Vacuum Powder Transfer System
Suitable for facilitating maximum transfer of the powder materials. This is exactly what you stand to gain from our vacuum powder transfer system. Built of high quality materials hence can last for long. The ergonomic design enhance the usability of the equipment.
Vacuum Powder Transfer System : Product Description
Senieer powder transfer system is also known as powder vacuum conveyor. It uses the vacuum to transport or convey powder materials in the manufacturing process. The system does not dead-end to ensure a smooth transfer and delivery of the materials. The vacuum powder transfer system has a wide range of applications in different industries.
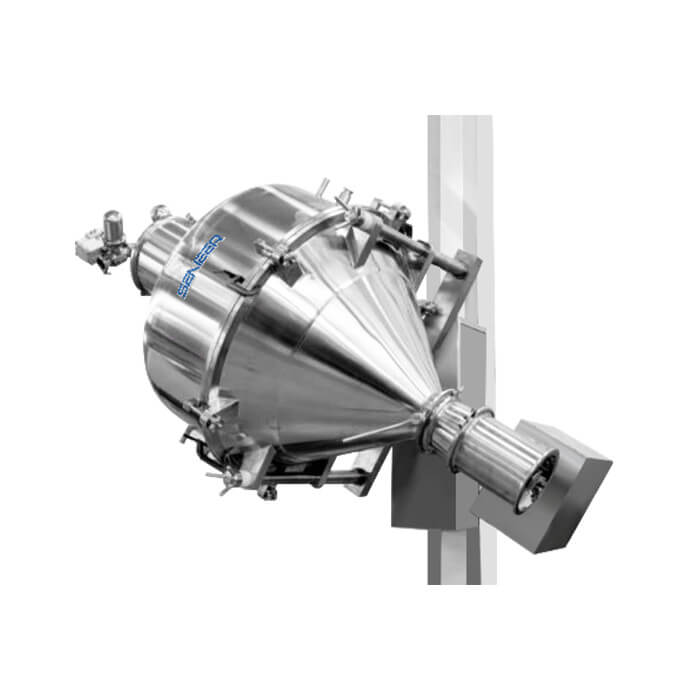
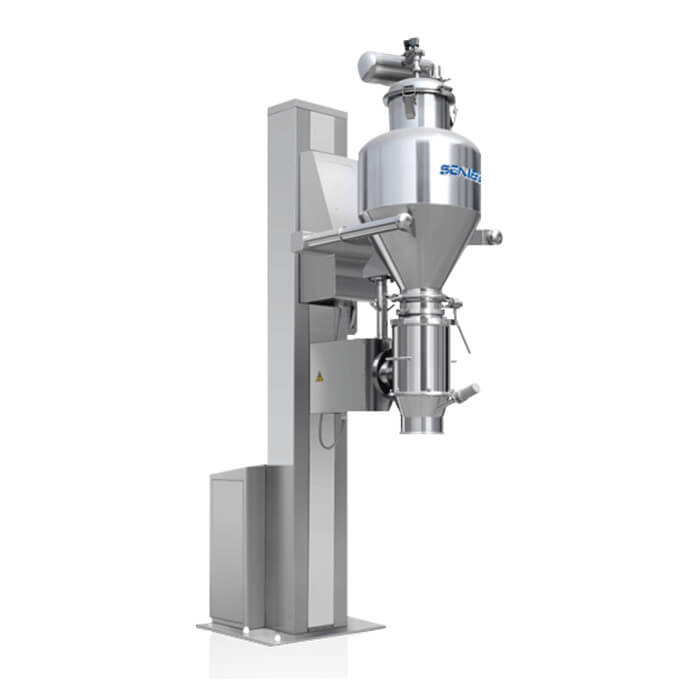
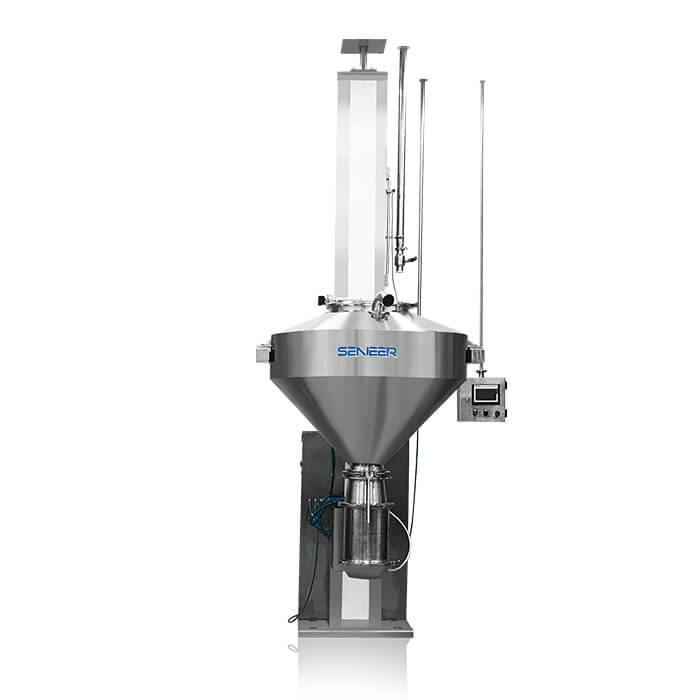
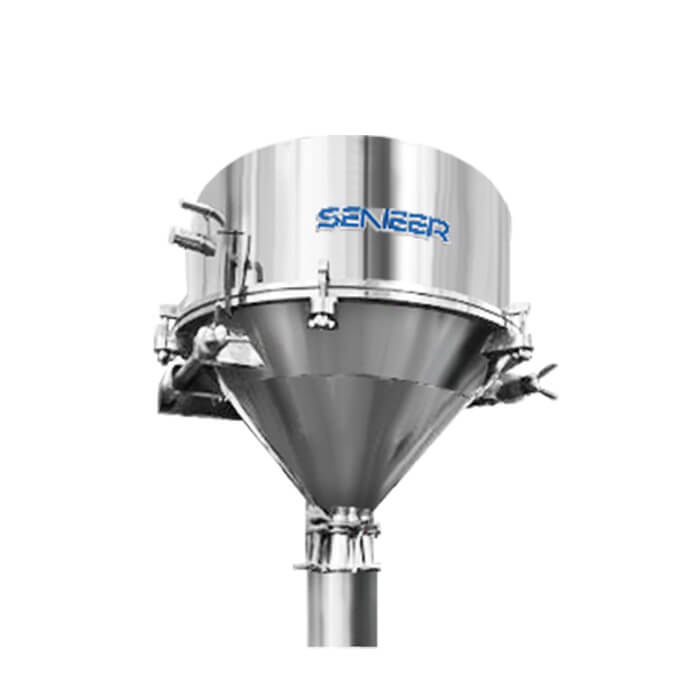
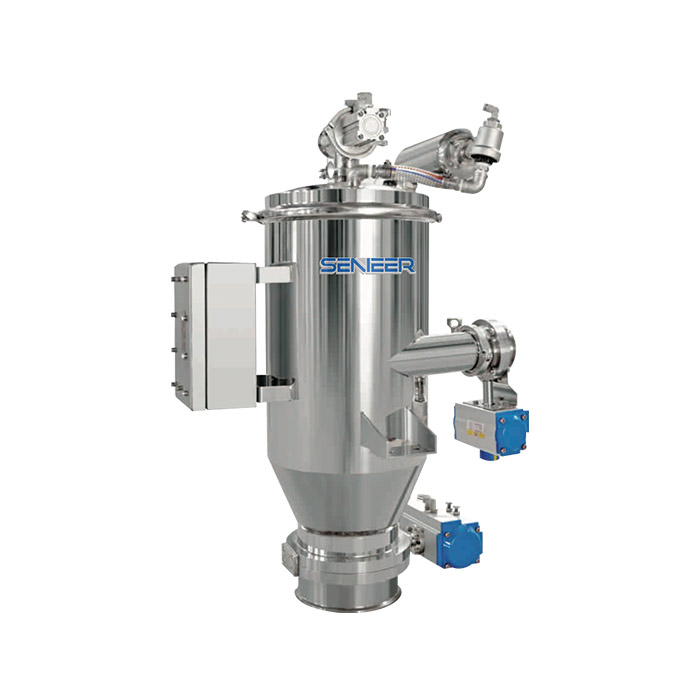
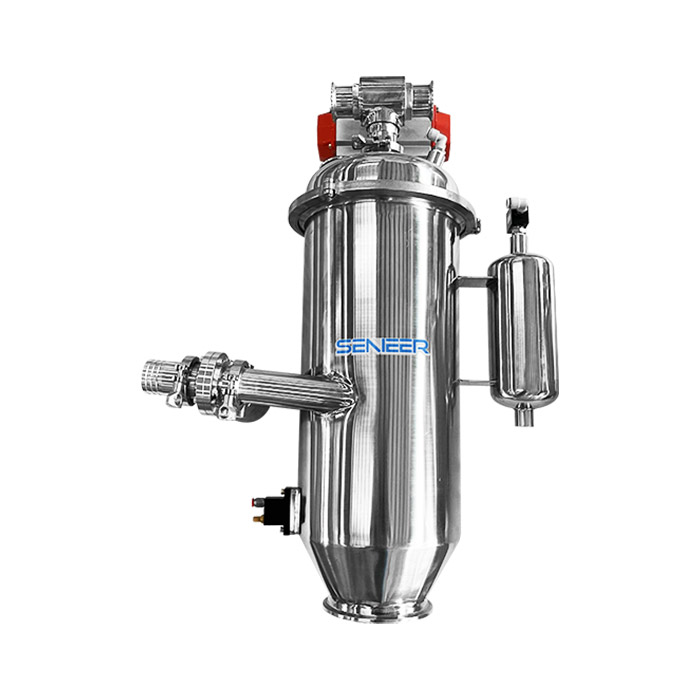
Details of Vacuum Powder Transfer System
- Stainless steel materials: The body of the system is made of high-grade stainless steel metal. This guarantees the strength and durability of the system. Our vacuum powder transfer system is rust-resistant and easy to clean.
