In this article we will be dealing with Key Equipment And Technology For The Production Of Oral Solid Dosage Forms
Batching Equipment
1.Automatic Batching Weighing System
Ingredients are an indispensable key link in the production of many solid dosage forms, and the accuracy of ingredients has an important impact on the quality of products. In the past, manual weighing, manual batching and feeding of pharmaceutical ingredients were often used. During the batching process, dust was flying, causing environmental pollution, affecting the health of personnel, and low batching efficiency. With the continuous development of information technology and automatic control technology, the batching system for oral solid dosage form is bound to develop in the direction of informatization and intelligence.
The Automatic batching and weighing system for solid dosage form has the following characteristics:
◇The production process is completely closed, no dust leakage, reducing material loss, avoiding polluting materials, protecting the environment and personal safety, and the noise meets environmental protection requirements;
◇WIP function and quick installation structure, easy to operate, maintain and clean;
◇Production instruction and formula review function to avoid human error;
◇Anti-error function, the correct material can be identified when feeding;
◇It can realize the weighing ratio of various materials, and automatically generate batching records;
◇The production process can prevent wrong feeding and human operation errors;
◇High-performance actuators, high measurement accuracy;
◇ Can be connected to MES system.
2.Continuous Quantitative Feeding Mixing Feeder in Oral Solid Dosage forms formation process
The continuous quantitative feeding mixing feeder is the main feeding method for the continuous production of oral solid dosage forms preparations. It is mainly used to add raw and auxiliary materials into the continuous production system. It consists of a feeding unit and a continuous mixing unit. The feeding unit generally adopts loss-in-weight control, and the continuous mixing unit continuously mixes the raw and auxiliary materials to make the API and auxiliary materials evenly distributed.
The feeding unit is composed of a hopper, an anti-bridge mechanism, a conveying screw, a weighing system and a controller. In production, the hopper, material and conveying screw are jointly and continuously weighed. As the material is delivered, the actual weight loss rate is measured and compared to the desired weight loss rate (setpoint). The loss-in-weight feeding unit automatically corrects the deviation from the set point by adjusting the conveying screw speed, so as to continuously feed the material evenly and accurately. The continuous mixing unit has an in-line mixing uniformity measuring device to ensure higher mixing uniformity.
-
Granulator
1.Twin Screw Granulator
The twin screw granulator is an ideal tool for continuous granulation as it can be conveyed, mixed, wetted and sheared in the same machine in a very short time. The twin-screw granulator was originally converted from a twin-screw extruder, and its structure is basically the same as that of the twin-screw extruder, mainly including: transmission, feeding device, barrel, screw, head, pulping device and other parts , and the most significant difference from the extruder is that it does not require a die. In addition, the barrels are generally split to meet the cleanliness specifications required by GMP in pharmaceutical production.
The residence time distribution (RTD) of the material in the twin-screw granulator is an important parameter to characterize the performance of the granulator. Understanding RTD and its influencing factors is very important for continuous granulation and its control.
The twin screw granulator is also an efficient mixer. The flow of material in the granulator is similar to that of a continuous mixer. Different kneading and mixing screw elements can extend the material residence time (RTD) and create axial mixing in the process. Therefore, in some cases, the raw and auxiliary materials do not pass through the continuous mixer, and can directly enter the twin-screw continuous granulator in proportion to complete the mixing. Figure 34 presents a schematic diagram of a twin screw granulator.
Figure 1 – Schematic Diagram Of Twin-Screw Granulator
2. Continuous Mixing And Granulation Technology
A typical system has three modules: wet high shear granulation module, segment dryer module and particle conditioning module. In the granulation module, the dry ingredients are individually or premixed into a continuous high shear granulator. After dry mixing, the granulation liquid is added so that each granule receives the same amount of liquid. The entire wet granulation process takes place in seconds, with only a few grams of product in process at a given time, resulting in faster start-up and minimal losses. Particle size can be adjusted by changing the working level in the granulator, which results in a continuous flow of wet granules with constant mass and density transfer to the dryer without oversized agglomerates.
