closed environment.
Working Principle
Vacuum conveying with cone mill uses a vacuum negative pressure system to suck materials from the raw material hopper into the interior of the equipment. Subsequently, the materials enter the granulating chamber, where the particle size is adjusted through the extrusion and cutting action between the granulating blades and the screen mesh, and ultimately the conveying is completed through the discharge system. The specific process includes:
- Vacuum Suction: Utilizing the negative pressure generated by the vacuum pump, powdered or granular materials are sucked into the buffer hopper.
- Granulating Treatment: After the materials enter the granulating chamber, the particle size is adjusted by extruding and breaking through the adjustment of the distance between the granulating blades and the screen mesh, ensuring uniform particles.
- Discharge Conveying: The granulated materials are conveyed to the next process through a closed pipeline or hopper, preventing dust leakage.
Main Advantages
- Sealed and dust-free, meeting GMP standards.
- Efficient integration of granulating and conveying.
- Automated operation, reducing labor costs.
- Flexible adaptation to different material characteristics.
- Easy maintenance and cleaning.
Choose Your Interested Production Line
Bottle Filling Line
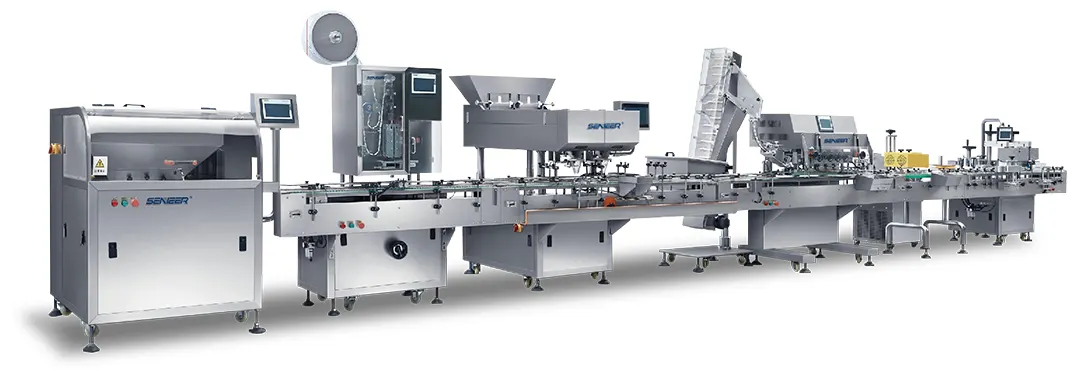
Granulation Line
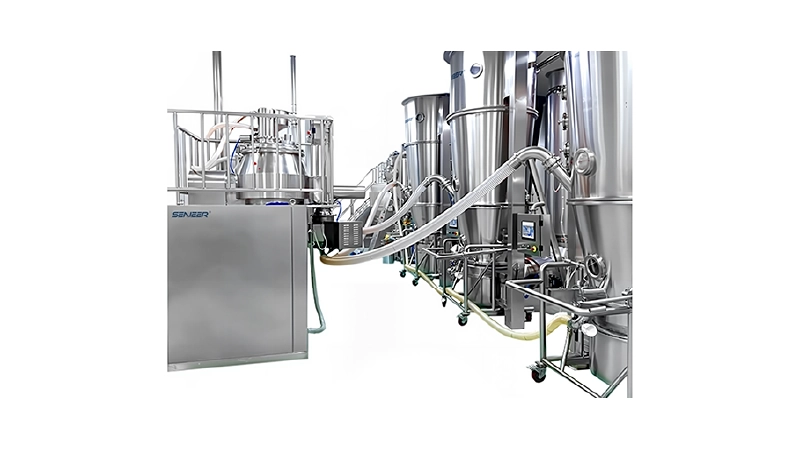
Blister Packaging Line
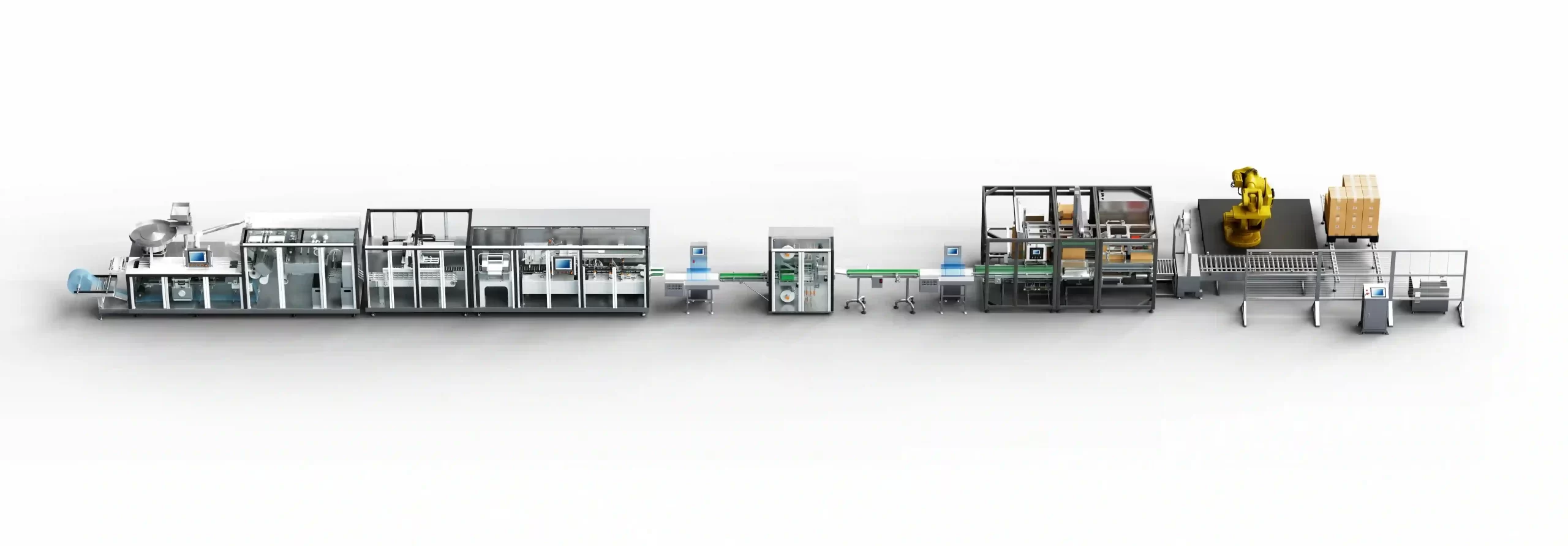
Powder Filling Line
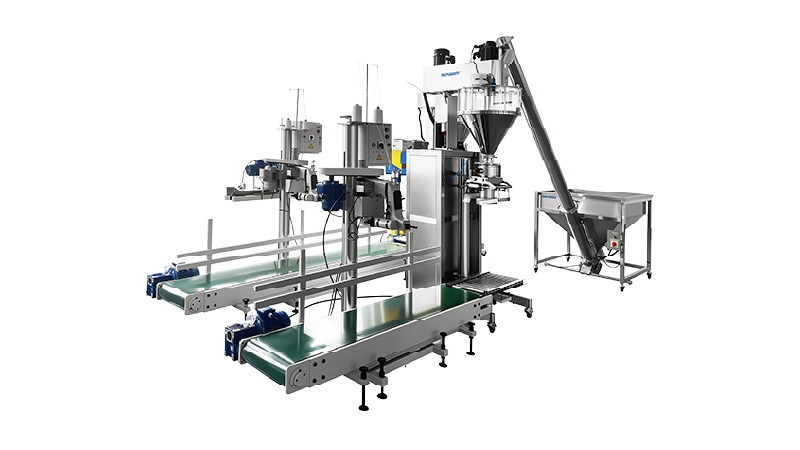