Home » Turnkey Project
Turnkey Project
Turnkey Project
Turnkey Process
GMP Technical Solution is also called GMP turnkey solution. From land to pharmaceutical factory, health product factory or food product factories. From 0 to 100, user requirements specification (URS) and consultant, design and design confirmation, pharmaceutical machinery and cleanroom solutions products manufacturing, factory acceptance testing ( FAT) and delivery, installation and commissioning at factory site, validation and qualification, etc. Senieer team can support whole process for one stop turnkey solution.
If design the factory and under construction of pharmaceutical company already, Senieer can customize machinery and make turnkey clean room solutions as per your process requirements.
Senieer has been to 41 countries, checking factory sites, giving the best solutions and creating value for its customers.
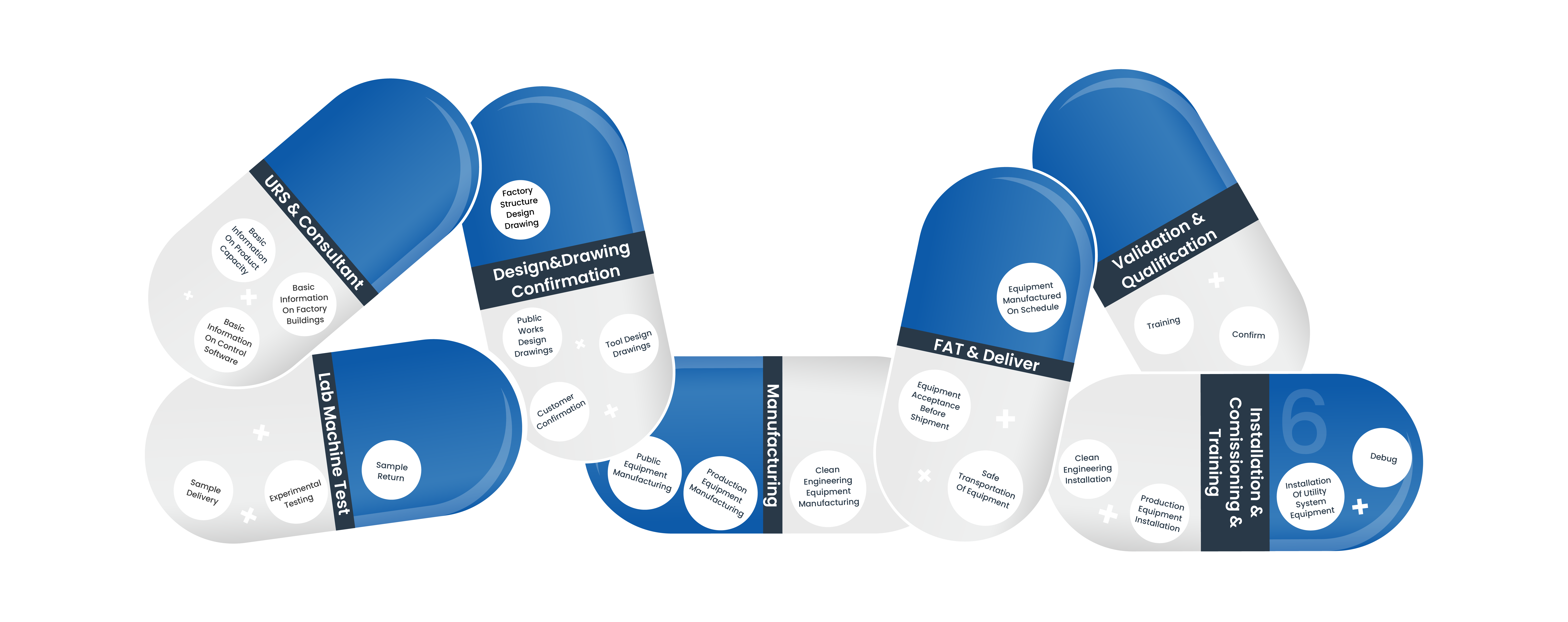
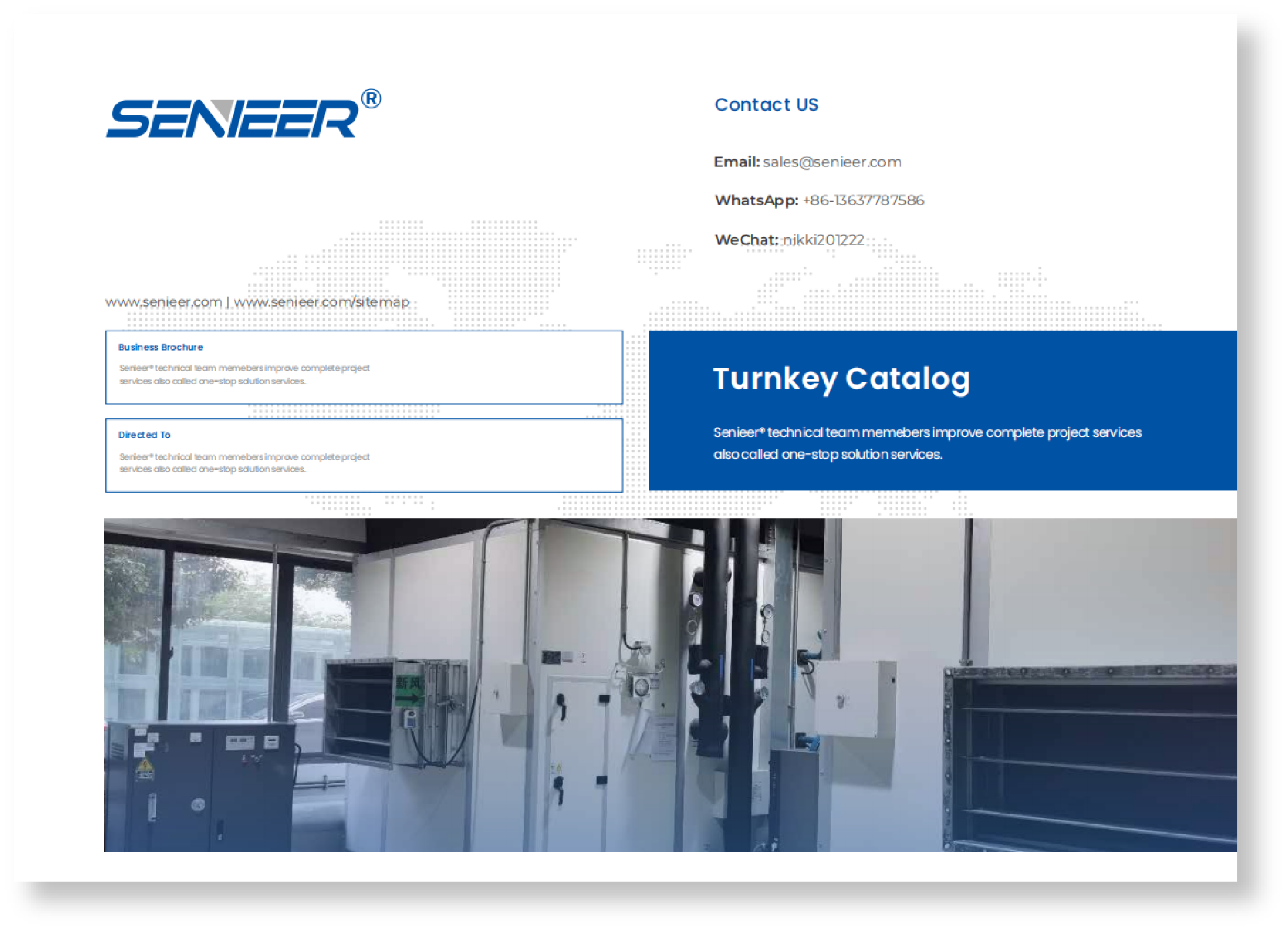
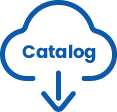
Turnkey Catalog
Granulation line combines both granulation and drying processes to ensure continuous and stable production, it can highly increase the yield of finished products.
The WIP system in the Granulation line can fulfill well cleaning effect for the granulator and dryer.
Guidelines For Production Line
Senieer products cover the whole pharmaceutical production line including solid dosage line, packing line, powder line, liquid filling line, etc. The main part of solid dosage line is granulation line. Granulation line combines both granulation and drying processes to ensure continuous and stable production, it can highly increase the yield of finished products. The packing line includes sachet packing, stick packing and pouch packing, etc.