3. Hot Melt Extrusion Technology (HME)
Hot Melt Extrusion (HME) is a continuous process that uses an extruder to uniformly disperse API in a polymer-based carrier. Under the action of mechanical force and external heating of the barrel, the material is first melted, and then distributed, dispersed and mixed, so that the API and various auxiliary materials are evenly dispersed in the carrier, and then the degraded small molecules and water are further removed from the material. Finally, the material is extruded from the head by the extruder screw. After the material is extruded from the extruder, it can be cooled and shaped by air cooling, water cooling, cooling roller, etc., and finally crushed, diced or rolled according to the needs of the medicine. The application of hot melt extrusion technology in the pharmaceutical field mainly includes: improving the solubility and bioavailability of drugs, preparing slow-release or delayed-release preparations, preparing position-release preparations, parenteral depots and local drug delivery systems, and masking API bad taste.
Hot melt extrusion technology has the advantages of continuous process, fewer process steps, high repeatability, solvent-free, online monitoring, small footprint, and easy scale-up. It is the mainstream granulation technology in the current continuous production technology of solid forms, FDA is now strongly encouraging the continuous production process of HME, and many foreign pharmaceutical companies have also participated in it and carried out related research and applications. Its core technology is the research on the process parameters of different drugs, the design and manufacturing technology of extrusion screw, etc.
Combining the advantages of traditional Chinese medicine research in China, applying HME technology to the field of traditional Chinese medicine to improve the controllability and compliance of traditional Chinese medicine preparations will open up a wider market. Hot melt extrusion granulation technology combines many advantages of solid dosage form technology and mechanical preparation to achieve dust-free, continuous operation, good reproducibility and extremely high production efficiency. This technology can not only promote the dissolution of poorly soluble active ingredients to improve their bioavailability, but also be used to delay the dissolution of water-soluble active ingredients to prepare slow-release or enteric-coated preparations; in addition, it can also be used to prepare taste-masked pellets or other Special shaped preparations, such as films, sticks, etc. Since the entire extrusion process lasts for a short time and does not require the addition of water or organic solvents, heat drying is not required.
The technical characteristics of hot melt extrusion are as follows:
◇Continuous process;
◇The final product can be formed at one time;
◇There is no organic solvent problem in the process (safety, saving, environmental protection);
◇No solvent residue in the product;
◇No surfactant is required, and plasticizer is rarely used;
◇Improve the bioavailability of poorly soluble drugs;
◇Adapting process analysis instrument (PAT) can realize process design (QbD);
◇ Novel dosage forms (new dosage forms for implanted administration, direct extrusion transdermal absorption products, co-extruded sustained-release products).
Hot melt extrusion granulation equipment can be divided into plunger type and screw type. The plunger type is gradually eliminated due to its poor mixing ability. Screw extruders are divided into single-screw, twin-screw and multi-screw, and the first two are currently the most widely used in the field of formulation. Both single-screw and twin-screw extruders are composed of feeding system, transmission system, screw and barrel system, heating and cooling system, die system, monitoring system and downstream auxiliary processing system. The single-screw extruder adopts an integral structure and consists of three parts: feeding section, melting section and metering section.
Compared with single-screw extruders, twin-screw extruders have more advantages:
◇The average residence time of materials is short. The distribution range of residence time is narrow, generally between 1min and 10min;
◇Under the action of high shear and kneading force, the mixing effect of materials is better;
◇The two screws mesh with each other and scrape each other, which has a high self-cleaning ability and reduces the waste of materials;
◇The operating parameters are highly controllable, and the extrusion and mixing processes can be continuously operated. The screws of each section can be arbitrarily matched, with flexible and changeable characteristics, and the die can also be arbitrarily changed according to the shape;
◇Enhanced mixing ability, distributive mixing and dispersive mixing are intertwined, making the mixing of drug and carrier material more uniform.