- Different Capacity: The vacuum powder transfer system is designed to suit both small and large production requirements. We manufacture vacuum powder transfer systems with a capacity of up 10t/h vacuum suction. The vacuum powder transfer systems are ideal for small, medium, and large-scale manufacturing projects across the globe. You can also request a customized vacuum transfer system. The size of this system will be customized according to your requirements.
- Speed: A vacuum powder transfer system can be easily configured to suit a certain application. You can configure a vacuum rayon suction system as per your requirement. This ensures easy control over vacuum flow rates and hence improved efficiency levels during operation.
- Simple Design: Our vacuum powder transfer system comes in standard or customized designs that meet different needs. Each part of our vacuum powder transfer system is tailor-made to fit the specific design you require for your manufacturing project.
- Adjustable Vacuum levels: vacuum powder transfer systems are vacuumed to a specific vacuum level. This vacuum level is maintained by the vacuum controller module. The vacuum controller adjusts the flow rate of air as it passes through the vacuum channel to ensure optimum vacuum levels in various parts of the vacuum powder transfer system.
- Optimum Performance: Our vacuum powder transfer systems maintain high performance and efficiency across all operating conditions. You can be sure that you won’t experience any downtime with our vacuum powder transfer system in operation. The suction pressure remains stable during operations despite different fluctuations in humidity, temperature, and air pressure levels from the outside environment.