The following is the GMP Pharma Turnkey Projects Process. Mainly includes: User Requirements Specification & Consultant, Customized design and Confirmation, Manufacturing,, FAT & Delivery, Installation & Commissioning & Training, Validation & Qualification
Turnkey Projects: Pharmaceutical turnkey projects process lines
- Granulation (RMGwet cone mill +Fluid Bed Dryer + bin blender +Dry Mill) + Tablet Press + Tablet Coating Machine + Sorting + Blister Packing + Cartoning
- IBC Mixer (Powderand Granules) + Capsule Filling + Sorting + Blister Packing + Cartoning
- IBC Mixer (Powder and Granules)+Sachet Filling+Cartoning+Weigher
- Granulation (RMGwet cone mill +Fluid Bed Dryer + bin blender +Dry Mill) + Tablet Press + Tablet Coating Machine + Sorting + Bottle Filling + Cartoning + Weigher
- Granulation (RMGwet cone mill +Fluid Bed Dryer + bin blender +Dry Mill) + Capsule Filling + Sorting + Bottle Filling + Cartoning
- Granules, Powder or Pellets for capsule filling
- IBC Mixer (Powderand Granules) +Filling in bottle
Turnkey Projects: User requirements specification & consultant
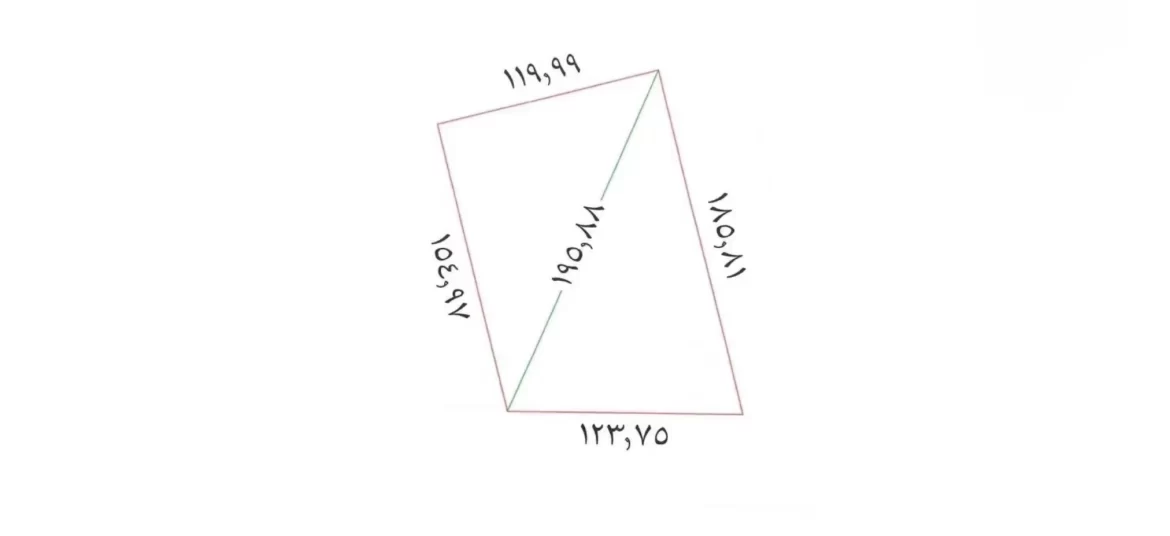
Factory land size provided by customer, 20000 m²( real project)
1. Production area & process line consultant
According to GMP and cGMP requirements, different types of drugs can’t be produced on the same line.
Co-production of similar varieties should undergo relevant verification and obtain approval. There are some factors need to consider:
- According to product’s chemical and biological risks,which products need. to be produced in isolated blocks?
- In order to keep the flexibility of production and adjustment of output. capacity, which dosage form and which type of product need to be set with isolated production block?
- In order to avoid cross contamination, which dosage form and which type. of product need to be set with isolated production block?
- Concerningthe same dosage or element product with different packing size/volume, shall we design it in one line or multiple lines which allow manufacturing of different packing size/volume at the same time?
- Arethere some products which have common elements but with different. dosage? For these products, the primary processing sections-weighing/dispensing is the same.
- Shall we designone primary processing block or multiple, which allow the manufacturing of different dosage at the same time?
Provide the process flow chart for all products. Know process requirements, provide product names, product categories, for example, solid dosage form, powder line, liquid line, etc and target packing line forms required for production.
If the process is oral solid dosage forms, granulation line with packing line, need high shear mixer with fluid bed dryer with vacuum conveyor (transfer product to downstream process) or pharma lifter with bin blender with capsule filling machine or tablet press machine with packing line.
Senieer offers different packing lines:
1. Capsule/tablet bottle filling line
Bottle material and bottle size should be improved. Automatic bottle unscrambler, desiccant inserter, automatic counting machine (8 channels, 16 channels or 32 channels), capping machine, automatic bottle labeling machine. Senieer can custom design as per your needs.
2. Blister packing line
Bilster packing machine with cartoning machine, factors need to consider: tablet shape, tablet size, tablet CAD drawing, blister size and how many pieces of per blister.
Carton size. If it is capsule blister packing, we should know what the capsule size is #000,#00,#0,#1,#2,#3,#4.
If encryption is not involved, the process flows ( flow chart, process description, critical control points points) should be provided.
At this stage, communicate and confirm process with relevant process technology persons. Pharmaceutical equipment service for process, the entire factory is built to realize the process, Clarity of process, dosage form and output is crucial.