Since the mechanical structure of the screw and barrel of the common extruder used in the food industry or chemical industry is relatively complex, how to disassemble and clean the screw and barrel of the extruder to meet the requirements of GMP is also a hot melt. A major difficulty in the application of extrusion technology in the pharmaceutical industry. Modular twin-screw extruders are currently considered to be the most suitable hot melt extrusion equipment for the pharmaceutical industry, as shown in Figure:
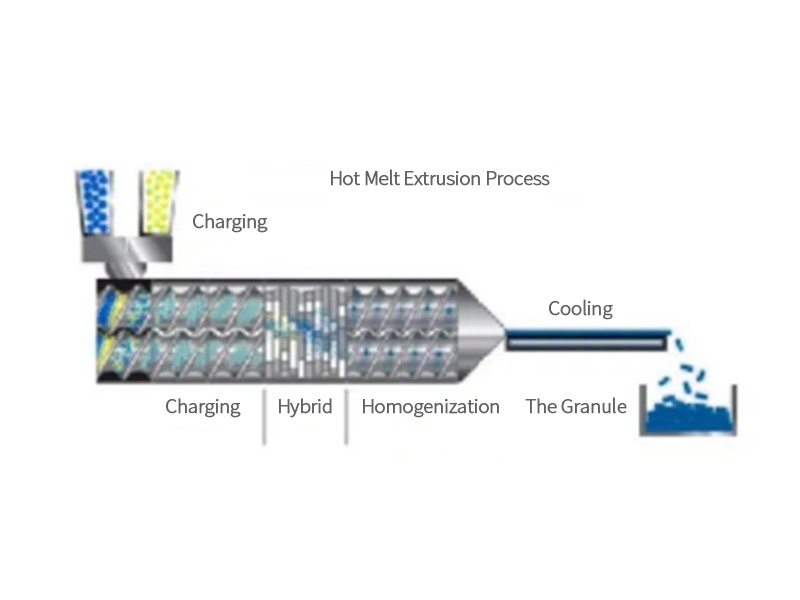
Figure 2 – Schematic Diagram Of Hot Melt Extrusion
As can be seen in Figure 35, the modular screw combination can replace different screw components, which are mainly divided into conveying section and mixing section. The conveying section mainly plays the role of conveying the material forward, and cooperates with the barrel to heat the material to melt the polymer: the mixing section is responsible for uniformly mixing and distributing the main components such as API into the molten polymer, by increasing or decreasing the number of mixing sections or adjusting the angle combination between the mixing sections can effectively adjust the mixing shear force to suit different recipes and processes. Therefore, the combination of screws is an important process parameter in the hot melt extrusion process.
In the process of hot melt extrusion, API and carrier and various auxiliary materials are first continuously fed into the extruder in a quantitative manner by means of a volumetric single-screw or twin-screw feeder. These raw materials have a variety of shapes and flow characteristics, and accurate and reproducible metering of the raw materials as they are fed is important to the hot melt extrusion process. In order to ensure the accuracy of feeding, a feeder with weighing feedback is often used to monitor the rate of weight loss during the feeding process in real time, and to realize feedback control of the speed of the feeding screw to achieve uniform and accurate continuous feeding. In addition, for different materials, it is sometimes necessary to select or design different screws.
After feeding, under the action of the mechanical force of the extruder and the heat outside the barrel, the material is first melted, and then distributed and mixed to make the API and various auxiliary materials evenly dispersed in the carrier, and the next step will degrade the matefluid rial. Small molecules and moisture are removed from the material, and finally the material is extruded from the head by the extruder screw. In the whole mixing extrusion process, due to the different melting points of various materials, the barrel temperature should be accurately detected and controlled in stages. In addition, because the rheological properties of each polymer are different, the screw is often required to be modularly designed and replaced to meet different product process requirements. The API-dispersed polymer is extruded at the end of the extruder by means of an extrusion die, which can have different designs to make the dosage form expected for downstream solid dosage form production. Some common dosage forms that use hot melt extrusion include film models (such as transdermal patches and oral dissolution therapy), co-extrusion models (co-extrusions that form landfill contraceptives and subcutaneous controlled release formulations), extrusion models. A spheronization model (to form a segment, which is convenient for spheronization).