- Designed for safety: Our vacuum powder transfer systems are designed with safety measures to ensure the protection of operators and also the vacuum powder transfer system itself. The vacuum controller module has built-in safety features to prevent any vacuum fluctuations during operation.
Senieer vacuum powder transfer system is used in different industries. They include pharmaceuticals, food processing, chemical processing, cosmetic companies, detergent manufacturers, ceramic manufacturers among others. As long as your products entail the transportation of powder, you will find this equipment useful.
- Simple and stable design
- Customized to meet your production needs
- PLC control system
- High energy efficiency
- Minimum noise when in operation
- Can be used on different powder materials
More Models of Vacuum Powder Transfer System
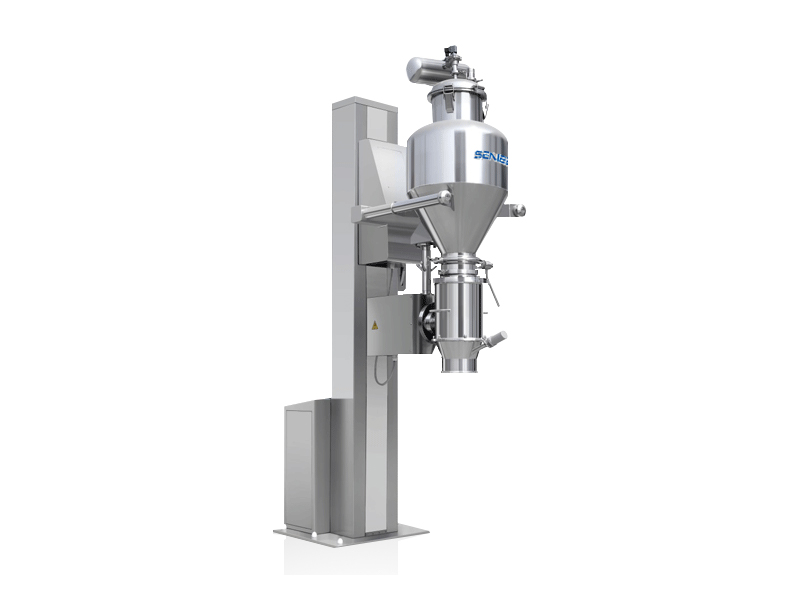
LVM1000 Vacuum powder conveyor with cone mill
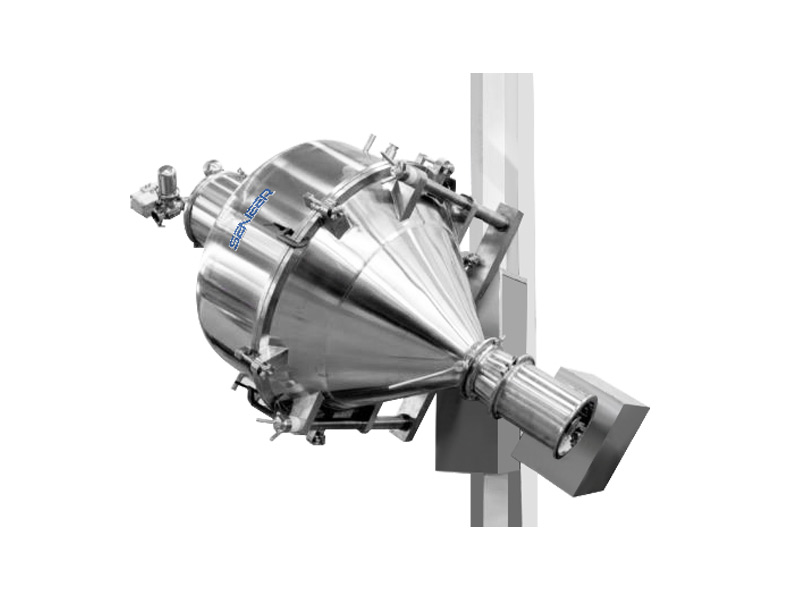
LVM800 Vacuum powder conveyor with cone mill
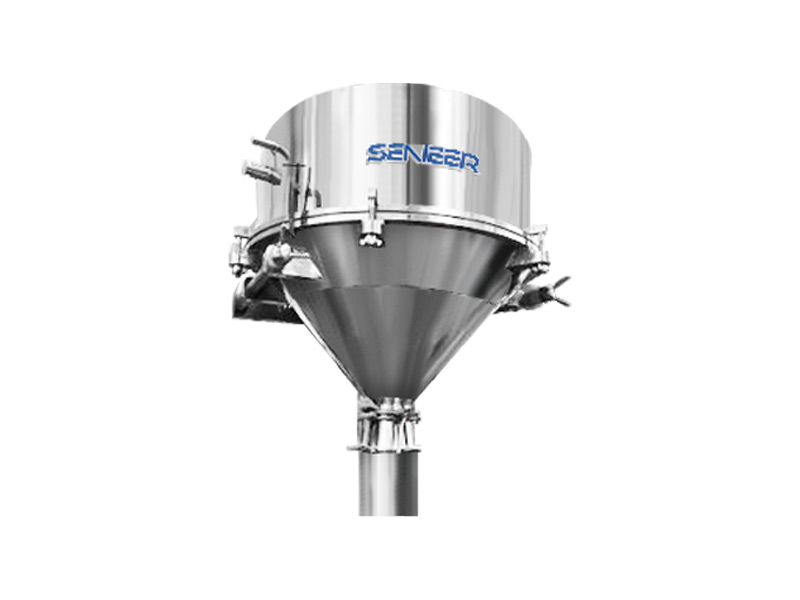
LVM600 Vacuum Mill Cum Sifter
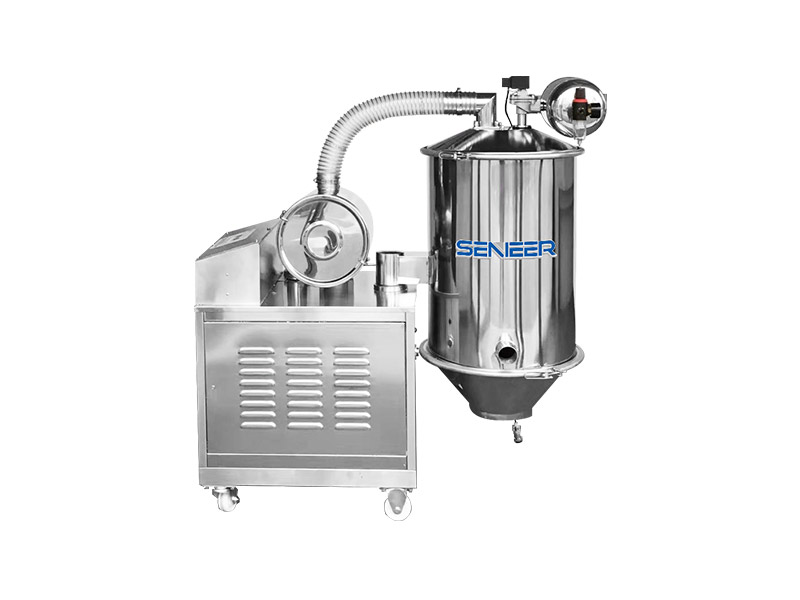
LVM400 Vacuum powder conveyor with cone mill
Any Question About Senieer Vacuum Powder Transfer System
Why Global Company Trust Senieer
Top Quality Factory Price
We have a quality control department to verify each product at different phases, from the procurement of parts to finished products
As Your Layout, Customize Machine
According to your layout, we can suggest the best capacity and type for you, customize equipment for you
Equipment Consult & Design Service
Save energy resource for you, professional engineers can improve the best processing solution. We have the experience to help add a tremendous amount of value to your project
ISO.CE Standard Qualified
We successfully obtaining the ISO9001:2008 certificate and CE security management system certificate, this is significant for Senieer in building enterprise image
Equipment Training & Maintance Service