2. Production Management Consultant
The step is very important, involving pharmaceutical machinery, model selection and utilities system matching issues. The following questions need to be considered:
- Provide the output capacity for each product
- How many shifts of production every day? What’s the number of personnel for each shift?
- What’s the temperature and humidity requirement for each product’s raw material, packing material’s storing condition? Does it need cold storage? If so, what’s the storage temperature range?
- What’s the temperature and humidity requirement for finished product’s storing condition? Does it need cold storage? If so, what’s the storage temperature range?
- What’s the packing size of the finished product?
What’s the turnover rate for the raw material and finished goods warehouse? Is the turnover rate high or low? This determines how much area to be programmed for the storage.
3 Factory Site Consultant
Provide factory site drawings and photos to show boundaries, neighboring conditions and road conditions. Surrounding utilities system network diagram (water, electricity, compressed air, vacuum source steam, hot water etc.). Is the main entrance and exit location adjustable?
If the factory site is under construction, then please provide the existing construction drawings and pending construction drawings.
- Is there a designated location for the production site? Is the location adjustable?
- Where’s the civil resources connected points: tap water, drainage, power, telecommunication, steam?
- Pls advise the local climate conditions: temperature in winter and summer? Is there any sandy condition?
- Dark Factory need or not?
Turnkey Projects: Customized design and confirmation
After the client clarifies requirements and the consultant carries out design work, the engineering team begins to design the factory. Classify it into different kinds of function areas, comprehensive building which include office and quality inspection, production workshop, warehouse, power center, etc.
Clients check it, if need update, update till satisfaction. From the first step to customized design and design confirmation. After site plan drawings are approved by both parties, construction should be carried out as soon as possible (construction involves concealed engineering construction, and the main building and subsequent reservations should be completed before purification construction.
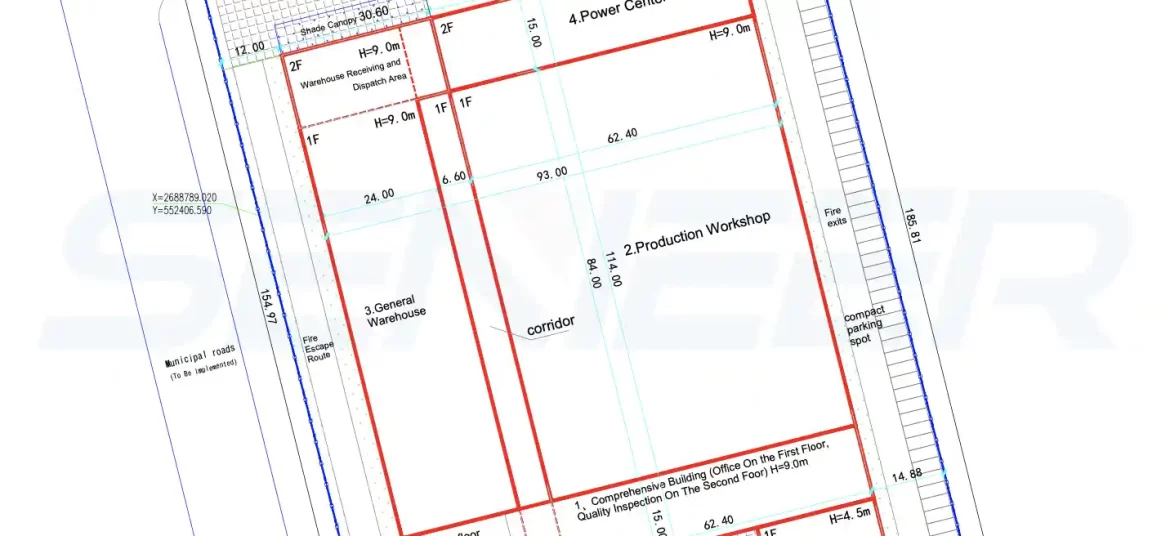
Manufacturing
According to the specific production line which was confirmed in the first step, begin manufacturing equipment, such as cleanroom panel, cleanroom door, cleanroom floor, cleanroom ducting and cleanroom window, etc.
FAT & Delivery
Senieer make Factory acceptance test (FAT) by video or at factory. It will depend on the clients. All products meet FAT, packing and deliver to customer site.
Installation & Commissioning & Training
Senieer after-service teams will guide installation and commissioning or installation and commissioning at factory workshop. During this process, your engineering team members follow us. Our experienced engineers will guide and train a lot of knowledge. It is a benefit for clients. After installation and commissioning, focus one period for training production operators and maintenance engineers.
Validation & Qualification
We will support validation documents, such as DQ, IQ, OQ, Manual, etc. Clients can pass GMP, FDA (if you require, let us know in advance).
If you are looking for GMP turnkey solutions, Senieer is the right choice.