After the material is extruded from the extruder, it can be cooled and shaped by air cooling, water cooling, cooling roller, etc., and finally pulverized, diced or rolled according to the needs of the drug to obtain the prepared target shape, as shown in Figure 3:
Figure 3 – Hot Melt Extrusion Process Route
Some new dosage forms produced by hot melt extrusion have been widely used clinically, and some common drugs include Zoladex, vildagliptin, guanidine metformate, olaparib, and suvorexan.
4. Single-Pot Granulation Technology
Mixing, granulation and drying are done in the same equipment, often referred to as “one-pot granulation” (or “one-pot granulation”). A single pot granulator is essentially a high shear granulator enhanced with various integrated drying options. The basic drying principle is to reduce the evaporation temperature of the granulation liquid by using vacuum in the pot, use a jacketed pot for heating, and introduce a small amount of gas at the bottom of the pot to pass through the product bed to improve the drying efficiency. However, the same limitation exists for “pure” vacuum drying, since the heated wall is the only source of drying energy. Microwave drying can be used to overcome these limitations, providing a more efficient drying method that also allows more binder fluids and water-based particles to be effectively dried. For the use of organic solvents, vacuum and microwave drying offer distinct advantages in waste gas treatment, requiring only pure organic vapors, unlike most other wet granulation techniques which require a mixture of solvent and bulk process gas.
5. Multi-Chamber Fluidized Bed Continuous Drying Technology
The dryer module is based on the fluid bed drying principle, dividing the continuous flow of particles into small portions and drying them in a separate drying chamber of a multi-chamber fluid bed dryer. When the content reaches the desired moisture level, it is emptied and transferred to the granulation module and refilled with fresh wet granules. The drying profile of each drying chamber is monitored. In the Particle Sizing module, dry granules can be measured for key quality attributes such as particle size distribution, moisture and content uniformity. At any one time, only a few kilograms are processed, which will minimize the amount of risky product. The unit’s small size and modular construction allow for quick deployment and easy installation.
-
Tableting Machine
1. High Airtight Grade Tablet Press
See the application of foreign high airtight technology.
2. Powder Direct Compression Technology
At present, more than 40% of foreign tablet varieties have been produced by this process, while domestic direct powder compression is still in its infancy, and most domestic tablet production still uses the traditional granulation and tableting process.
Compared with traditional granulation and tableting, the advantages of direct compression of whole powder are as follows:
◇The technological process is relatively simple, and there is no need to go through the processes of wetting, bonding, granulation, drying and granulation, and the production efficiency is high and energy is saved.
◇The quality of the finished product is stable, and it is suitable for drugs that are easily discolored or decomposed when exposed to humidity or heat. The obtained tablet has a smooth surface, a short disintegration time limit, less content drop and high stability.
◇Due to the few processes and short time, the chance of cross-contamination is reduced, and it is not exposed to moisture and is not easily contaminated by microorganisms, which meets the requirements of GMP.
Combined with the research on the fluidity, compressibility and lubricity of powder, it focuses on breakthroughs in key technologies such as powder fluidity and compressibility, tablet weight accuracy, tablet hardness, and production capacity during direct powder compression, and solves traditional tableting problems. In the production process, the process is complicated, the process is long, the loss of raw materials is large, the production efficiency is low, the energy consumption is high and the risk of cross-contamination is high. The new technology and tableting equipment of all-powder direct compression will improve my country’s tablet preparation technology.
3. Pellets Tableting Technology
Using conventional tablet presses for pellet compression presents significant challenges in terms of process yield, productivity, and batch content uniformity due to the tendency for pellet segregation in the blend.