Free Equipment training & maintenance service for you, we will provide your team in-depth training on safe operation and equipment maintenance
Equipment Installation Service
Senieer offers equipment installation & commissioning service for production products, your equipment and control systems are qualified based on the GAMP life-cycle
Pharmaceutical Bin Ultimate Buying Guide for Importers
Let’s dive right in:
- Chapter 1: What is a vacuum powder transfer system?
- Chapter 2: How does the vacuum powder transfer system work?
- Chapter 3: Design considerations of vacuum powder transfer system
- Chapter 4: Benefits of vacuum powder transfer system
- Chapter 5: Parts of Vacuum Transfer System and their Functions
- Chapter 6: Vacuum Powder Transfer System Technical Specifications
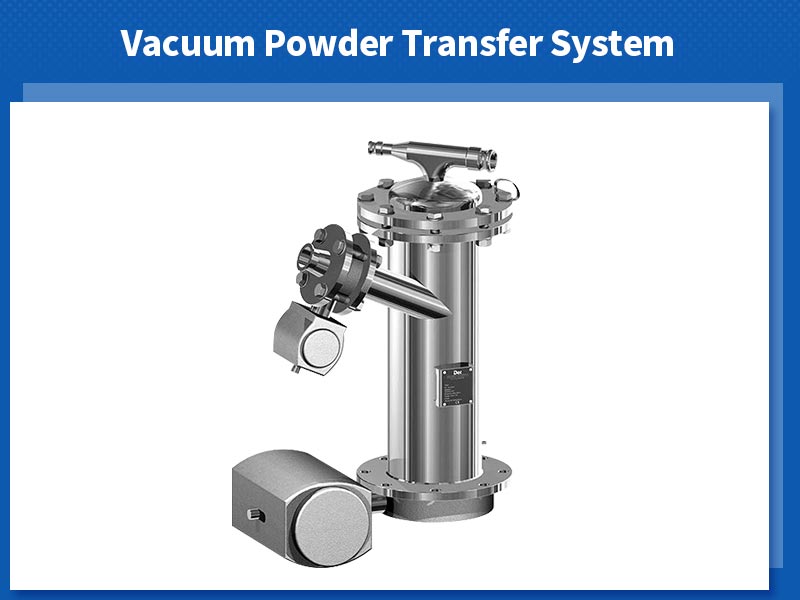
Chapter 1: What is a vacuum powder transfer system?
This is a system that utilizes a vacuum to facilitate the transfer of powder vertically and horizontally to the desired target. It can be to the machinery or the storage unit.
These vacuum powder transfer systems may be used in industrial settings, such as vacuum conveying of powder on the production line. It is also used for the transportation of goods because a vacuum permits very little friction between its surface and that of other objects.
Chapter 2: How does the vacuum powder transfer system work?
The vacuum powder transfer system is a vacuum conveyor which moves granular powders or fine, loose, and free-flowing materials through a vacuum in closed pipe lines.
To understand how the vacuum works with powders, we need to discuss two different types of vacuum:
Present vacuum
The level of vacuum that can be produced by a vacuum pump. This type of vacuum only affects loose particles weighing less than 0.2 grams each and forces them to move toward the region of highest pressure (i.e., the vacuum source).