To address the above problems, GEA’s MUPS technology provides a solution: two weight-reducing screw feeders are installed above the tablet press, one for pellets and the other for premixed excipients. Both the pellets and excipients are continuously fed into a conical mixer fitted with a ribbon paddle above the tablet press, which mixes the two streams into a unified formulation. Because the filling volume in the mixer determines the mixing time, the filling volume of the mixer should be accurately controlled. Pellets may separate if the distributor and mixer are connected directly. In order to avoid this, GEA developed a special valve to control the amount of material entering the distributor, and at the same time optimized the design of the distributor’s base plate and paddle wheel to avoid separation and damage of the pellets.
5. Directly Connected Torque Transmission
At present, the main drive of domestic tablet presses are all driven by ordinary AC motors through belt accelerators and reducers, which have low transmission efficiency, serious heat generation and large torque loss. The Senieer Compacting Press adopts a direct-connected torque transmission as shown in Figure 37, which has the following advantages:
◇No need for gearbox anymore;
◇No drive belt adjustment/replacement, no drive belt flexibility;
◇No gearbox lubrication, no gearbox backlash, simplified mechanical installation;
◇No need for expensive maintenance work;
◇Energy cost can be saved up to 50%;
◇Especially suitable for large torque torch drive;
◇Can be perfectly matched with all other products;
◇The tablet press runs smoothly.
Figure 4 -Direct-Connect Torque Transmission For Senieer Compacting Presses
5. Replaceable Template Technology
The technology of changing table of tablet presses has matured in domestic and foreign manufacturers. In recent years, GEA have respectively launched tablet presses with replaceable template technology. Segmented replaceable template technology has the following features and advantages:
(1) Simplified Structure
◇No middle mold.
◇There is no need to fix the bolts and threaded holes of the middle mold.
(2) The Output Is Greatly Increased, And The Product Loss Is Significantly Reduced
◇With the same pitch circle diameter, the number of punches is increased, and the output is increased by 40%.
◇The surface of the middle platen is smooth, there is no gap between the middle mould and the middle plate, the scraper slides on a smoother surface, and the product loss can be reduced by more than 50% (see Figure 39, Figure 40).
(3) Product Switching Is Significantly Accelerated
◇ Shorter replacement time, save up to 88% time per product switch.
Take 2090ⅰ as an example, loosen and remove 36 bolts, and remove 36 middle molds with a total of 72 parts. Now loosen the 6 clamping wedges and 6 bolts and remove the 3 die table segment middle templates (see Figure 41). Time-consuming adjustments to the dies and punches are no longer required for special form tablets.
◇The cleaning time is shorter:
——Fewer parts and therefore less cleaning;
——Without the gap between the middle mold and the middle plate;
——There is no middle die hole, no middle die fixing bolt hole, and the surface that needs to be cleaned is significantly reduced;
——The cleaning work is greatly reduced.
Figure 5 – Traditional Medium Template Figure 6 – Segment Can Be Replaced In The Template
Figure 7 -Senieer Segmented Replaceable Middle Plate Without Middle Mould And Fixing Bolts
6. Special Tablet Press Die
Senieer increases throughput and tablet quality through specially designed dies. Figure 42 shows the special die FS12 of FITE, which can increase the production capacity by 40%. Figure 43 shows a special die FS19 from Senieer Compacting with a 30% longer compression dwell time.
7. 3D Printed Tablet
At present, the drug that has been approved by the FDA and produced through continuous production technology using 3D printing technology is Levetiracetam tablets from Aprecia Pharmaceuticals. Especially when the patient needs to take a large dose of the drug at one time.
-
Coating machine
1. Continuous Coating Technology
(1) DRIACONTI-T Continuous Coating Machine From DRIAM Company In Germany
The structure of the coating machine is shown in Figure 44 and Figure 45. The interior of the coating pot is divided into several small compartments. The tablet cores in each compartment are in different coating stages and are independent of each other. According to the setting, it enters the first coating room quantitatively, and the prepared coating medium is sent to the spray gun or dropper through the peristaltic pump, and is automatically sprayed on the surface of the tablet core or pill, and is continuously supplied by the hot air blower. The heated clean hot air is introduced from the mesh on the upper part of the drum, and the hot air passes through the gap between the chips in the moving state, passes through the mesh in the lower part of the drum, and is discharged by the exhaust fan after dust removal. The clean hot air dries the coating medium sprayed on the surface of the tablet cores quickly and uniformly, so that the surface of the tablet cores can quickly form a firm, dense, flat and smooth film coating. It can enter different compartments in sequence according to the control requirements, and the spray devices in different compartments can automatically supply air and liquid according to the settings of the operator. After passing through all compartments, the tablet cores achieve the intended film coating.
Figure 8 -Internal Structure Of Driaconti-T Pharma Coater
(2) Canada O’HARA Company Continuous Coating Machine
The world’s first continuous coating machine is a continuous film coating machine model HVCC-3015 launched by O’Hara Technologies, Canada (see Figure 9).
Figure 9 -Continuous film coater for HVCC-3015
This machine is suitable for batch production and continuous production mode with different output requirements. The gun’s automatic sequencing system and additional control mechanisms ensure that all tablets are uniformly coated and bright in color, minimizing potential drug loss. The continuous coater is equipped with 28 spray guns, which are divided into 5 independent control sections: the discharge end is equipped with a pneumatically controlled weir, which is located lower and when it is raised, controls the flow of tablets to the discharge mouth speed. In addition to the skid bars, the movement of the tablets in the coating pan is only controlled by the tablet feed rate and the height of the weir plate. This control mechanism is an improvement on the continuous coating technology, and another difference is that There are no baffles inside, as shown in Figure 10.
Figure 10 -Coating Pan
The equipment has several patents, including automatic loading and unloading, controllable bed depth and start-up and shutdown procedures. The startup and shutdown procedures are said to reduce the amount of tablet waste by about 80% compared to other continuous coating equipment. Startup and shutdown procedures typically include:
◇Fill the coater with enough product to start the first spray;
◇As the tablet gradually flows to the bottom of the machine, turn on each spray gun in turn;
◇ Once the coater is loaded, the operation goes into continuous mode;
◇When the feeding stops, use the sensor to start the shutdown procedure;
◇Once the shutdown procedure is started, stop all product discharges until it is completed.
The continuous process increases throughput because in batch production, time is spent on filling, tablet preheating, end-of-process drying, cooling, and unloading. When clear film coatings are used for low weight gain requirements (1% to 2%), the continuous process can save a lot of time. However, large weight gain is required for color film coating, which is a challenge for continuous film coating technology. In this case, it would be necessary to pass the product through the coater twice to achieve the desired increment, which would halve the throughput. For example, the continuous film coating machine produced by some enterprises, although the nominal output is close to 1000kgh, but its actual output is not much different from the traditional batch production process because of the two passes through the coating machine. HVCC-3015 type coating machine only needs one pass, the output is 1000kg/h ~ 1200kg/h, and the weight gain is nearly 3.5%. The tablet bed depth can be adjusted so that a larger number of tablets can be more fully exposed to the gun. Increasing the number of spray guns can improve tablet coating uniformity. The coating speed is fast, reducing the time that the medicine is exposed to high temperature and high humidity environment. The most important point is that, because of the airtightness of the material and the WIP system, the HVCC-3015 continuous coating machine can realize automatic cleaning in place, remove drug residues, avoid the direct influence of batches, and help meet the requirements of GMP and realize cleaning. The verification of the process increases the service life of the machine parts.
(3) ConsiGma® Coating Machine From GEA
The device is a revolutionary, high-performance tablet coating technology that precisely controls the amount of coating solution sprayed onto the core, even if the core is hygroscopic or very brittle. Improved heat and mass transfer reduces drying time and increases process efficiency.