In other words, the present vacuum would remove as much air from between particles as possible but will not remove air from inside individual particles. For example, if there is an obstruction in the line or on top of the powder surface then it will remove air from around the obstruction but will not vacuum inside of it.
Path vacuum
The vacuum created by the vacuum pump on one end of an enclosed pipeline transfers to the other end of the pipe and, as particles pass through, are pulled toward that vacuum.
This vacuum is also known as a ‘path’ vacuum because it is created by passing a small amount of gas or air (known as the carrier) through a pressurized pipe which is attached to another larger or main (vacuum) pipe.
As this carrier travels along its path, it pulls behind it all other gas in the system including any present vacuum caused by obstructions such as elbows.
This means at any given time there is less gas pressure in front of the vacuum carrier and more behind it. This vacuum pressure differential continuously pulls the particles along as they move down the pipe line.
Working mechanism
As a vacuum powder transfer system uses vacuum to create a smooth flowing vacuum conveyed flow of materials that can carry heavier material loads than conventional suction or gravity fed systems.
The first vacuum is created by a vacuum pump which creates a present vacuum over the total length of pipe required for conveying process. The second vacuum is created during transport from one end to another end of the pipe line through an enclosed pipe line (pipe & fittings).
The transfer is effected using nonvolatile gas like Nitrogen or Argon which will pull any other atmospheric gases (air) inside the particle surface because of density difference.
Sectional vacuum powder conveyors consist of multiple vacuum tanks known as vacuum chambers. These chambers are arranged in either a straight or serpentine configuration having different lengths & diameter pipes to achieve desired vacuum level. The arrangement provides ideal conditions for vacuum transfer.
Each vacuum chamber consists of a single vacuum tank with an internal pump and valve system, exit point, and interconnecting pipe lines with individual vacuum tanks.
This design and arrangement of the chambers allow continuous operation by automatic switching on/off mode for all pumping units based on the need to achieve higher efficiency over the entire system.
In this way, only those pumps required to maintain vacuum level are running & as the vacuum transfer process progress, the vacuum pumps required for the next vacuum chamber will come on.
This will helps in reducing the energy consumption up to 30% as compared with conventional vacuum systems that use only a single vacuum pump for the entire system’s operation.
The entire vacuum transfer system is controlled by PLC based controller unit which connects directly to each tank through a dedicated control panel & valves that can be operated via external switches or sensors.
Power supply
The main source of energy in the vacuum process is the vacuum pump that pulls air from within the vacuum path to create the vacuum level required for vacuum conveyed material’s movement. The excess power consumed is due to friction loss inside the vacuum piping system, vacuum chambers, and interconnecting pipelines.
Vacuum powder transfer devices are consisting of multiple vacuum chambers and interconnected pipes & fittings. Each vacuum chamber will be provided with an individual permanent vacuum pump so that it can maintain preset vacuum levels at needed points of time.
Chapter 3: Design considerations of vacuum powder transfer system
One of the key features of the vacuum powder transfer system is the design. Manufacturers must ensure that the design of the system enhances its efficiency and performance.
Vacuum powder transfer system design features take care of an array of issues, all of which are connected to the performance efficiency and suitability of the vacuum powder conveyor.
That is, the Vacuum Powder Transfer System should be able to handle abrasive powders with particle sizes from 100 micrometers upwards and one of the significant challenges in designing such systems is the prevention of blockages.
These can occur due to the natural build-up of material in corners inside pipework or in other areas. Blocked Vacuum powder transfer Systems severely limit its efficiency making it unable to effectively handle increasingly large amounts of product at a time. This then creates a danger for people working around the Vacuum Powder Transfer system that runs on compressed air.
Another critical issue that vacuum powder transfer system designers is how to prevent dust from leaving the system. This is especially common during discharge operations this is due to the high amount of energy created and flowing through the Vacuum Powder Transfer System after being compressed.
The design must also enhance the ease of using the machine so that the vacuum powder conveying is easily specified and installed. The vacuum powder transfer system design must also be easy to clean and maintain with low maintenance costs.
The Vacuum Powder transfer system must be designed using an in-depth study of the powder being handled as well as other considerations such as:
Powder pumps are usually used in vacuum powder transfer systems to transport the product from one place to another. Vacuum powder transfer system design must consider different ways of using powder pumps such as dusting, conveying, or delivering the product at a rate that meets the fundamental rule for consistent transfer operations.
The cleaning process is important in a vacuum powder transfer system and it should be designed in such a way that it minimizes contamination risk when handling different types of products being transferred through the vacuum powder transfer system.
The vacuum powder conveying system design should also take care of the safety of the users and operators. Vacuum powder transfer system design must consider Vacuum Powder Transfer hazards that may be present at the Vacuum Powder transfer system site.
Integration with other equipment and accessories
The design should also promote easy connection or integration with other equipment. The vacuum system design must consider the vacuum powder transfer system installation and integration with other systems that may be in use such as ventilation, dust collection, explosion-proof lighting, and any other safety precautions that may be needed.
Vacuum powder transport system design should also conform to applicable standards in each country [such as ISO 2859-1:2015, FDA, cGMP among others. The standards usually specify the design requirements for the vacuum conveyor.
You can also get custom designs for vacuum powder transfer systems. Here, the manufacturer will customize the design of the system according to your needs. Vacuum powder transfer System manufacturers will help you get the best Vacuum Powder transfer system that fits your requirements and works efficiently.
Chapter 4: Benefits of vacuum powder transfer system
Are you planning to buy a vacuum pneumatic conveying system? Here are some of the key benefits of using this system.
Faster transfer of powder
When you use a vacuum powder transfer system, you will be able to get your powder from one place to another efficiently in a short period.
Compared with pneumatic conveying systems that use pressure as the main driving force for transferring material, vacuum takes less time to get things going. This will lead to a fast production process
Less power consumption
The fact that air is not anymore needed to drive the conveying system leads to reduced power consumption and thus increased efficiency of your production line.
Low power consumption also means that you will cut won on the expenses of running the business.
More compact design
The dependence on air lessens the need for large-scale installations, so you will be able to use this vacuum powder transfer system even in limited spaces with ease.
This means that your plant or building will be more efficient in terms of space utilization. The equipment will easily fit into your compact space.
Metal construction
Consider getting yourself stainless steel, aluminum, or copper vacuum pneumatic conveying systems because they will last longer and you won’t have to worry about corrosion issues as compared with other materials such as plastic or carbon fiber.
Furthermore, if you get yourself a metal vacuum powder transfer system, it can easily withstand the high-pressure air inside while keeping the fumes outside the chamber. This means that your risks of having dust contamination will be minimized.
Minimal loss of powder
This vacuum pneumatic conveying system must contain the least amount of loss possible, even if it is only a small one.
Several factors affect this such as dead corners and sharp turns that usually cause powder transfer to not be done smoothly. Therefore, make sure that you choose a vacuum powder transfer system with minimal curves or corners to get the smoothest powder movement.
Minimized contamination risk
Always opt for an oven-dried vacuum pneumatic conveying system instead of those that are ready to use. This is because it would give you fewer risks of having contaminations in your powders due to moisture build-up inside them. This would also save energy since the drier they are, the less energy you need to run them.
Low maintenance requirements
There is no doubt that vacuum pneumatic conveying systems require minimal maintenance costs and schedules. However, for you to maintain their optimum performance, you should do regular maintenance on this equipment.
Can be used with different materials
A vacuum transfer system can be used for the transfer of different materials regardless of their physical and chemical properties.
This means that it is one of the best ways for you to ensure that your production is heightened in terms of efficiency.
Wide range of applications
The best vacuum powder transfer system can easily fit into different industries. While some are made for chemical or pharmaceutical production lines, some of these vacuum powder transfer systems can also be used in the food and beverage industry.
Indeed, vacuum conveying is a popular industrial process known for its efficiency and flexibility. Hence, if you want to ensure greater productivity in your factory, then consider getting yourself a vacuum pneumatic conveying system today.
Chapter 5: Parts of Vacuum Transfer System and their Functions
A vacuum powder transfer system comprises of different parts and components. Each part has a special role that it plays for the whole system to function perfectly. Let’s look at each part and the role that it plays.
Suction device
The suction device is responsible for blowing a vacuum in the system. It comprises one or more blowers that blow the air out from the system and create negative pressure. The suction device ensures that there is no accumulation of powder in between two points.
The suction fans are fixed at different locations determined by their operational requirements like reduced temperature, the flow of product among others.
Vacuum pump
Vacuum pumps are used to generate a vacuum in the system. Vacuum pressure controls the rate at which solids and water vapor leaves a product or dry solid matter leaving it behind due to low moisture content.
A vacuum pump produces a negative pressure to suck up powders from the storage container to transfer into a final container where it’s ready to be used.
A vacuum pump comprises of shell side where tubes are installed internally through which vapors pass from the bottom upwards towards the top end of the shell.