The coating quality can be monitored online using the PAT tool. Significant cost savings in production time, materials, downtime, process revalidation, stability testing, etc., compared to traditional systems. Compared to established technologies, the space requirements are smaller, the cleaning effort is less and the floor area can be reduced.
The energy requirements of the ConsiGma® coater are very low, and as a continuous production technology, there is no process scale-up and the maximum batch size is practically unlimited. Currently, two types of ConsiGma® coaters have been launched, a single coating unit and a double coating unit. A single coating unit (see Figure 48) has a coating volume of 6kg in 6min-12min, and a production capacity of 30kg/h. The tablet cores are loaded into a perforated coating pan. Through rapid acceleration, the coating pan reaches a high speed. Under the action of centrifugal force, the tablet cores form an annular tablet bed along the wall of the pan (see Figure 49). The tablet bed, under the action of the radially placed air curtain, forms a stable waterfall (see Figure 50), and the coating liquid is sprayed out in a vertical waterfall, presenting the tablet core into the coating suspension, which is sprayed on on the vertical plane. Drying efficiency is improved by spraying the coating suspension into a waterfall of cores. As a result, the process is much faster, with a target weight gain of 3% in less than 10 minutes, compared to at least 90 minutes in a traditional process. Furthermore, the predictable weight gain and operating conditions obtained through thermal and mass balance ensure more uniform drug color at lower gain weights. Excellent coating thickness uniformity can be achieved even with enteric and extended release formulations.
Figure 11 -ConsiGma®Tablet Coating(TC)Modules
2. Large Drum Replaceable Coater
Thomas company drum replaceable coating machine: the maximum volume can reach 920L, the drum is easy to replace, and the coating weight range is 100kg ~ 700kg, which is suitable for different batch production.
3. Process Parameterized Control
Detection and control of various parameters of the coating process equipment: There are many parameters in the coating process, including dozens of parameters such as temperature, speed, pressure, flow, humidity, air volume, etc. The closed-loop control of parameters can ensure the stability and consistency of coating conditions It can reduce the influence of the outside world on the coating process and ensure the stability of the coating quality.
Automatic detection of equipment status: The coating equipment includes the host, the air supply system, the exhaust and discharge treatment system, the liquid supply system, the cleaning system, the compressed air system, the control system, etc. Alarming the abnormal state of the system, prompting the parts that need maintenance, etc., these are all conducive to improving the integrity rate and working time of the equipment.
4. Digitization And Networking
Digitization, networking, and intelligence are the development trends of equipment, and digitization and networking are the foundation of intelligence. Foreign advanced coating machines generally have a network interface and have the hardware conditions to access the pharmaceutical factory network. The collected and recorded coating process parameters can be uploaded through the network interface of the equipment, and the production instructions can also be downloaded. In this way, the MES system of the workshop can be connected, which is very beneficial to the realization of the ERP system management of the pharmaceutical factory.
-
Automatic Capsule Filling Machine
1. Integral Replaceable Filling Station
The filling station enables quick switching between different products and between different filling methods. Senieer Compacting’s Integral Replaceable Filling Station (see Figure 52) is available in either powder or pellet interchangeable units, allowing the user to choose between a powder filling station and a pellet filling station. The simple overall replacement system allows customers to switch quickly when changing products, greatly reducing replacement and cleaning time. When using an additional pre-assembled filling station, the equipment is ready for production in a very short time.
Figure 12 – Integral replaceable filling station for FEC40 from Fitte Corporation
2. Filling Volume Control
Filling accuracy is the key to high performance capsule filling machines, each capsule must be filled with the same weight of product. This requires a measurement method that operates at high cycle rates without sacrificing performance. The NMC sensor (Net Quality Control) specially developed for the FEC series by Senieer Compacting meets this need. It is based on a non-contact capacitive measurement technique where the electric field measures mass during drug delivery.