The fluid passes out to different points like a purifier, boiler, evaporator via distributors at the base end depending on the required setpoint value feeding back to the process.
Material Discharge
The vacuum powder transfer system uses a material discharge unit to throw out materials that are positioned in the retainer. This is usually installed on multi-component dispensing systems.
Material level sensor
The main function of this component is to sense the level of material in the hopper. This will keep the system from overfilling and cause a spill around the mixing vessel. Many systems can be used to sense the level of material, air-float systems, water buoyancy sensors, etc.
Powder Inlet
The powdered substance is added to the vacuum system through this element. It also keeps an eye on the powder flow rate for the best performance.
Material Mixer:
The rotating disc inside the mixing bowl revolves at high RPMs for effective mixing of materials without producing any lumps or cracks. The mixer ensures that all the particles that make up the powder are uniformly shaped and sized for easy transportation.
Storage Containers
These storage vessels store bulk quantities of powder until the vacuum powder transfer system is used to suck them up. The storage tank has a lid that keeps it from spilling any powder during transportation.
PLC Control system:
PLC control systems are used to automate the process of vacuum powder transfer and ensure that it’s done correctly. The control system determines various variables such as pressure and vacuum level to create a system that functions properly. They affect the overall operation and performance of the powder transfer system.
Chapter 6: Vacuum Powder Transfer System Technical Specifications
There are several technical specifications that you should know when buying a vacuum powder transfer system. These specs determine the overall performance of the powder conveying system.
Some of the key technical specifications that you should know include:
*Conveying distance: This is the total distance that the powder is expected to cover in the vacuum powder transfer system. This distance is usually measured in meters.
The longer the conveying distance, the higher will be the pumping rate required; a higher pumping rate will translate to higher energy consumption by the pump manufacturer. Due to this reason, you should know how long the powder will need to be conveyed before buying a vacuum powder transfer system.
When looking for a vacuum system supplier, make sure that they specify this technical specification so that you can have an idea of how much energy your powder handling systems are going to consume and decide whether it’s worth investing in them or not.
*Pumping speed: The maximum amount of dry material that can be pumped through a vacuum system within any given period is known as its pumping speed. In other words, it is the maximum amount of material that can be transferred per unit of time.
Usually, this spec is given in terms of kilograms or pounds; larger systems are capable of handling more weight than smaller ones.
*Pumping capacity: The total amount of dry material that a vacuum system can transport through it within any given amount of time is known as its pumping capacity. In other words, it refers to the total amount of material that can be transported by a powder conveying machine.
The greater the piping area (which also increases pumping speed), the higher will be the overall pumping capacity. On average, 1 tonne/hr (1000 kg/h) may suffice for small-scale industrial applications while several tonnes/hour should be considered for large-scale industrial applications.
*Installation requirements: Powder vacuum systems usually come with their own specific installation and maintenance requirements that need to be considered before setting up a powder conveying system. These specifications include the selection of piping materials, testing and commissioning procedures as well as maintenance guidelines.
Headroom requirements
The headroom required for a vacuum conveying system is defined as the vertical distance between the center of gravity of its container and its cover plate. It essentially indicates how much clearance should be left above the machine, so that it can run smoothly.
Headroom requirements vary depending on the type of powder handling machinery used in it; you should look for a vacuum conveying system with enough headroom to ensure smooth operation in your industry.
Piping materials
Vacuum powder transfer systems usually come with one or more piping components made out of different materials such as steel, stainless steel, aluminum, etc.
Sometimes they are manufactured directly from special plastics known as thermoplastics or thermosets, which are capable of being processed at very high temperatures without losing their properties and strength.
These piping materials also vary in terms of resistance to both heat (thermal) and cold (cryogenic), i.e. they can work well at room temperature as well as at very low temperatures such as -184 degrees Celsius (-300 degrees Fahrenheit).
Would you like to have a customized vacuum powder transfer system? It is recommended that you submit these technical specifications to potential vacuum system suppliers so that they can quote accordingly.
This will ensure that your investment in a vacuum powder transfer system is worthwhile in the long term.
Vacuum powder transfer system
From this guide, it is clear that a vacuum powder transfer system is a piece of essential equipment that you should incorporate into your business or organization.
If you are seeking to buy the best vacuum powder transfer system, then you should consider getting from a reliable vacuum powder transfer system manufacturer in China. This is the surest way of getting quality equipment at the best price.
At Senieer, we offer a vacuum powder transfer system at affordable prices. We have been manufacturing and supplying the machines globally for several years and our products are preferred by many.