Sensor detection frequency up to 140 filling cycles per minute, 100% detection of weight outliers, fully integrated into the machine, no settling time required, not affected by process variations, when using multiple pellet filling stations, the dosage of each pellet can be controlled individually.
3. Diversification Of Filling Materials
In addition to powders and pellets, Hanhui’s capsule filling machines can also fill tablets, microtablets, dry powder inhalants, liquids, and folded film corrosion inhibitors
-
Laboratory Equipment
For the laboratories of pharmaceutical companies and drug research institutions, small-scale solid dosage form equipment is necessary, because generally, scale-up production can only be carried out after the small-scale research is successful. Although this type of equipment is “small”, it has a lot of requirements for operation, multi-function, data acquisition, etc., and has the functions of online data acquisition and analysis. For example, “Mini-Glatt” and ACT150 of German GLATT company are both equipments that meet the requirements of one-step fluidized bed granulation in the laboratory. The output of ACT150 is only 3 kg per hour, and “Mini-Glatt” is even smaller: The STYL’ONE and STYLCAM laboratory tablet press from Klein, Germany, has the functions of single-layer, double-layer, triple-layer and core wrapping. It can simulate the entire tableting process with a small amount of powder, and can automatically execute various Research, as well as clinical and batch production, with throughputs up to 1200 tablets/hour, with high-precision measurements and special software to record critical research data. The above-mentioned laboratory equipment is quite expensive and has high added value, however, such domestically produced products are rarely known.
-
Online Detection Technology
As a pioneering component of cGMP, Process Analytical Technology (PAT) is a part of risk control system, and online detection is a key part of implementing PAT technology. Huanmei developed countries have applied infrared thermal imaging technology, near-infrared spectroscopy technology, laser diffraction technology, X-ray technology, visual analysis technology, microwave resonance technology, etc. to online detection, and the research on online detection technology has gradually covered all Solid preparation process and equipment, however, we are still blank in this regard, and the gap is not small. At present, the online detection of solid preparations includes:
(1) The Insitec online particle size analyzer from Malvern, UK, can measure the particle size, particle shape and particle size distribution of wet and dry methods in real time in the range of 0.1 μm to 1000 μm by laser diffraction technology and record thousands of particle size data in seconds, effectively becoming a pair of alert eyes on the solid dosage production line.
(2) The on-line detection of tablet weight, tablet diameter and thickness, and tablet hardness can be achieved by physical detection methods by companies such as Kreamer in Germany, ERWEKA in Germany and Schleuniger in Switzerland. The detection and analysis data can be fed back to the tablet press.
(3) TVIS-EX3-CD visual inspection system of Japan First Industrial (VISFWLL) and VISITAB2 visual inspection system of French PRODITEC company can realize online inspection of the appearance defects of tablets with a diameter of 5mm to 16mm and a thickness of 2mm to 8mm. The maximum detection volume can reach 300,000 pieces per hour, and the accuracy rate can reach 100%. It is reported that Japan has mandatory regulations for the full inspection of the appearance of tablets.
(4) The KKX3900 hard capsule X-ray inspection device of Bosch, Germany, uses X-ray technology to conduct online inspection of the weight of hard capsules, foreign bodies in the capsule, capsule closure, capsule appearance, etc. The maximum inspection volume can reach 220,000 capsules per hour, accurate rate of 100%.
-
The Importance Of Basic Technology Research
Pharmaceutical machinery companies in developed countries in Europe and the United States attach great importance to the research of pharmaceutical process theory, which contributes to technological innovation and new product research and development, and also provides solutions for pharmaceutical companies. For example, the German GLATT company is a well-known enterprise engaged in granulation, drying and coating. In the early years, the company set up a laboratory led by a doctor of pharmacy, which not only provided strong technical support for the research and development of the company’s own equipment such as granulation, drying and coating, but also proposed solutions and process recipes of the granulation, drying and coating of the pharmaceutical factory.